Cement CO2 Emissions: Challenges and Solutions
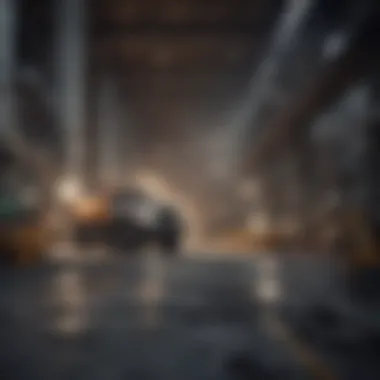
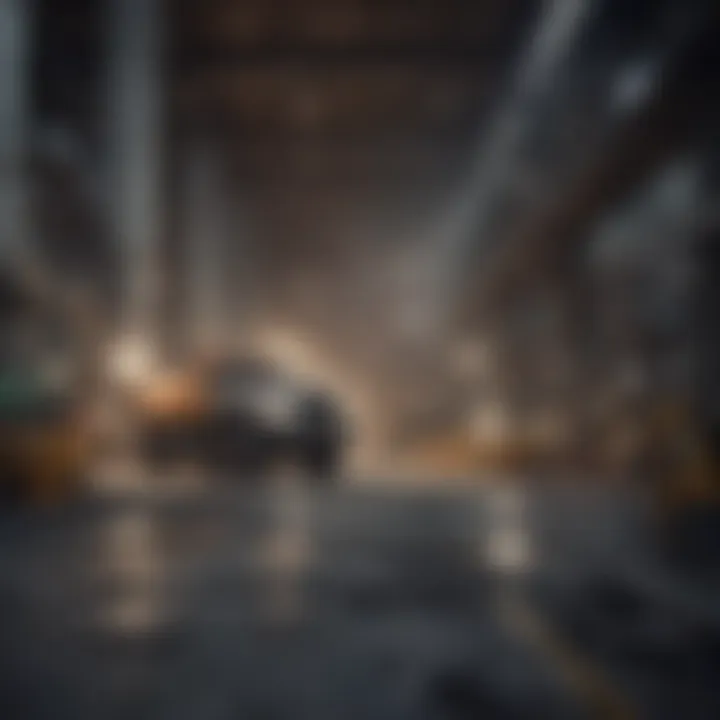
Intro
Cement, a substance that many take for granted, plays a vital role in construction and infrastructure. However, the production of cement carries a heavy environmental cost. As it stands, cement production is responsible for around eight percent of global CO2 emissions, presenting a daunting challenge in the face of climate change. This article aims to unravel the intricacies surrounding cement emissions—highlighting its significance to both industry and environment alike.
Understanding the chemical processes at play in cement manufacture is crucial. The traditional method involves heating limestone and clay in a kiln, a process that not only emits CO2 but also requires vast amounts of energy, primarily from fossil fuels. Given the rising demand for cement in developing countries and the ongoing urbanization trends, the urgency for alternative production methods has never been greater.
Moreover, as policymakers and businesses seek ways to lower their carbon footprints, the impact of innovations in materials, carbon capture technologies, and policy implications are of paramount importance. Tackling cement-related emissions isn't just a technical challenge; it bears heavy societal stakes, too. There’s a pressing need for comprehensive oversight, informed dialogue, and collaborative efforts, bringing together researchers, policy-makers, and industry leaders alike.
Prelude to Cement Production and CO2 Emissions
The cement industry is often referred to as the backbone of modern infrastructure. From towering skyscrapers to sprawling highway systems, its presence is hard to miss. Yet, this omnipresence comes at a cost, especially regarding its contributions to global carbon dioxide emissions. Cement production has become synonymous with substantial environmental impact, contributing to roughly eight percent of total CO2 emissions worldwide. Understanding the process of cement manufacturing and its relationship with climate change is crucial not only for industry professionals but also for anyone concerned about the future of our planet.
This section will delve into the nuances of cement production, highlighting its importance in our day-to-day lives while also drawing attention to the environmental considerations that accompany it. We will explore various aspects of the manufacturing process and how it ties into the larger conversation about global warming and sustainability.
Overview of Cement Manufacturing Process
Cement manufacturing is a complex process that encompasses several stages, each producing emissions through chemical reactions and fuel combustion. At its core, the process begins with the extraction of raw materials such as limestone, clay, and sand, which are transported to a factory. The primary ingredient, limestone, is heated in a kiln at temperatures exceeding 1,400 degrees Celsius, leading to a transformation where calcium carbonate decomposes to form calcium oxide, releasing CO2 as a byproduct.
- The main steps in cement production include:
- Raw Material Extraction: Sourcing elements primarily from quarries.
- Crushing and Grinding: Reducing the size of raw materials for blending.
- Homogenization: Ensuring consistent chemical composition.
- Calcination: Removing carbon dioxide from limestone within rotary kilns.
- Clinker Production: Cooling the clinker post-kiln, a key element in cement.
- Grinding and Blending: Mixing clinker with additives to produce the final cement product.
Thus, it’s not just the heating that’s of concern; every step has a cumulative effect on the total emissions associated with cement manufacturing.
Global Context of CO2 Emissions
The heating of raw materials is a significant contributor to greenhouse gas emissions on a global scale. As the world tilts more toward sustainable practices, it’s important to contextualize the role of cement in the larger picture of global emissions. Different countries contribute differently based on their levels of industrialization and energy sources. Emerging economies tend to depend heavily on coal for energy, further exacerbating emissions linked to cement production.
Moreover, the construction boom in developing regions compounds the situation, leading to higher demand for cement.
At the same time, many nations are starting to rein in production through regulations and initiatives aiming to reduce carbon footprints. This includes strict mandates targeting energy efficiency, emissions reductions, and innovation in alternative building materials.
The World Business Council for Sustainable Development reports that a significant push towards sustainability in the cement industry could potentially cut CO2 emissions by 30% by 2030.
In summary, the cement manufacturing process is fundamental to modern infrastructure, yet it poses significant environmental challenges. A thorough understanding of these challenges is essential for paving the way for a more sustainable future.
Chemical Reactions in Cement Production
The chemical reactions involved in cement production bear heavy implications for both the efficiency of the manufacturing process and the environmental toll it takes. Cement, primarily a mixture of calcium silicate compounds, forms the backbone of modern construction. Yet, this fundamental material brings with it a host of environmental concerns, particularly regarding carbon dioxide emissions.
In cement manufacturing, the chemical breakdown of limestone is a critical first step. This process, alongside the combination of various raw materials, sets the stage for the formation of clinker, the substance that eventually becomes cement. Understanding these intricate reactions not only shines a light on their significance in the overall production but also emphasizes the potential pathways for emission reductions.
The Role of Limestone
Limestone serves as the cornerstone of silicon, alumina, iron oxide, and other compounds needed for cement production. When limestone is subjected to high temperatures, generally around 1,450 degrees Celsius, it undergoes calcination. During this process, limestone (calcium carbonate) decomposes into calcium oxide and releases carbon dioxide:
This reaction is responsible for nearly 60% of the total CO2 emissions from cement production, making it a pivotal component to consider in emissions strategies. The extracted calcium oxide then reacts with silica, alumina, and iron oxide to form compounds like tricalcium silicate, crucial for cement strength and durability.
One must note, however, that sourcing limestone itself comes with its own set of environmental considerations. The extraction process can disrupt local ecosystems and lead to degradation of landscapes, putting pressure on already fragile environments. Therefore, innovative approaches are necessary to limit not just the emissions from calcination, but to also strike a balance between resource extraction and environmental stewardship.
Other Raw Materials Used
In addition to limestone, cement production incorporates a variety of other raw materials such as clay and iron ore. These materials also undergo distinct chemical reactions during the clinker formation process. For instance:
- Clay provides aluminum and silica, essential for the development of critical silicate compounds.
- Iron ore is vital in creating the distinct properties of cement, impacting color and strength.
When these materials are mixed and heated, they undergo complex reactions that ultimately lead to the synthesis of various silicate and aluminoferrite compounds. The more diverse the raw materials used, the greater the potential to modify the chemical reactions taking place, which can lead to modifications in emissions levels.
This flexibility invites future innovations. Utilizing industrial by-products like fly ash or slag can not only enhance the chemistry of cement but can also cut down the carbon footprint significantly. This opens the door for sustainable practices that leverage alternative materials, thus redefining the production landscape for cement.
Quantifying Cement's Contribution to Climate Change
To appreciate the profound implications cement production has on climate change, it is crucial to delve into how this industry quantifies its contribution to CO2 emissions. Cement, often dubbed the backbone of modern construction, is responsible for about eight percent of the global greenhouse gas emissions. The importance of scrutinizing these emissions cannot be overstated; it offers insights essential for policy-making and informs strategies for sustainable development. By understanding the level of emissions, stakeholders can prioritize reduction measures, innovate within processes, and adhere to international climate agreements.
Metrics for Measuring Carbon Emissions
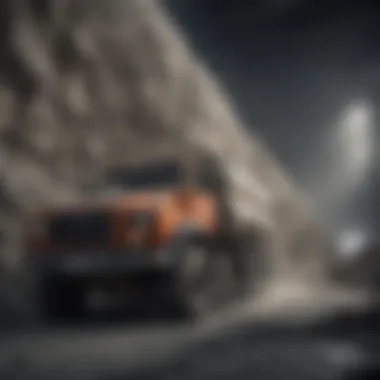
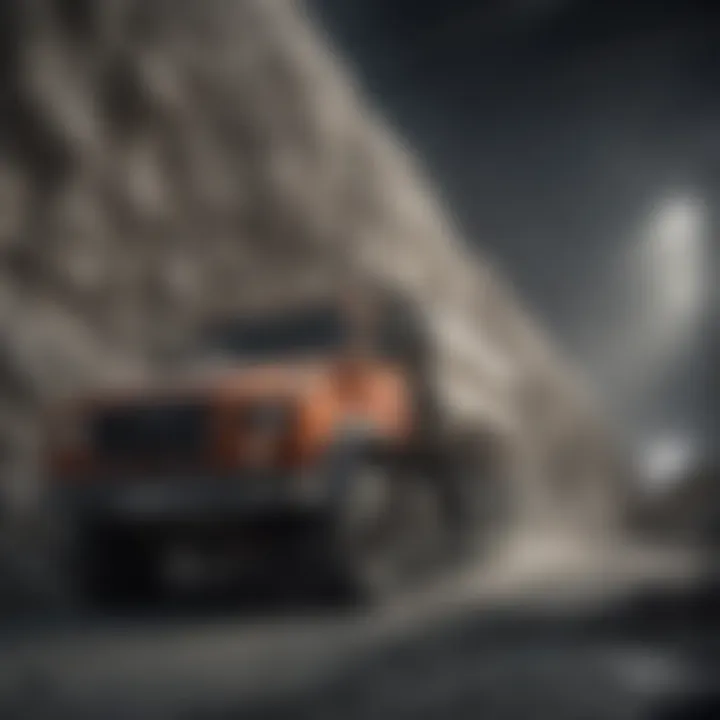
Understanding how to measure carbon emissions in cement production is palpably vital. Different metrics provide varied perspectives. Here are some key methods:
- CO2 Intensity: Often expressed in tonnes of CO2 emitted per tonne of cement produced, this metric offers a direct insight into the emission efficiency of the production process.
- Life Cycle Assessment (LCA): This approach monitors emissions throughout all stages—from raw material extraction, through manufacture, to transportation and use of cement—providing a holistic view of the emissions associated with cement.
- Carbon Footprint Calculators: These tools can help companies estimate their total greenhouse gas emissions tailored to specific operations or practices in cement production.
By using a combination of these measurements, stakeholders can pinpoint emission sources more accurately.
Regional Variations in Emissions
Cement production does not occur in a uniform manner across the globe, and as such, regional variations in emissions are significant. Factors influencing these disparities include:
- Resource Availability: Areas rich in natural materials, like limestone, may have a lower carbon footprint because they can utilize locally sourced raw materials, reducing transportation emissions.
- Technology Adoption: Regions with advanced technology tend to have lower emissions due to the implementation of modern, efficient production methods.
- Regulatory Environment: The stringency of regulations and policies governing emissions can vary widely, influencing how cement companies operate.
For instance, countries in Europe often have stricter regulations that enforce rigorous sustainability measures compared to developing nations where rapid urbanization may lead to higher emissions despite a growing awareness of climate issues.
Alternative Materials in Cement Production
The quest for sustainability in construction and manufacturing has brought the topic of alternative materials in cement production into the spotlight. As traditional cement production is notorious for its high CO2 emissions, seeking innovative alternatives becomes not just a matter of preference, but an urgent necessity. Alternative materials not only hold the promise of reducing carbon footprints but also enhance the overall performance of concrete. Understanding their role provides insights into how the cement industry can pivot towards a more sustainable future.
Fly Ash and Slag Utilization
Fly ash, a byproduct from burning pulverized coal in electric power generating plants, is one of the most widely used supplementary cementitious materials. By substituting a portion of the cement with fly ash, we can effectively harness its pozzolanic properties. This results in numerous benefits:
- Environmental Impact: Using fly ash reduces the demand for traditional cement, thereby decreasing the overall CO2 emissions associated with its production. Not only does this divert waste from landfills, but it also conserves natural resources.
- Improved Concrete Durability: Concrete mixed with fly ash exhibits enhanced durability against sulfate attack and alkali-silica reaction. The bottom line is longevity—structures built to last.
Similarly, granulated blast furnace slag, a byproduct of iron production, serves as another alternative. The reactions it undergoes with water and calcium hydroxide lead to comparable strength attributes as traditional Portland cement. This not only reduces the carbon footprint but also improves the overall mechanical properties of the mix. The utilization of these materials may not be mainstream yet, but their benefits are making waves in sustainable building practices.
Biomass and Recycled Materials
When considering a shift towards sustainability, the use of biomass and recycled materials in cement production gains traction. Biomass, including agricultural residues, poses an innovative way to replace conventional fuels in cement kilns. Instead of relying solely on fossil fuels, adopting biomass can lead to significant reductions in greenhouse gas emissions. Here’s a closer look at its advantages:
- Carbon Neutrality: Biomass is often considered carbon neutral because the CO2 it releases during combustion is roughly equivalent to the CO2 absorbed during its growth. Thus, while it may not eliminate emissions completely, it can significantly lessen their impact.
- Circular Economy: Integrating recycled materials such as glass cullet or crushed concrete into cement production promotes a circular economy. This approach helps salvage resources that would otherwise contribute to waste, fostering an environmentally friendly industry.
Furthermore, incorporating recycled materials can also lead to better thermal properties and increased insulation of buildings. These benefits underscore the potential for a holistic approach, where both economic and environmental aspects are balanced, creating a win-win situation for all stakeholders in the industry.
In summary, the exploration of alternative materials not only addresses the pressing issue of CO2 emissions but also paves the way for innovative practices within the cement industry.
The shift towards these materials is crucial, as they offer a pathway to significantly lower emissions, foster sustainability, and ensure that cement remains a critical component of modern construction without compromising our planet's health.
Innovative Technologies for Emission Reduction
The challenge of reducing CO2 emissions from cement production is no trifling matter; it requires innovative thinking and advanced technologies. The significance of innovative technologies in minimizing emissions cannot be overstated. They stand at the forefront of the cement industry’s attempts to carry on its operations while lessening its environmental footprint. As global consciousness shifts toward sustainability, these technologies not only mitigate adverse effects on the climate but also pave the way for a more responsible approach to construction and infrastructure.
Adopting new technologies can lead to a myriad of benefits, such as:
- Lower emissions: By integrating advanced techniques, companies can significantly decrease the volume of CO2 released during production.
- Cost-effectiveness: These innovative solutions can, in many instances, lead to long-term financial savings by optimizing production processes and reducing energy use.
- Improved product quality: Enhanced production methods often result in stronger and more durable cement products, which can further contribute to sustainability by reducing the need for repairs and replacements.
However, considerations abound when implementing these technologies. Investment costs, the need for incoming workforce training, and the readiness of existing infrastructure to accept these innovations are just a few crucial factors that must be weighed.
Carbon Capture Techniques
Carbon capture techniques are emerging as a beacon of hope in the fight against carbon emissions. These methods are designed to capture the CO2 produced during cement manufacturing before it can enter the atmosphere. The technology functions by filtering out CO2 from the exhaust gases released during the production process and storing it safely rather than allowing it to contribute to climate change.
Some of the notable techniques include:
- Post-combustion capture: This method captures CO2 after fossil fuels are burned, using chemical solvents to seize the carbon dioxide from flue gases.
- Pre-combustion capture: Here, carbon is removed before combustion. A mix of fuel and air is subjected to partial oxidation, producing a synthesis gas that separates the CO2 before it is combusted.
- Oxy-fuel combustion: This involves burning the fuel in pure oxygen, which creates a flue gas composed mainly of CO2 and water vapor, making capturing the carbon much easier.
Implementing these techniques can lead to a marked reduction in emissions. However, the technology is still maturing, with substantial research and development needed to make it widely applicable across various cement operations.
Utilization of Carbon as a Resource
Rather than merely seeing carbon emissions as a problem requiring a solution, there is a growing movement toward viewing carbon as a resource. This paradigm shift envisions using captured CO2 as feedstock for new products.
Some innovative applications include:
- Mineralization: This process involves converting captured CO2 into stable carbonate minerals, which can then be used in construction materials, creating a useful byproduct from something that would otherwise be waste.
- Synthetic fuels: Captured carbon can be transformed into synthetic fuels, which can help offset reliance on fossil fuels. The idea is to create a closed-loop system where carbon is reused perpetually rather than simply emitted.
- Renewable Chemicals: There is potential to develop chemical products from captured CO2, such as methanol and other valuable compounds used in various manufacturing processes.
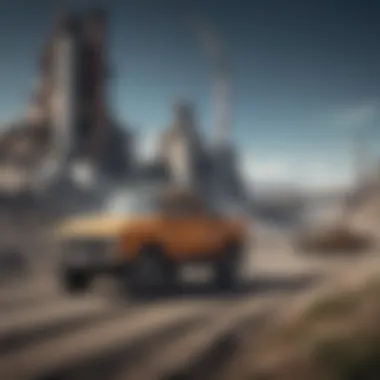
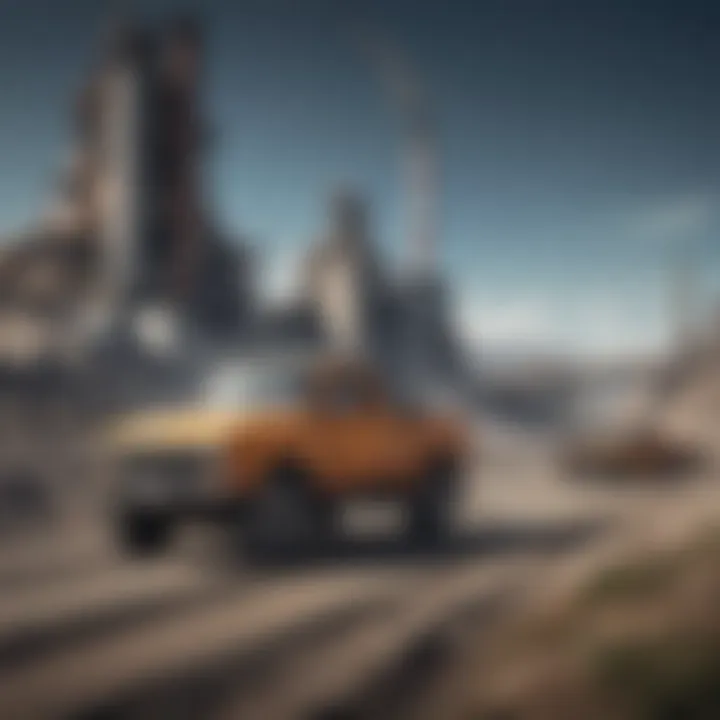
This utilization strategy not only addresses emissions but also encourages innovation and growth in other industries, pushing society towards a more circular economy.
"Innovative technologies might just be the cornerstone upon which we build a sustainable future for the cement industry."
In summary, the road to emission reduction in cement production is inextricably linked to the development and adoption of innovative technologies. Whether through advanced carbon capture techniques or the utilization of carbon as a valuable resource, the industry stands at a pivotal moment where change is both necessary and achievable. The future of cement production could very well depend on how we harness these innovations.
Regulatory Framework and Policies
The regulatory framework surrounding cement production is crucial in addressing the industry's considerable contribution to CO2 emissions. As the world grapples with climate change, policymakers are finding it essential to establish clear guidelines that balance environmental sustainability while ensuring economic viability within the cement industry. This balancing act involves creating policies that not only regulate emissions but also incentivize the adoption of cleaner technologies and alternative materials.
International Agreements and Goals
Internationally, agreements such as the Paris Accord set ambitious targets for CO2 reductions on a global scale. Countries participating in this agreement commit to limiting global temperature rise, which indirectly puts pressure on industries like cement to step up their game. These targets often translate into national policies that require the cement sector to improve its sustainability practices.
Countries are expected to report their emissions regularly, fostering transparency. To align with these goals, initiatives like emissions trading schemes, carbon taxes, and subsidies for green technology have been introduced. For instance, the European Union’s Emissions Trading System (ETS) is a robust model that helps to set a cap on emissions while allowing market forces to dictate carbon pricing.
The significance of adhering to these international agreements cannot be overstated as they drive nations to innovate and transition toward sustainable building practices.
"The clearest way to show what the future holds is to be an active participant in the projects of today.”
National Policies Impacting the Cement Industry
National policies also play a pivotal role in shaping the strategies employed by the cement sector. Each country has its approach, driven by local conditions, industry needs, and environmental objectives. For example, countries like Canada and Germany have introduced stringent regulations that mandate lower emissions thresholds for cement plants. These requirements often include specific benchmarks that must be met for organizations to operate.
In addition, financial incentives such as grants and low-interest loans are offered to companies willing to invest in emission reduction technologies or in research for alternative materials.
Some nations have started implementing more comprehensive frameworks, which integrate efforts from various sectors to address emissions holistically. Such frameworks encourage collaboration across industries, essentially broadening the impact of cement-related policies on overall national sustainability goals.
To summarize, the regulatory framework concerning cement production is a complex yet vital aspect of mitigating CO2 emissions. The interplay between international goals and national policies helps create a structured pathway for the industry to innovate, adapt, and contribute positively to a more sustainable future.
Impact of Cement Production on Local Communities
The impact of cement production on local communities is a critical aspect that deserves focused attention. Cement plants are not standalone entities; they operate within the fabric of the communities they inhabit. The economic activities surrounding cement production can create a ripple effect that reaches deep into the daily lives of residents. Yet, this growth is often accompanied by a host of challenges, particularly environmental and health-related concerns, that cannot be overlooked.
Economic Benefits Versus Environmental Costs
When looking at the economic engine that cement plants can provide, it’s clear that they offer significant advantages. For many small towns, a cement factory can be a lifeline that brings jobs, robust tax revenue, and local business stimulation. For example, in towns where factory jobs are scarce, employment opportunities in cement production can uplift families economically. Local suppliers often benefit too, as they secure contracts, leading to a more vibrant economy.
However, the economic benefits come at a potentially high cost. The environmental footprint of cement manufacturing includes not just CO2 emissions but also dust, noise, and the alteration of local landscapes. When production ramps up, residents may find their once-quiet surroundings transformed into bustling industrial hubs. This often leads to disputes between economic desires and environmental reality. Local communities are sometimes caught in a tug-of-war: they desire economic growth, but at what environmental cost? The challenge lies in finding a balance where economic development does not undermine environmental health.
"The true measure of progress is not just economic growth, but the health of the community and environment we build it in."
Health Implications for Nearby Residents
The health implications of cement production for nearby residents are a matter of increasing concern. Air quality can deteriorate as emissions—both greenhouse gases and particulate matter—increase. Studies have shown a correlation between living near cement plants and various respiratory ailments. People, particularly children and the elderly, find themselves vulnerable to chronic health issues, which can be even more pronounced among lower-income communities that often bear the brunt of industrial pollution.
Moreover, noise pollution and vibrations from heavy machinery can disrupt daily life, leading to stress and impacting mental health. Long-term proximity to these facilities can affect quality of life, leading some communities to advocate strongly for stricter regulations or even the relocation of industrial activities that pose threats to their health and well-being.
To wrap it up, while cement production can bolster local economies, the associated environmental and health impacts are critical considerations that must be addressed. Communities must navigate these challenges wisely, ensuring that the benefits of cement production do not come at the expense of the health and quality of life of their residents.
Case Studies in Sustainable Cement Practices
Case studies play a crucial role in understanding and demonstrating sustainable practices within the cement industry. Highlighting real-world examples helps to illuminate the path towards reducing carbon emissions and adopting greener technologies. These case studies show not only the practical implementation of innovative methods but also illustrate the tangible benefits these strategies can yield, such as cost savings, improved community relations, and reduced environmental impact.
One significant advantage of examining specific cases is the ability to glean insights that are often overlooked in theoretical discussions. Moreover, showcasing successful initiatives can inspire widespread adoption and collaboration across the sector, facilitating a collective push towards sustainability.
Leading Companies and Their Innovations
Several companies have made noteworthy strides in implementing sustainable cement practices deserving of attention. For example, HeidelbergCement has embraced alternative raw materials and invested in advanced production technologies. They’ve been integrating industrial by-products like fly ash into their cement mixes, which not only reduces waste but also lowers the carbon footprint of the cement produced. Their multiple production sites utilize waste heat recovery units, capturing excess energy that would otherwise be lost, significantly improving energy efficiency.
Another innovative player is LafargeHolcim, which has developed the ECOPact line of cement. This product range allows for a continual reduction in CO2 emissions, meeting various sustainability benchmarks while maintaining performance. Furthermore, the adoption of digital technology and smart logistics has streamlined their operations, further decreasing emissions associated with transportation.
- Innovative Practices include:
- Impact of Innovations:
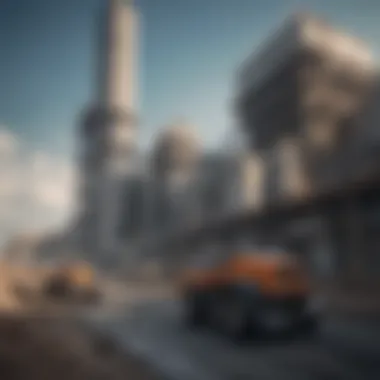
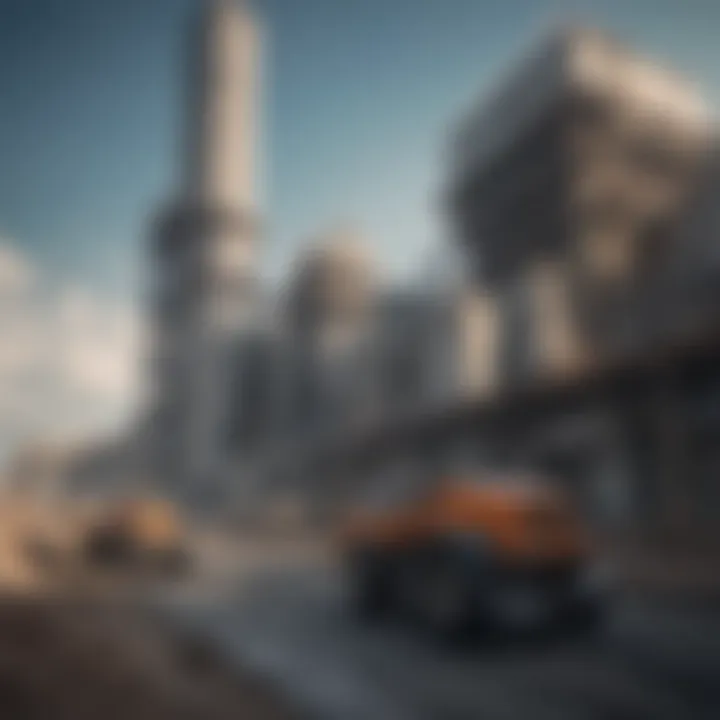
- Alternative material use without compromising structural integrity.
- Installation of carbon capture and storage systems.
- Emphasis on circular economy initiatives, reusing waste materials.
- Reduction of greenhouse gas emissions.
- Increased operational efficiency.
- Improved public perception and market competitiveness.
Successful Implementation of Green Technologies
The real promise in sustainable cement practices can be seen as companies successfully implement green technologies. For instance, CEMEX has deployed innovative carbon capture processes at its production facilities, showcasing their commitment to a low-carbon future. Their use of sustainable biomass as a fuel alternative highlights how diversifying fuel sources can significantly diminish emissions.
Another compelling example is the China National Building Material Group, which has introduced an automated control system for cement production that optimizes the mixing and burning processes. This approach minimizes waste and maximizes energy use efficiency.
In addition to these technological advancements, partnerships with research institutions worldwide reinforce such efforts. The collaboration aims to innovate and refine existing technologies, ensuring that emergent methods remain at the cutting edge of sustainability.
“Sustainable practices in the cement industry are no longer just an option; they’re an imperative.”
Ultimately, examining these case studies paints a promising picture of where the cement industry could head. By learning from others' successes and challenges, it becomes clearer that collaboration and innovation will be vital for a sustainable future.
Future Prospects for the Cement Industry
The future of the cement industry holds significant relevance as it grapples with the pressing demand for sustainable practices while addressing its environmental footprint. As awareness regarding climate change grows, stakeholders across the sector—from researchers to policy-makers—are increasingly focused on probing innovative solutions that can tightly knit sustainability with cement production.
An important element to consider is the shifting preference towards sustainable building materials. This transition is crucial because cement, known for its associated high CO2 emissions, must adapt to evolving market needs. Sustainability isn’t just a buzzword anymore; it’s a core requirement for new construction projects. Builders and developers are now looking beyond traditional materials, adding pressure on cement manufacturers to innovate.
While the traditional cement industry remains the backbone of construction, the essence of its future lies in embracing new, sustainable paradigms.
Trends in Sustainable Building Materials
With increased focus on reducing carbon footprints, emerging trends showcase a move toward materials that are not only effective but also environmentally friendly. The integration of alternative binders, such as geopolymer cements and calcium sulfate, are making waves. These materials often emit less CO2 during production compared to conventional Portland cement.
Additionally, there is a growing interest in materials that incorporate industrial by-products, such as fly ash and slag. Not only do they enhance the durability of concrete, but they also divert waste from landfills, showcasing a win-win situation for both the environment and the economy.
Embracing recycled and bio-based materials in construction adds another layer of innovation. With an emphasis on circular economy principles, stakeholders are maximizing resource efficiency, which, in turn, makes a solid case for sustainable procurement practices. Here are a few notable trends:
- Use of Recycled Aggregates: Old concrete, once crushed, can be reintroduced, reducing the demand for virgin materials.
- Incorporation of Bio-based Materials: Such hasty advancements often depict a more harmonious relationship between the built environment and nature.
- Smart Technology Integration: Internet of Things (IoT) applications are increasingly being used to monitor concrete curing processes, leading to better material performance and reduced waste.
These trends not only present opportunities for cement producers to align with sustainability goals but may also help reduce production costs in the long term.
Research Directions and Innovations Needed
In order for the cement industry to truly evolve, a multitude of research directions and innovations are needed. First off, developing more effective carbon capture technologies is essential. Current techniques show promise; however, advancements can help in making them more efficient and economically viable.
The exploration of new chemical formulations for lower carbon cements is another key area. This might involve extensive experimentation to refine chemical reactions that occur during cement manufacture. As researchers continue to innovate, they may craft cements that maintain performance while dramatically reducing carbon outputs.
The potential for collaboration among academia, industry, and governments stands out. By pooling resources and sharing knowledge, this triad can facilitate breakthroughs that might otherwise remain untapped. This could take form in:
- Joint research and development programs.
- Industry-academia partnerships fostering knowledge exchange.
- Funding mechanisms that champion pioneering projects focused on sustainability.
Keeping abreast of technological advancements is equally crucial. Whether it's through machine learning to optimize production or biological processes for carbon utilization, the horizon is vast with possibilities yet to be realized.
In a nutshell, as the cement industry embarks on a journey towards sustainability, its trajectory will be heavily influenced by innovations that tackle emissions head-on, alongside a commitment to environmentally responsible practices.
End and Call for Action
The narrative surrounding cement production and its CO2 emissions presents a multifaceted challenge that beckons for urgent attention. As one of the key players in the climate change saga, the cement industry contributes a staggering amount to global greenhouse gas emissions. Thus, the call for action is not just a suggestion; it is a plea for collaboration, innovation, and concrete steps toward sustainability.
Summarizing Key Findings
Throughout this article, we've traversed various aspects of cement production, delving deeply into its environmental repercussions. Here are the essential takeaways:
- Cement Production's Contribution: Approximately eight percent of global CO2 emissions stem from cement manufacturing, a highlight that cannot be ignored.
- Chemical Processes: The chemical transformations involving limestone and other raw materials are pivotal to understanding emissions.
- Alternative Materials: The use of fly ash, slag, and recycled materials holds promise for reducing the carbon footprint significantly.
- Innovative Technologies: Cutting-edge carbon capture and utilization methods are emerging, representing a beacon of hope.
- Collaborative Frameworks: Diverse policy frameworks and international commitments play a crucial role in shaping the industry's future.
They paint a picture that, while not devoid of challenges, still reveals pathways to minimize impact. The journey toward a more sustainable future necessitates not only awareness but also actionable steps that unite industry stakeholders, scientists, and policy-makers.
The Importance of Collaboration Across Sectors
Addressing the CO2 emissions from cement production cannot be a solo endeavor. Cross-sector collaboration acts as a keystone in developing comprehensive strategies that encompass various insights and expertise. For instance:
- Academic Institutions: They can spearhead innovative research to create alternatives that other industries may not yet recognize.
- Private Enterprises: Industry leaders must invest in technologies that are both sustainable and economically viable.
- Government Bodies: Regulatory frameworks must evolve to incentivize greener practices while holding companies accountable.
- Non-Governmental Organizations (NGOs): They serve to inform public discourse and promote sustainable practices through advocacy and education.
Engaging in partnerships allows shared knowledge and resources to flourish. It's like growing a garden; there's more fruit when various plants co-exist and support each other. Working together increases the chances of success in combating climate change, as it taps into “collective intelligence” — the understanding that the sum is greater than its parts.
Above all, every stakeholder has a role to play — from lowly engineers in cement plants to high-flying corporate headquarters. The time has come to roll up our sleeves and pivot from the old ways of production to innovative models that emphasize sustainability. Let collaboration ring true as we address one of the most pressing concerns of our time.