Comprehensive Analysis of Brass Alloy: Properties & Applications
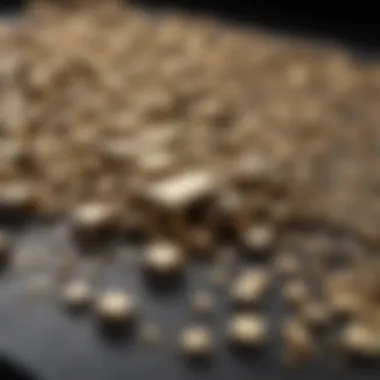
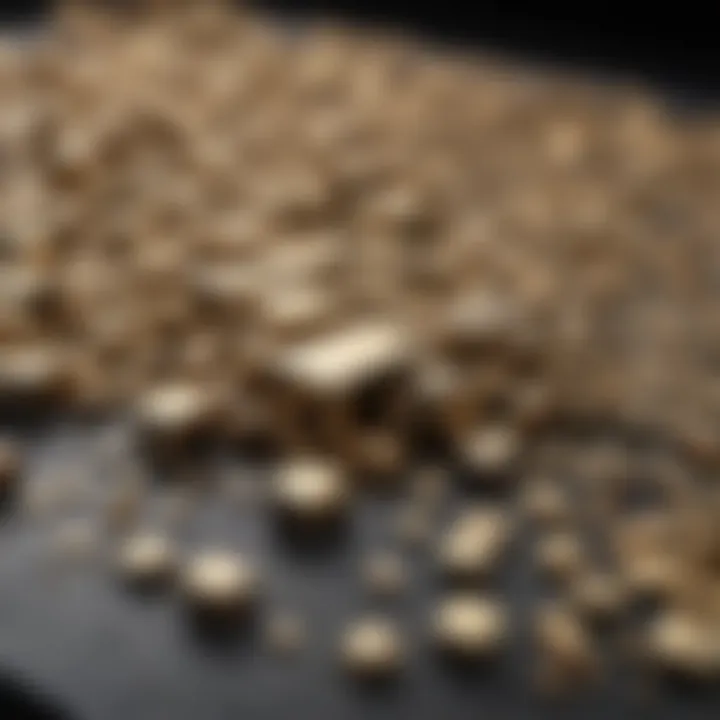
Intro
Brass alloy is a versatile and widely used material in multiple industries. It consists mainly of copper and zinc, with the proportions determining its specific grade and characteristics. Beyond just composition, the properties of brass lead to its use in various applications, ranging from musical instruments to plumbing fixtures, electrical components, and decorative items. The significance of brass alloy cannot be overstated; it plays a crucial role in manufacturing processes owing to its favorable mechanical and physical properties.
In this analysis, we will dissect various aspects of brass alloy, including its chemical composition, the unique properties that arise from it, and the intricate manufacturing processes involved. Additionally, we will delve into the different applications it serves and highlight innovations affecting its usage in modern industries.
Understanding brass alloy is vital for students, researchers, and professionals in materials science and engineering. The exploration here aims to provide not only technical insights but also a platform for exploring challenges and advancements within this essential alloy.
Research Overview
Summary of Key Findings
Brass alloys are distinguished by their unique chemical composition and varied characteristics, making them suitable for different uses. Key findings of this analysis will cover the following points:
- The specific compositions of various brass grades.
- Mechanical properties such as strength, ductility, and corrosion resistance.
- The environmental impact and recycling potential of brass alloys.
- Innovations in brass manufacturing techniques, emphasizing efficiency and sustainability.
Significance of Research
This research is significant as it provides a comprehensive overview of brass alloys, illustrating the scientific principles that govern its functionalities. Assessing the challenges and innovations brings forth a deeper understanding, aiding those engaged in related fields to make informed decisions regarding material selection and application.
Methodology
Research Design
The research undertaken for this analysis is structured to include a thorough examination of available literature, including academic papers, articles, and industry reports concerning brass alloys.
Data Collection Methods
Data has been collected from multiple reputable sources. The sources considered include:
- Wikipedia: For general information about brass alloys (https://en.wikipedia.org/wiki/Brass).
- Britannica: For historical significance and definitions (https://www.britannica.com/science/brass).
- Reddit: For discussions and modern applications (https://www.reddit.com/r/engineering/).
"Understanding the various types and properties of brass alloys allows for better performance in practical applications and contributes to innovations in material science."
The information collected helps elucidate the complex nature of brass alloys, supporting both theoretical and practical insights.
By laying this foundation, we will continue to explore the composition, properties, manufacturing processes, and applications of brass alloy in the following sections.
Prelims to Brass Alloy
Brass alloys are significant materials that find use across diverse industries due to their unique properties. Understanding brass alloys is essential for those engaged in materials science and engineering. This section sets the foundation for the exploration of brass alloys, detailing their definition, composition, and historical context. It is not only a matter of academic interest but also practical relevance in both manufacturing and everyday applications.
Definition and Composition
Brass is primarily an alloy made of copper and zinc. The proportion of these two metals can vary, resulting in different types of brass with unique characteristics. Generally, copper makes up about 55% to 90% of the alloy, while zinc accounts for the remainder. The composition affects properties such as strength, ductility, and corrosion resistance.
Besides copper and zinc, brass can contain small amounts of other elements like lead, tin, and iron. These additions can enhance specific attributes. For instance, lead improves machinability, while tin enhances corrosion resistance. The ability to tailor the composition allows engineers to create brass alloys suitable for various applications ranging from decorative items to critical components in machinery.
Historical Context
Brass has a rich history dating back thousands of years. The first known use of brass alloys can be traced to ancient civilizations, particularly in Asia Minor around the 5th century BC. Artisans discovered that combining copper with zinc produced a metal with appealing characteristics, opening opportunities for various applications.
In the early years, brass was mainly used for ornamental purposes, including coins and jewelry. The Industrial Revolution marked a turning point, expanding brass application into tools, electrical components, and plumbing fixtures. The development of new manufacturing processes significantly improved the quality and availability of brass alloys. Today, the understanding of brass alloys continues to evolve through ongoing research and innovation, making them relevant in modern material science.
Chemical Properties of Brass Alloy
Understanding the chemical properties of brass alloy is crucial for its application and functionality in various industries. These properties dictate not only how brass performs under different conditions but also how it can be engineered for specific uses. Thus, examining its chemical characteristics can lead to enhanced material performance and reduced failure rates in practical applications.
Composition Variations
The composition of brass alloy typically includes copper and zinc, but variations exist depending on the intended application. The ratio of these metals can drastically influence the alloy's chemical properties. For instance, a high copper content results in better corrosion resistance and enhanced thermal conductivity, while increasing zinc content can improve the alloy's strength.
Other elements such as lead, tin, or aluminum may be added to brass to enhance specific properties.
- Lead is included for improved machinability.
- Tin is effective in enhancing corrosion resistance.
- Aluminium improves strength and can help in reducing the density of the alloy.
The careful selection of these constituent elements is essential, as it directly impacts factors like malleability, durability, and resistance to various environmental conditions.
Corrosion Resistance
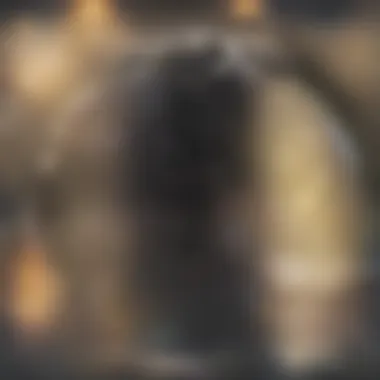
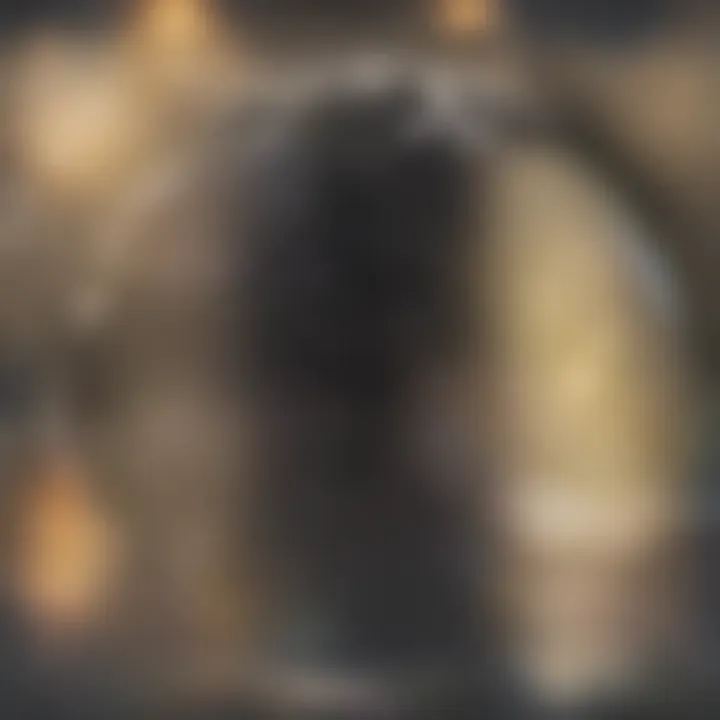
Corrosion is a significant concern in many applications involving brass alloy. The resistance to corrosion is influenced by its composition and the environment it is exposed to. Brass alloys with higher copper content are generally more resistant to corrosion. This is particularly valuable in applications such as plumbing fixtures and marine components where exposure to moisture is inevitable.
However, zinc can leach out in certain corrosive environments, often leading to a reduction in mechanical properties. This phenomenon is known as dezincification. To avoid this problem, engineers often select specific brass types that exhibit better corrosion resistance. To summarize, enhancing the corrosion resistance of brass alloys not only extends the life of the materials but also ensures reliability and safety in their applications.
Mechanical Strength
Mechanical strength is another vital property of brass alloys. This includes attributes like tensile strength, yield strength, and hardness. The mechanical properties are significantly affected by composition, processing techniques, and even temperature changes.
Brass alloys can be engineered to achieve specific strength characteristics:
- Alpha brass has a somewhat softer nature but excellent ductility. It is suitable for applications where deformation is required.
- Beta brass, on the other hand, generally displays high strength and can be used in more demanding stress applications.
Optimizing the mechanical strength of brass is essential for ensuring that components can withstand operational stresses without failure.
"Understanding the chemical properties of brass alloy not only informs its application but also empowers engineers and manufacturers to innovate in their designs."
In summary, the chemical properties of brass alloy, including composition variations, corrosion resistance, and mechanical strength, are pivotal for its successful application across many sectors. This includes industries such as construction, automotive, and electronics, where reliability and performance are non-negotiable.
Types of Brass Alloys
Understanding the various types of brass alloys is crucial for comprehending their applications and properties in different fields. Each type of brass alloy offers specific advantages and has distinct characteristics, which makes them suitable for various industrial uses. This section dives into three primary varieties: Alpha Brass, Beta Brass, and Gilding Metal. The significance lies not only in their differences but also in how these characteristics affect performance in practical situations.
Alpha Brass
Alpha brass is a category of brass alloy that primarily consists of copper and zinc, with a zinc content typically below 35%. It is known for its excellent ductility and good corrosion resistance. The lower zinc content allows for a higher level of malleability, making it easier to work with in various manufacturing processes. Thus, alpha brass is widely used in applications like plumbing fittings and electrical contacts where formability is crucial.
The metallurgical structure of alpha brass contributes to its mechanical properties. The face-centered cubic crystal structure enhances its strength and ductility. This allows for better performance under stress compared to other alloys. Additionally, alpha brass maintains its appearance when exposed to environmental factors, which is essential for aesthetic applications.
Beta Brass
In contrast, beta brass has a higher zinc content, generally ranging from 35% to 45%. This composition provides different mechanical characteristics. However, the increased zinc content tends to lower the ductility, which can present challenges during machining and forming processes. Beta brass alloys are particularly notable for their high strength and hardness, making them suitable for applications that require robust materials, like marine fittings and certain types of fasteners.
Beta brass can also suffer from stress corrosion cracking in certain environments, so engineers must consider this property when using it in specific situations. The alloy's behavior under different temperatures and environments is crucial for performance in long-term applications.
Gilding Metal
Gilding Metal is another type of brass alloy, characterized primarily by its high copper content, usually around 90% copper and 10% zinc. This alloy is valued for its appearance, closely resembling gold due to its color and sheen. It is often used in decorative applications and jewelry. Moreover, gilding metal offers enhanced resistance to tarnishing, making it suitable for items that require a lasting finish.
The softness of gilding metal also aids in the ease of fabrication, allowing it to be artistically crafted into intricate designs. However, its low strength limits its use in applications that demand high durability.
In summary, the types of brass alloys discussed each serve distinct purposes and have unique properties, affecting their applicability in various industries. Understanding these differences aids professionals in selecting the right material for their specific needs.
Manufacturing Processes of Brass Alloys
Manufacturing processes for brass alloys play a critical role in determining the quality and application of the final metal products. These processes are not just about shaping the alloy but also about enhancing specific properties, such as strength, ductility, and resistance to corrosion. A thorough understanding of these methods is therefore essential for anyone engaging with brass alloys in engineering or design. As we explore each technique, we will consider the benefits they offer, alongside important considerations for manufacturers.
Casting Techniques
Casting is one of the oldest methods of manufacturing brass alloys. This technique involves pouring molten brass into molds where it solidifies into desired shapes. There are various casting methods such as sand casting, die casting, and investment casting. Each method has unique advantages based on the complexity of the design and production volumes.
- Sand Casting: This is a cost-effective process, especially for prototype production. Molds are made from a mixture of sand and a binding agent. This technique can produce large components but often requires post-casting machining to achieve precise tolerances.
- Die Casting: This method is ideal for high-volume production. It uses metal molds, allowing for fine detail and smooth surfaces. The initial cost is higher due to mold fabrication but the efficiency increases with scale.
- Investment Casting: This process enables high precision and excellent surface finish, making it suitable for intricate designs. The initial investment is significant, but it results in minimal waste of material.
Casting techniques require careful temperature control and timing to ensure quality. The properties of the alloy can change during casting, which needs to be considered for high-performance applications.
Extrusion Processes
Extrusion is another essential method for producing brass alloys. This process involves forcing the metal through a die to create long sections of uniform cross-section. Extruded brass can be crafted into rods, tubes, and profiles, making it a versatile method for many industries.
- Benefits of Extrusion: The process allows for continuous shapes and is efficient for mass production. The extrusion process also improves mechanical properties due to strain hardening, enhancing both strength and durability.
- Considerations: The choice of die design is crucial, as it directly affects the final product's dimensions and surface finish. Additionally, the temperature during extrusion must be controlled to prevent oxidation and ensure a good flow of material.
Overall, extrusion is an effective way to produce custom profiles that can meet specific application requirements.
Forging and Rolling
Forging and rolling are methods that involve shaping brass alloys through mechanical working. Forging involves heating the metal and then deforming it under pressure. This creates a denser grain structure, thereby enhancing mechanical properties.
- Forging: This technique can be performed hot or cold, depending on the desired characteristics. Forging results in a robust material with high fatigue resistance. It is ideal for components subjected to high-stress, such as gears and axles.
- Rolling: This is a process where metal is passed through rollers to reduce thickness. Rolling can be hot or cold, with cold rolling typically leading to superior surface finish and tighter tolerances. Components like sheets and strips are commonly produced this way.
Both forging and rolling lead to efficient material usage and can be adapted for various scale needs. However, the energy costs and equipment requirements can be significant.
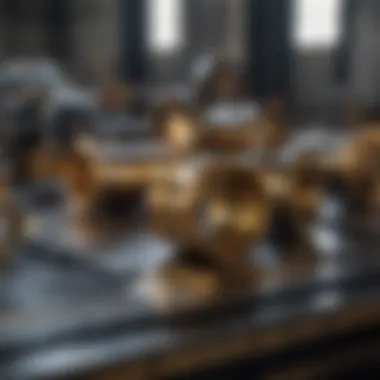
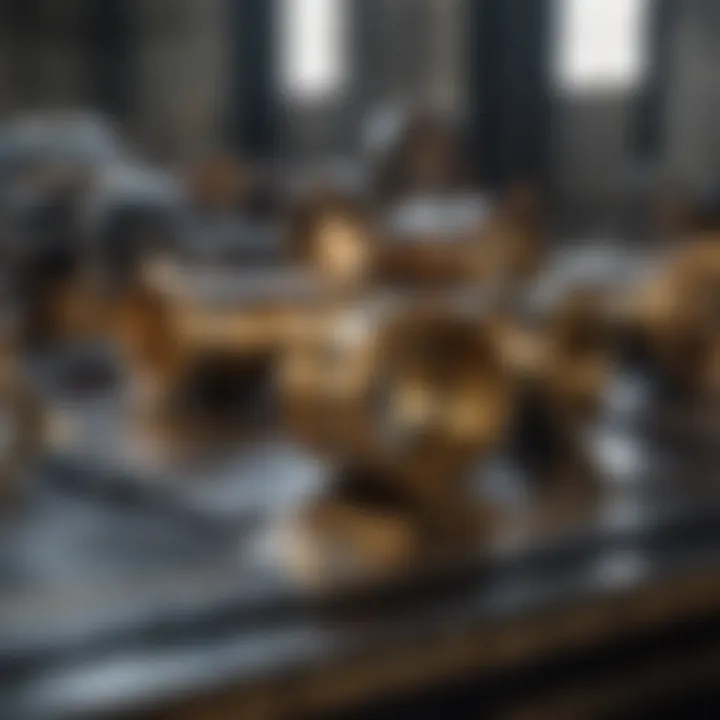
Proper selection of manufacturing processes impacts the sustainability of brass alloy production by minimizing waste while maximizing performance.
Understanding the intricacies of these processes aids in selecting the right method for a given application, ensuring optimized performance and cost-effectiveness in manufacturing brass alloys.
Applications of Brass Alloy
Brass alloy is significant in multiple industries due to its unique properties. The versatility and combination of elements in brass enhance its functionality across various applications. Understanding the applications can provide insights into both historical usage and future potential. Key benefits include its machinability, corrosion resistance, and ability to be cast in intricate shapes. These factors make brass an attractive choice in sectors requiring durability, aesthetic appeal, and reliable performance.
Musical Instruments
Brass alloy is predominantly used in musical instruments such as trumpets, trombones, and tubas. Instruments made from brass produce a bright and resonant tone, which is essential for performance quality. The alloy's workability allows for fine, detailed crafting of the instrument's shape, contributing to the sound quality. Various compositions of brass, like yellow brass, are often preferred for their sound properties.
Brass instruments often require a delicate balance between sturdiness and lightness. The use of brass supports this balance, allowing musicians to have instruments that perform well without excessive weight. Additionally, the aesthetic appeal of shiny brass enhances the visual attractiveness of instruments, often enticing musicians and collectors alike.
Electrical Components
Brass alloy exhibits excellent electrical conductivity while maintaining mechanical strength. This makes it a preferred material for electrical components such as plug connectors, switches, and terminals. The ability to withstand corrosion further enhances its utility in electrical applications, ensuring long-lasting performance in varied environments.
In terms of specific applications, brass is often used in components that require reliable electrical connections. Its ductility allows for easy shaping and forming into complex designs, which can be essential for specific electrical needs. Moreover, brass's resistance to tarnishing ensures that performance is not compromised over time, making it a suitable choice in industries that rely on consistent electrical performance.
Plumbing Fixtures
In plumbing, brass is commonly used for faucets, valves, and fittings. The corrosion resistance of brass makes it ideal in environments where exposure to water and moisture is frequent. Unlike other metals, brass can withstand harsh conditions without deteriorating quickly.
Additionally, the ease of fabrication allows plumbing fixtures to be efficiently manufactured to meet various design specifications. Brass fittings are reliable under different pressure levels, making them essential for plumbing systems. They ensure that joints and connections remain leak-proof and functional.
In summary, the applications of brass alloy span various fields, demonstrating its versatility. From musical instruments to vital plumbing fixtures, brass serves essential roles, and understanding these applications is crucial for industries and future innovations.
Advantages of Brass Alloy
Brass alloys have gained significant attention in various fields due to their unique characteristics and advantages. These are not just material preferences but practical considerations guiding engineers, designers, and manufacturers. Understanding the advantages of brass alloys can help professionals make informed decisions when selecting materials for specific applications and projects.
Workability and Machinability
One of the primary advantages of brass alloys is their exceptional workability and machinability. Brass can be easily formed into various shapes without losing structural integrity. This ability to be readily shaped makes it a popular choice in manufacturing processes. The fine grain structure of brass allows for precise cutting, resulting in less wear and tear on tools used during machining. Additionally, brass has favorable properties that allow for smooth finishes, which is especially important for components requiring tight tolerances.
- Easy to cut: Brass can be shaped through various methods, such as turning, milling, and grinding.
- Low friction: This reduces wear on cutting tools and enhances process efficiency.
- Versatile applications: Components can range from intricate designs to sturdy parts, suitable for numerous industries.
These traits make brass an ideal candidate for applications requiring high accuracy, such as in the production of small fittings or precision components.
Aesthetic Appeal
Another notable benefit of brass alloys is their aesthetic appeal. The naturally warm golden hue of brass complements various designs, making it a favored material in architectural and design contexts. Whether for decorative fixtures, musical instruments, or jewelry, the visual allure of brass often contributes to its selection. Furthermore, brass can be polished to a high shine or left with a more subdued finish; this flexibility allows designers to achieve desired aesthetics without needing additional treatments.
- Color options: Brass can be coated or treated for different appearances.
- Patination: Over time, brass develops a unique patina that can enhance its character.
- Use in design: Its pleasing appearance makes it suitable for artistic applications.
The aesthetic versatility of brass means it can be integrated seamlessly into both modern and traditional settings, appealing to a wide range of preferences.
Thermal Conductivity
Thermal conductivity is another critical advantage of brass alloys. Brass materials conduct heat effectively, making them suitable for applications that require quick heat dissipation, such as in heat exchangers or electronic components. Good thermal conductivity ensures that brass parts maintain consistent temperatures, minimizing the risk of thermal damage or failure.
- Heat transfer: Brass efficiently transfers heat, which is vital for engine components and radiators.
- Durability: Enhanced performance in temperature fluctuations can lead to longer service life for components.
- Energy efficiency: Using brass in heating systems can improve overall energy efficiency.
Challenges in Brass Alloy Use
Brass alloys are widely used in various applications due to their favorable properties, yet there are notable challenges tied to their use. This section aims to shed light on these key difficulties, specifically focusing on zinc leaching issues and the environmental impacts of production. Addressing these challenges is vital for future advancements in brass alloy technology.
Zinc Leaching Issues
Zinc leaching is one significant problem in the utilization of brass alloys. Brass is primarily composed of copper and zinc, although the specific proportions can vary. During certain conditions, particularly in plumbing applications, zinc can be released into water. This phenomenon raises several health concerns.
When zinc leaches into drinking water, it can lead to gastrointestinal complications if consumed in high quantities. Moreover, the water's taste can alter, affecting consumer satisfaction. It is essential to understand the conditions under which leaching occurs, as temperature, pH, and the presence of corrosive agents can enhance the process.
To mitigate such issues, engineers and material scientists explore coatings or alternative materials. These efforts are crucial to maintaining public health while preserving the beneficial properties of brass alloys. Innovations in lead-free brass formulations may also play a role in reducing the risk of zinc leaching.
Environmental Impact of Production
Another pressing challenge is the environmental impact associated with the production of brass alloys. The extraction and processing of copper and zinc, the primary elements in brass, consume significant resources and energy. Mining operations contribute to land degradation and encourage ecosystem disruption.
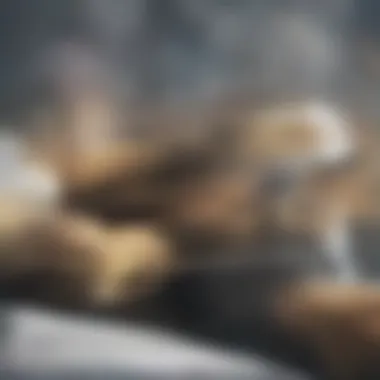
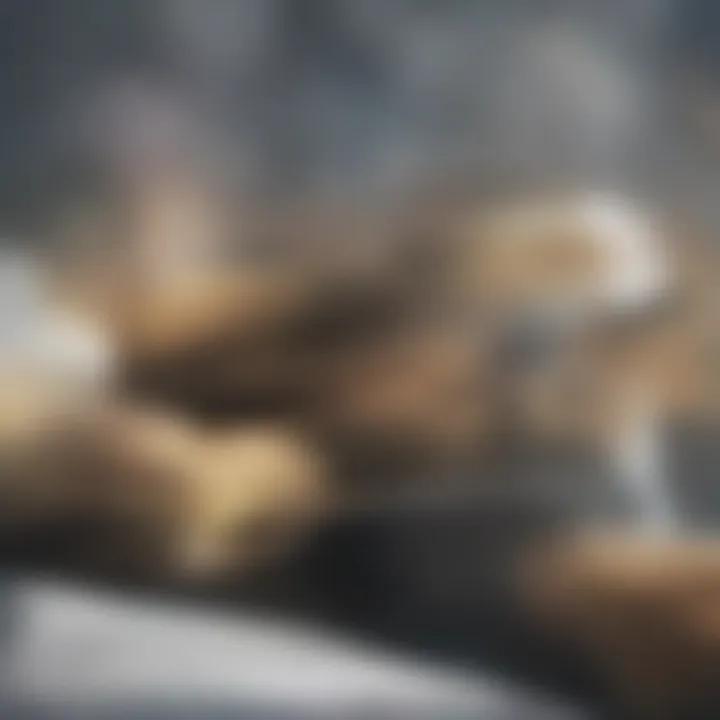
Additionally, the production process itself generates pollutants, which can adversely affect air and water quality. Many brass manufacturers face regulations aimed at curbing these impacts, prompting the industry to adopt more sustainable practices.
Efforts are underway to enhance recycling processes, aiming to limit the need for raw material extraction. As recycled brass retains the desired characteristics of new alloys, it presents a more environmentally friendly solution.
"Sustainability in metal production is not just an option; it is rapidly becoming a necessity."
Recent Innovations in Brass Alloy Development
The field of brass alloy development has witnessed significant transformations in recent years. These innovations are crucial for various reasons, including the need for enhanced environmental sustainability, the demand for improved material performance, and advancements in manufacturing technologies. As industries strive to meet stringent regulations and market expectations, understanding these recent advancements in brass alloys becomes essential, especially for professionals engaged in materials science and engineering.
Lead-Free Brass Alloys
Lead has been a common additive in brass alloys for many years, primarily due to its ability to enhance machinability. However, increasing awareness of health hazards associated with lead has prompted the development of lead-free brass alternatives. The innovative formulations of lead-free alloys typically incorporate elements like copper, zinc, and tin, which maintain adequate machinability while significantly reducing health risks.
- Benefits of Lead-Free Alloys:
- Health and safety improvements for workers in machining and fabrication.
- Compliance with regulatory requirements, such as those set by the EPA.
- Enhanced corrosion resistance compared to traditional leaded brass.
Despite these benefits, lead-free brass presents challenges. For instance, the machinability may not match that of leaded brass, necessitating adjustments in manufacturing processes. Ongoing research aims to refine these formulations further and address machinability concerns through technological enhancements.
Smart Alloys Integration
The integration of smart alloys into brass development represents a dynamic shift in material capabilities. Smart alloys react to environmental stimuli, allowing for enhanced adaptability in applications. For brass, this innovation can lead to improvements in damping properties, electrical conductivity, and overall resilience.
- Key Attributes of Smart Brass Alloys:
- Ability to change properties based on external factors like temperature and stress.
- Improved lifespan of components due to self-regulating features.
- Increased versatility in both industrial and consumer applications, such as in electronic devices or automotive parts.
As industries adopt smart alloys, considerations around manufacturing techniques and application contexts will grow in importance. Future developments may include the combination of smart features with traditional brass properties, leading to hybrid materials that fulfill a broader spectrum of needs in sectors such as electronics, aerospace, and architecture.
"The future of brass alloy development hinges not just on improving existing properties, but also on tapping into new functionalities through innovation."
In summary, the innovations in the realm of brass alloys, particularly lead-free formulations and smart alloys integration, address critical future-focused material requirements. These developments not only prioritize health and safety but also open avenues for expanded applications and enhanced performance across industries.
Future Prospects of Brass Alloy Research
Brass alloys have been essential in various industries for decades, and their future is likely to hold significant advancements. Understanding the prospects of brass alloy research is crucial for both current applications and future innovations. Research in this area focuses not only on improving existing materials but also on developing new, sustainable solutions that meet modern requirements. In particular, attention is directed towards enhancing properties such as corrosion resistance, strength, and workability, which are vital in many applications.
Sustainable Manufacturing Practices
The push for sustainable practices in manufacturing is more urgent than ever. Brass alloys, traditionally containing lead and other substances, have faced scrutiny due to health risks and environmental impacts. The future of brass alloy research will likely emphasize lead-free alternatives. These new formulations aim to maintain the quality and performance of brass while eliminating harmful components.
Additionally, researchers are exploring methods to minimize energy consumption during the production of brass alloys.
Some potential strategies are:
- Recycling and Reuse: Recycling brass can significantly reduce the environmental footprint. It requires less energy and raw materials compared to producing new alloys from scratch.
- Efficient Processing Techniques: Innovations in casting, forging, and machining can further reduce waste and energy use. Researchers are working on refining these methods to improve efficiency.
- Biodegradable Alternatives: There is ongoing research aimed at integrating biodegradable components into brass processing, which could lessen the ecological impact associated with end-of-life disposal.
Emerging Applications
As materials science continues to evolve, the applications of brass alloys are expanding. This development not only opens new markets but also reinforces the ongoing relevance of brass as a versatile material. Some of the emerging applications include:
- Electronics: With the rise of smart devices, there is a growing need for materials that can efficiently conduct electricity while resisting tarnishing and corrosion. Brass alloys meet these criteria effectively, making them ideal for connectors and components in electronic devices.
- Medical Devices: Due to its antimicrobial properties, certain brass alloys are being investigated for use in medical devices and hospital environments, where hygiene is essential.
- Architectural Design: In construction and design, brass is becoming popular for its aesthetic appeal. Its sability and workability make it suitable for fixtures, accents, and structural components, contributing to both form and function.
Research into these emerging sectors highlights the adaptability of brass alloys. By prioritizing sustainable practices and examining new applications, the field is poised for meaningful advancements that can benefit industries globally.
"As industries evolve, the future of brass alloy is bright, paving the way for innovative solutions that combine functionality with sustainability."
The continued exploration in brass alloy research holds the potential to yield not only better materials but also a deeper understanding of sustainable practices in manufacturing and application.
Epilogue
The conclusion holds significant value in this article as it serves to encapsulate the extensive discussion around brass alloys. Recognizing the importance of brass as a metallic composite, we summarize the insights derived from its analysis, highlighting both the essential characteristics and newfound innovations.
Summary of Key Points
In the context of brass alloys, several key points emerge:
- Definition and Composition: Brass is an alloy primarily made of copper and zinc. Its versatility can be attributed to the varying ratios of these metals. Other elements like lead may also be included to enhance machinability.
- Chemical Properties: Brass exhibits commendable corrosion resistance, which is critical for its use in environments subject to moisture and chemicals.
- Applications: Multiple industries utilize brass, from plumbing fixtures to musical instruments, showcasing its wide range of functionalities.
- Advantages: Brass boasts excellent workability and aesthetic appeal. Its thermal conductivity is valuable in applications requiring efficient heat transfer.
- Challenges: Attention must be paid to issues like zinc leaching and the environmental impacts associated with brass production.
- Innovations: Recent developments focus on lead-free brass alternatives and smart alloys that integrate new technological features.
These various perspectives contribute to the understanding of how brass alloys have evolved and their significance within different sectors.
Implications for Future Research
Future research on brass alloys can forge paths towards more sustainable practices, particularly in manufacturing processes. This can include the exploration of:
- Eco-friendly Materials: Investigating alternative, less harmful materials that can replace lead in alloys while maintaining performance quality.
- Performance Enhancements: Identifying new formulations that could expand the capabilities of brass in demanding applications.
- Recycling Methods: Developing improved procedures for recycling brass to minimize wastage and reduce the environmental footprint.
- Smart Technologies: Integrating smart features into brass alloys to create products that can adapt or respond to environmental factors.
These areas of inquiry not only pose relevant questions but also expand the horizon of materials science, encouraging ongoing discussion within the academic and industrial communities.