Chain Reactors: A Comprehensive Overview
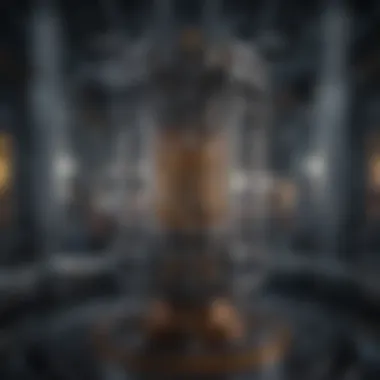
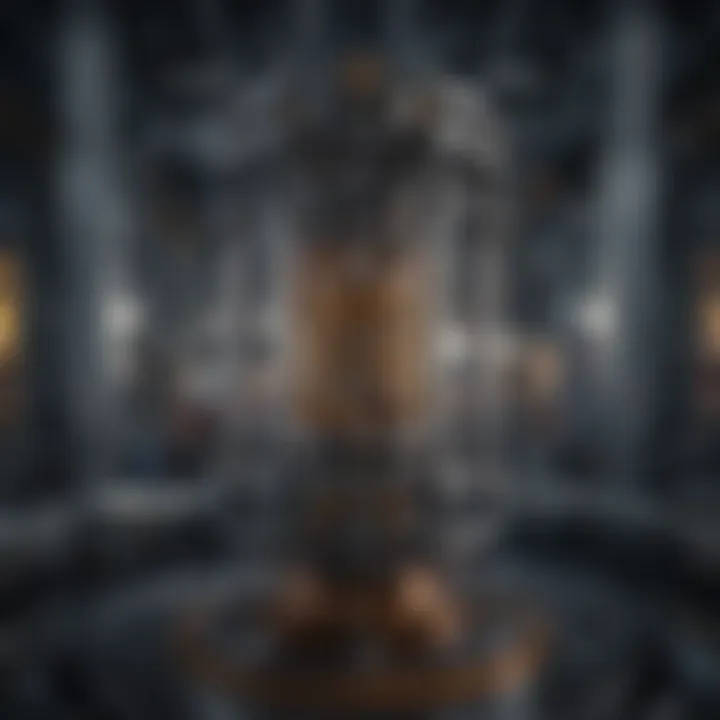
Intro
Chain reactors are complex systems that play a vital role in various scientific fields, including chemistry and engineering. Their ability to facilitate controlled reactions makes them essential in both academic research and industrial applications. Understanding the principles and functions of chain reactors is crucial for anyone looking to delve deeper into modern scientific practices.
This article provides a thorough examination of chain reactors. It aims to dissect their structural dynamics, functionality, and their practical applications across diverse disciplines. We will look at the latest technological advancements, as well as the challenges that researchers face in this domain.
The intention here is to equip students, researchers, and professionals with insights that can enhance their understanding.
Research Overview
Summary of Key Findings
The exploration into chain reactors reveals several key insights:
- Structure and Functionality: Chain reactors consist of interconnected components that enable sequential reactions. This design is crucial for efficiency in various chemical processes.
- Applications: These reactors find use in numerous areas, such as pharmaceuticals, materials science, and energy production. Their versatility is remarkable.
- Technological Advancements: Recent studies highlight innovations in real-time monitoring and control mechanisms that enhance reactor performance.
Significance of Research
Research in this area is significant for many reasons:
- It opens pathways for optimized chemical processes, impacting product yields and economic viability.
- Chain reactors also allow for more sustainable manufacturing practices by improving reaction conditions.
- Findings can lead to advancements in safety protocols, reducing risks in both laboratory and industrial settings.
Methodology
Research Design
This exploration involves a combination of literature review and experimental studies. Researchers analyze existing data and conduct practical experiments to validate theoretical models of chain reactors. This dual approach ensures a robust understanding of the subject.
Data Collection Methods
Data is gathered through several methods:
- Literature Review: Examining peer-reviewed journals and publications that focus on chain reactors informs the foundational knowledge. Relevant sources include articles from Britannica and Wikipedia.
- Experimental Trials: Researchers employ laboratory experiments to observe and document the behaviors of chain reactors under various conditions. This hands-on approach is crucial for empirical validation.
Fundamentals of Chain Reactors
Understanding the fundamentals of chain reactors is essential for grasping their complexities and applications within various scientific disciplines. Chain reactors play a crucial role in chemical processes, especially in the realms of synthesis and manufacturing. They provide a systematic approach to manage reactions involving multiple steps, often yielding higher efficiency and better control over the desired products.
Chain reactors can be designed to fulfill specific requirements of both laboratory and industrial needs. The importance of this section lies in highlighting the basic concepts, the interactions between key components, and the overall contribution of chain reactors to the field of chemistry.
Definition and Importance
A chain reactor is a system that allows for the continuous conversion of reactants into products through a series of interconnected reactions. These reactors can operate under various conditions and can optimize reaction conditions to enhance efficiency. Their flexibility makes them integral in both batch and continuous processes.
For researchers and industry professionals, understanding the operational principles of chain reactors is key. They can significantly impact the productivity and quality of chemical reactions. Their design holds great importance as it influences both the economic and environmental aspects of chemical manufacturing.
Key Components
Key components of chain reactors include reactants, catalysts, and the reaction medium. Each plays a distinct role in the overall efficiency and outcome of the reactions.
Reactants
The reactants are the substances that undergo chemical transformation within the reactor. Selecting the appropriate reactants is vital since they determine the nature of the reaction.
- Key Characteristic: Reactants must be compatible with both each other and the reactor environment. This compatibility enhances the reaction efficiency.
- Benefit: Choosing effective reactants can lead to improved yields and selective production of desired products, which is beneficial for both economic and environmental considerations.
- Unique Feature: Some reactants may require specific conditions like temperature and pressure to perform optimally, which can present challenges in reactor design.
Catalysts
Catalysts are substances that increase the rate of a chemical reaction without being consumed. Their role in chain reactors is indispensable as they enable reactions to occur more rapidly and under milder conditions.
- Key Characteristic: Catalysts can significantly lower the activation energy required for a reaction, leading to faster processing.
- Benefit: Using catalysts can reduce energy expenditure and improve overall efficiency, making them a popular choice in chemical processes.
- Unique Feature: Selecting the right catalyst is critical, as it must interact effectively with the reactants. If not properly chosen, it can lead to undesirable by-products, impacting the purity and yield.
Reaction Medium
The reaction medium is the environment in which the reaction occurs. This can be a solvent or gas, which influences the solubility and interaction of the reactants and products.
- Key Characteristic: The choice of reaction medium can affect the reaction rate and yield, making it an important factor in reactor design.
- Benefit: An appropriate medium can facilitate better reaction control, improving the efficiency and selectivity of the process.
- Unique Feature: Certain mediums can provide advantages such as stabilizing intermediate products but may also pose challenges in terms of handling and disposal.
The interplay of these components within chain reactors establishes a robust framework for efficient biochemical processes. A thorough grasp of these fundamentals is essential for students, researchers, and professionals aiming to innovate within this domain.
Types of Chain Reactors
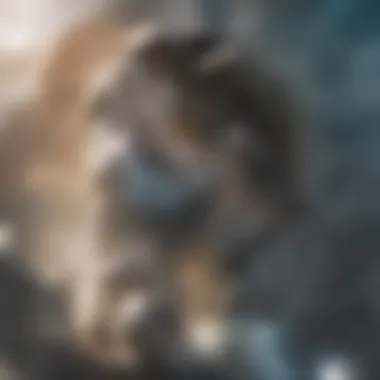
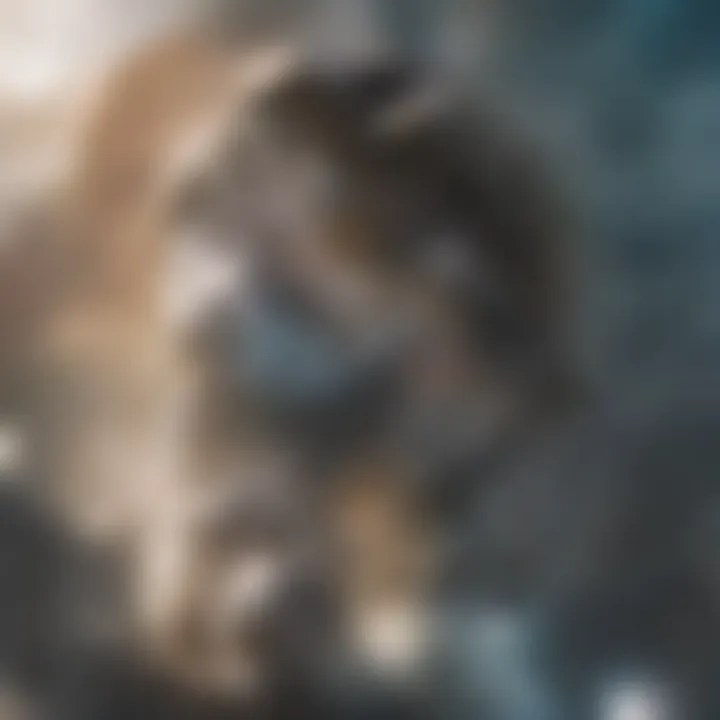
Understanding the different types of chain reactors is crucial due to their application in various chemical processes and industrial operations. These reactors can be categorized based on their operational mode and design philosophy. Each type exhibits unique characteristics that cater to specific needs in chemical synthesis, pharmaceuticals, and environmental applications. The selection of a particular type often involves weighing operational efficiency, cost, scale-up potential, and desired output quality.
Continuous Chain Reactors
Continuous chain reactors operate under a non-stop flow of reactants. These systems are essential for large-scale production where high throughput is required. Continuous reactors tend to offer better control over reaction conditions, thus ensuring a uniform product. This feature reduces the variability that can occur in batch processes, leading to a more consistent final product. The continuous operation also means less downtime, which is critical for optimizing production capacity.
Key elements of continuous chain reactors include:
- Steady State Operation: These reactors maintain a constant input and output of reactants and products.
- Enhanced Scalability: Easier to scale up due to their design, allowing increased production without significant redesign.
- Efficiency: They can operate at higher throughput levels compared to batch reactors, lowering the cost per unit produced.
Despite their advantages, continuous chain reactors require complex control systems to manage the constant input of materials, making initial set-up costs potentially higher.
Batch Chain Reactors
Batch chain reactors are designed for operations where reactants are added in discrete batches. This flexibility makes them suitable for processes with varying production needs. These reactors allow for diverse reactions in terms of scale and complexity.
In batch reactors, one can change parameters like temperature and pressure between runs, enabling experimentation and development of new products. Some of the notable features are:
- Versatility: Ideal for small-scale production or when the product design varies frequently.
- Process Customization: Easy to adapt methods depending on specific requirements of the batch.
- Lower Initial Investment: Generally less expensive to start due to simpler equipment demands.
Nevertheless, batch reactors have their downsides including higher labor costs per unit and longer production cycles, especially in comparison to continuous processes.
Hybrid Models
Hybrid models combine aspects of both continuous and batch operations. These innovative reactors can offer the flexibility of a batch system while maintaining some efficiencies of continuous reactors. A common application includes processes needing varying reaction times and conditions, where certain phases operate continuously while others use batch methods.
Some attributes of hybrid models include:
- Adaptability: They can cater to a wide range of chemical processes, balancing versatility and efficiency.
- Optimized Resource Use: Can enhance productivity by minimizing waste and maximizing throughput.
- Accelerated Development: Facilitates quicker testing of different operational conditions, which is beneficial for research.
Hybrid models reflect a growing trend toward integrating various reactor styles to meet specific industrial needs.
The type of chain reactor chosen significantly impacts both the efficiency and effectiveness of the chemical processes conducted within them. Selecting the appropriate reactor type allows industries to optimize production while maintaining high standards of quality.
Mechanisms of Reaction in Chain Reactors
Understanding the mechanisms of reaction in chain reactors is pivotal for optimizing their performance. This section focuses on the intricate processes that take place during reactions, which can significantly affect yield, efficiency, and scalability of production. Knowing these mechanisms allows researchers and engineers to develop better strategies for reactor design, operation, and troubleshooting.
Reaction Kinetics
Reaction kinetics plays an essential role in determining how fast a reaction occurs within the reactor. Kinetics is the study of the rates of chemical processes. In a chain reactor, the rate of reaction is influenced by several factors such as concentration of reactants, temperature, and presence of catalysts.
One must consider:
- Order of reaction: Different reactions exhibit different orders based on the relation between reactant concentrations and reaction rates.
- Activation energy: Reactants need sufficient energy to undergo a transformation. This is a critical factor to account for in reactor design.
- Catalytic activity: The type and amount of catalyst used can profoundly influence reaction rates. Therefore, efficient selection of catalysts is crucial in chain reactors.
Understanding these specifics allows for better control over how reactions are conducted, leading to more predictable outcomes. Moreover, optimizing these kinetics can enhance conversion rates and selectivity, which are vital in chemical manufacturing and research.
Energy Transfer Mechanisms
Energy transfer mechanisms are another critical aspect of chain reactors. These mechanisms ensure that reactants acquire adequate energy for the reaction to proceed efficiently. The following are key energy transfer concepts:
- Thermal conduction: Heat may be added or removed depending on the exothermic or endothermic nature of the reactions happening inside the reactor. Proper thermal management is crucial for maintaining optimal reaction conditions.
- Mass transfer: The movement of reactants and products must be efficiently managed to avoid bottlenecks. Poor mass transfer can limit reaction rates, therefore thorough analysis is necessary.
- Stirring or Agitation: Adequate movement within the reactor can promote better contact between reactants. Stirring mechanisms can affect the energy distribution and lead to more uniform conditions.
In summary, ensuring proper energy transfers within a chain reactor can significantly affect reaction rates and yield. Addressing these elements comprehensively aids in the design and implementation of more effective chain reactors.
Design Considerations for Chain Reactors
Design considerations are paramount when crafting effective chain reactors. Choices in materials, geometry, and scalability can significantly impact the reactor's performance, safety, and efficiency. It forms the foundational ground for enhancing the reliability and viability of the reactors. This section reviews important factors that inform the design and ultimately influence operational success in various applications.
Material Selection
The selection of materials for chain reactors is a critical step. Materials must withstand corrosive effects and high temperatures without degrading over time. Common choices include stainless steel, glass, and various alloys, each offering distinct advantages.
- Durability and Resistance: Materials like stainless steel provide high durability and corrosion resistance, beneficial for reactions involving aggressive reactants.
- Cost Considerations: Cost of the material factors into overall expenses. For large-scale applications, using economically viable materials can minimize costs without compromising safety.
- Reactivity and Compatibility: It is vital to ensure the selected materials do not react adversely with the contents of the reactor. Any unwanted reactions can lead to safety hazards or compromised product quality.
Reactor Geometry
The geometry of a chain reactor influences flow dynamics and reaction efficiency. Designing the reactor's shape can optimize mixing and heat transfer, leading to more effective chemical reactions. Key geometric considerations often include:
- Volume and Surface Area: The ratio of surface area to volume plays a pivotal role in reaction rates. Higher surface area can improve contact between reactants.
- Flow Patterns: Understanding how fluids move through the reactor is essential for ensuring consistent mixing and contact time among reactants. Designs like coiled reactors or multi-tubular systems can facilitate better flow management.
- Scalable Features: The reactor geometry should allow for scaling. Designs must be adaptable for larger volumes while maintaining performance metrics.

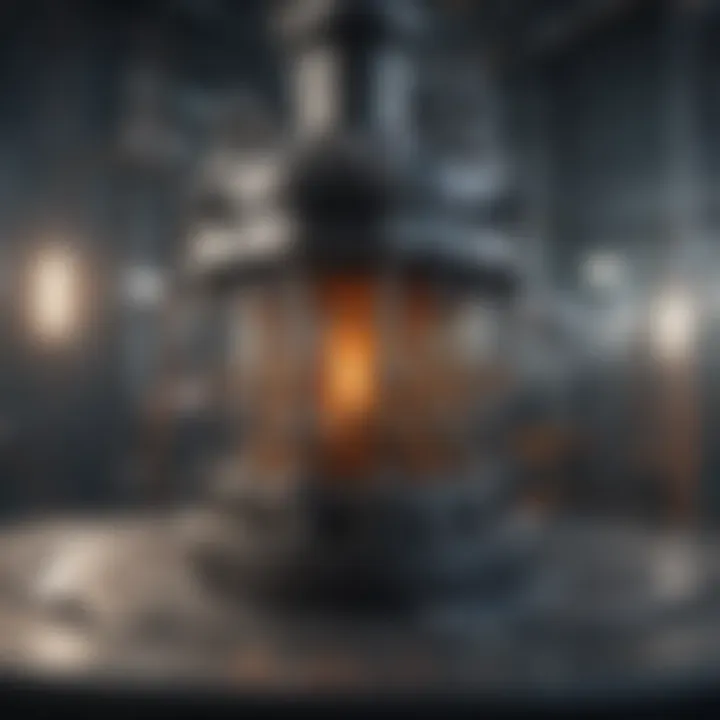
Scale-Up Challenges
Scaling up chain reactors from laboratory to industrial settings presents several challenges. Each step up in size brings complexities that must be managed to ensure efficiency and safety:
- Process Control: Maintaining fine control over reaction parameters such as temperature, pressure, and concentration becomes more complex as scale increases. Advanced monitoring systems are often necessary.
- Heat Management: Larger reactors can develop hot spots, which can lead to safety incidents. Effective heat exchange systems must be integrated into larger designs.
- Homogeneity of Mixtures: As the reactor size increases, ensuring uniform mixing becomes more challenging. Innovative designs are required to maintain reaction consistency.
The importance of material selection, reactor geometry, and addressing scale-up challenges cannot be overstated. These factors significantly determine the effectiveness and safety of chain reactors.
In summary, careful consideration of design elements is crucial for optimizing chain reactors. The chosen materials, geometric configuration, and strategies to tackle scale-up hurdles play significant roles in achieving desired outcomes.
Applications of Chain Reactors
Chain reactors have a wide array of applications that reflect their adaptability and efficiency in various fields. Their design and function cater to specific requirements in chemical processes, pharmaceuticals, and environmental practices. Understanding these applications is essential for researchers and professionals aiming to leverage the capabilities of chain reactors for innovative solutions. This section highlights the significance of these applications and their broader implications.
Chemical Synthesis
In the realm of chemical synthesis, chain reactors excel due to their ability to maintain a continuous process. This leads to higher efficiency and reduced waste compared to batch processes. The controlled environment within these reactors allows for precise adjustments of temperature, pressure, and concentration. As a result, reactions can be optimized for yield and selectivity.
Chain reactors are particularly useful for producing bulk chemicals, specialty chemicals, and fine chemicals. Moreover, they can be integrated with various catalysts to accelerate reaction rates. For instance, using a specific catalyst can enhance the transformation rate of reactants into desired products, thus driving down production costs.
"The continuous operation of chain reactors significantly minimizes downtime and boosts overall productivity within chemical synthesis processes."
Pharmaceutical Manufacturing
In pharmaceutical manufacturing, the demands for efficiency and precision are particularly high. Chain reactors offer a solution to these needs by allowing the synthesis of active pharmaceutical ingredients (APIs) in a controlled and consistent manner. This is crucial, as impurities in drugs can lead to severe health risks.
The adaptability of chain reactors also facilitates the production of a diverse range of compounds. Pharmaceutical companies benefit from the ability to scale processes without significant redesign. Furthermore, real-time monitoring systems can be incorporated, ensuring regulatory compliance while maximizing productivity. The integration of automation in these reactors further streamlines the manufacturing process.
Environmental Applications
Environmental applications of chain reactors are becoming increasingly important in a world focused on sustainability and ecological responsibility. These reactors are employed in the treatment of waste and in processes aimed at reducing emissions. They can convert organic waste into useful products effectively, thus promoting recycling of materials.
Additionally, chain reactors are utilized in processes such as biofuel production. By efficiently converting biomass into energy, they contribute to reducing reliance on fossil fuels. The continuous nature of these reactors allows for higher conversion rates and lower energy consumption, making them a preferred choice in environmental engineering.
In summary, the applications of chain reactors in chemical synthesis, pharmaceutical manufacturing, and environmental practices underscore their versatility and importance in modern technology. As the demand for efficient processes grows, understanding and utilizing chain reactors will be vital for advancing innovation across various industries.
Advantages and Limitations
By evaluating the advantages and limitations of chain reactors, one gains a clear understanding of their significance in various applications. This topic highlights how these reactors can enhance efficiency in chemical processes while also addressing potential hurdles faced during design and operation. Understanding both sides allows researchers and professionals to optimize usage and drive innovation.
Benefits of Chain Reactors
Chain reactors offer several benefits that can make them preferable in certain applications. Some of the key advantages include:
- Efficiency: Chain reactors enable continuous processing, which can lead to significant time savings. By maintaining a constant flow, reactants remain in continuous contact, thus promoting a steady state of reaction.
- Scalability: These systems can accommodate a variety of production scales. From small lab setups to large-scale industrial outputs, chain reactors can be designed to fit workload needs.
- Cost-Effectiveness: The operational cost can decrease due to reduced energy needs and minimization of raw material waste. This is particularly beneficial in processes where precision and efficiency are critical.
- Versatility: They can process a wide range of chemical reactions, including complex organic synthesis and polymerization processes. The adaptability of chain reactors facilitates diverse applications across fields like pharmaceuticals and materials science.
"The ability of chain reactors to adjust parameters in real time contributes significantly to process optimization in industrial settings."
In recent years, advancements in control systems and materials have further expanded the operational capabilities of chain reactors, making them even more beneficial for various applications.
Challenges Faced
Despite their many advantages, chain reactors also encounter specific challenges that require careful consideration. Some of the major challenges include:
- Complexity in Design: Developing an effective chain reactor involves intricate design considerations. Factors like flow dynamics and reaction kinetics need meticulous analysis to ensure optimal performance.
- Maintenance Requirements: Continuous operation often demands rigorous upkeep and monitoring. This can increase operational costs and require specialized staff for effective management.
- Process Control: Fluctuations in reaction conditions can lead to inconsistent product quality. Precise control systems are essential to maintain stability, which may involve additional investment in technology.
- Limited Flexibility: While chain reactors are versatile, modifications for specific processes can be time-consuming. Adjusting configurations often requires careful planning and can lead to downtime.
In summary, weighing the pros and cons of chain reactors leads to a better grasp of their role in chemical processes. Their capabilities can significantly improve efficiency, while the challenges faced require ongoing innovation and adaptation.
Technological Advancements
Technological advancements play a pivotal role in the evolution and efficiency of chain reactors. With the continuous progression in material science and automation, the performance of these reactors is significantly enhanced. The importance of this branch lies not only in improving operational efficacy but also in addressing the growing demands for sustainability and efficiency. Innovative technologies influence every aspect, from the design of the reactor to its day-to-day functions.
Innovation in Materials
The choice of materials in the construction of chain reactors is crucial for their performance and durability. The development of novel materials can lead to increased resistance against corrosion, temperature fluctuations, and chemical interactions. For example, the introduction of advanced ceramics and composites allows reactors to withstand harsher environments than traditional stainless steel. This leads to efficiency gains in several ways:
- Enhanced Lifespan: Materials that resist wear and tear extend the life of the reactor, reducing maintenance costs.
- Improved Reaction Rates: Certain materials can optimize heat transfer and reaction kinetics, resulting in higher yields.
- Lower Energy Consumption: More efficient materials often require less energy to maintain optimal operating conditions.
Innovations like nanotechnology also play a large role in creating materials with improved properties. By manipulating materials at the molecular level, it is possible to create reactors with superior characteristics, optimizing their operation across various applications.
Automation in Control Systems
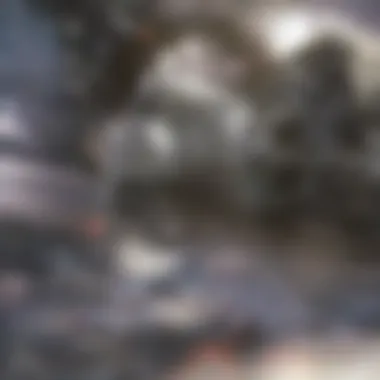
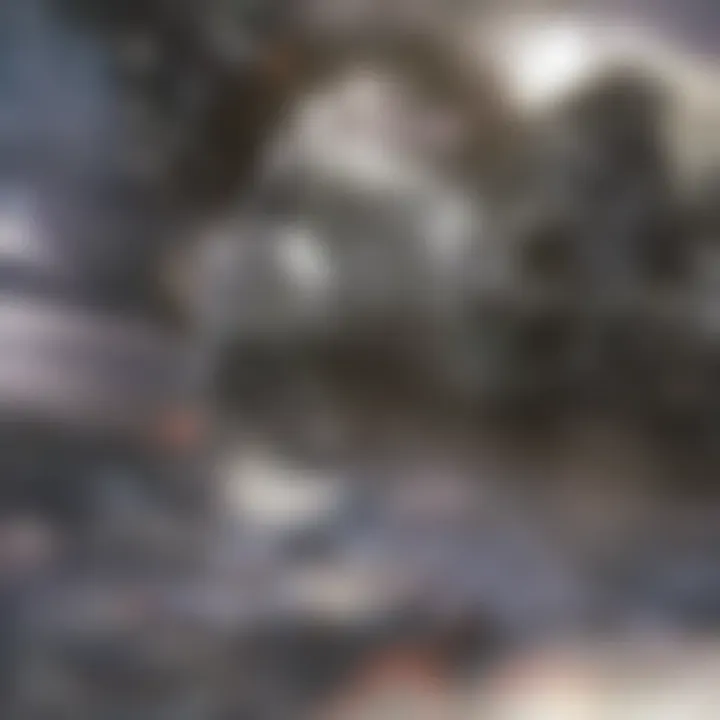
Automation within control systems is another significant advancement shaping the future of chain reactors. Advanced algorithms and control frameworks facilitate real-time monitoring and adjustments, enhancing process reliability and efficiency. Some of the benefits of automation include:
- Precision Control: Automated systems allow for precise control of reaction conditions, which can be adjusted dynamically based on real-time data.
- Safety Enhancements: Automation reduces human error and enhances safety protocols by enabling systems to respond to deviations swiftly.
- Data Collection: Intelligent systems can gather vast amounts of data over time, contributing to better process understanding and future optimization.
The integration of automation technologies, such as robotics and AI, can also revolutionize the operational capabilities of chain reactors. These technologies enable seamless operation and maintenance, making them an essential part of future reactor designs.
"Technological advancements in chain reactors not only impact efficiency but also shape their sustainability and operational resilience."
Investing in these advancements ensures that chain reactors remain at the forefront of chemical engineering and processing, meeting both current demands and future challenges.
Environmental Impact and Sustainability
Understanding the environmental impact and sustainability of chain reactors is crucial for developing effective strategies when implementing these systems across various industries. As society prioritizes ecological balance and resource efficiency, the design and operation of chain reactors must also innovate to minimize their carbon footprint and waste generation. The integration of sustainability principles into the reactor's lifecycle can significantly enhance overall environmental performance, thus fostering a better understanding among stakeholders of their responsibilities toward sustainable practices.
There are key elements, such as emissions, resource consumption, and waste by-products, that directly relate to the operational integrity of chain reactors. A proactive approach can yield numerous benefits, including compliance with regulatory standards, reduced operational costs, and the promotion of a positive public image. Moreover, effective sustainability practices contribute to the long-term viability of the reactor processes, benefitting not only the operators but also the broader community.
Adopting sustainable methods in the design and operation of chain reactors can lead to both economic benefits and environmental preservation.
Waste Management Strategies
Efficient waste management is a cornerstone of sustainable practices in chain reactors. Waste generated from reactions can vary widely, depending on the reactants and processes used. Therefore, it is essential to systematically manage this waste by employing a variety of strategies.
- Source Reduction: This involves modifying reactions to decrease the generation of waste at its origin. Choosing more efficient catalysts or optimizing reactant quantities can lead to significant waste reduction.
- Recycling: Certain by-products of chain reactions can often be reused in subsequent processes or as feedstocks for other chemical reactions. Incorporating recycling methods can help minimize waste and improve overall efficiency.
- Disposal Techniques: For waste that cannot be recycled, strategic disposal methods should be put in place. This includes utilizing proper treatment facilities that can neutralize harmful substances before disposal or safely integrated into ecosystems.
- Monitoring Systems: Continuous monitoring of waste generation and composition provides valuable data to adjust operations and implement corrective actions if necessary.
By conscientiously applying these strategies, industries utilizing chain reactors can significantly mitigate their environmental impact, aligning their operations with broader sustainability goals.
Sustainable Practices in Design
The sustainable design of chain reactors involves elements that extend beyond mere compliance with regulations. It encompasses the adoption of innovative technologies, materials, and strategies aimed at maximizing efficiency and reducing ecological footprints.
- Eco-friendly Materials: Using materials that are sourced responsibly can minimize environmental degradation. Advanced composites and recyclable materials in reactor construction help limit the ecological repercussions of traditional manufacturing processes.
- Energy Efficiency: Chain reactors should integrate energy-efficient systems. This could involve optimizing heat exchange mechanisms and utilizing technologies such as waste heat recovery, which can substantially reduce energy consumption.
- Life Cycle Assessment: By evaluating the entire lifecycle of the reactor, from conception through operation to decommissioning, designers can identify areas for improvement and ensure minimal environmental impact at each stage.
- Modular Design: Employing a modular approach allows for flexibility in scaling operations up or down based on current needs. Modular systems can often be more resource-efficient and adaptable to changing technologies.
Future Directions in Research
The field of chain reactors is at a critical juncture, where emerging trends and innovative studies pave the way for significant advancements. Understanding the future directions in this area is crucial for several reasons. First, with a variety of industrial applications, enhancing the efficiency and performance of chain reactors can lead to substantial economic benefits. Second, as environmental concerns grow, developing sustainable practices becomes ever more pertinent.
Research in this field not only focuses on optimization of existing technologies but also explores the incorporation of novel methodologies that can improve processes. This exploration will ultimately help address global challenges, such as resource conservation and waste reduction.
"Innovation in chain reactor research can redefine reactions, making them more efficient and environmentally friendly."
Emerging Trends
In the realm of chain reactors, several trends have emerged, indicating a shift towards greater complexity and efficiency. One trend is the integration of machine learning algorithms. These algorithms can analyze vast data sets from reactor operations, predicting optimal conditions for various chemical reactions. This leads to better control and reduces failures. The approach enhances productivity while ensuring safety.
Another trend is the incorporation of modular designs. Modular chain reactors allow for adaptability in processes, supporting varied scales without extensive redesign. Such flexibility makes them an attractive choice for manufacturers aiming to quickly respond to market demands or product variations.
Furthermore, the use of advanced materials, like graphene or specialized ceramics, is gaining attention. These materials often demonstrate superior performance under extreme conditions, increasing the longevity and efficiency of the reactors.
Potential Areas for Exploration
Several potential areas warrant deeper inquiry within the domain of chain reactors. First, the impact of biocatalysts in facilitating chemical reactions presents a compelling avenue for study. The application of enzyme-based processes could lead to greener production methodologies, minimizing harmful byproducts in chemical synthesis.
Second, examining the effects of process intensification also stands out as a vital area. This involves maximizing output while minimizing resource consumption. Researchers can explore various approaches, including enhanced mass transfer techniques or integrating multiple reaction stages into a single unit.
Lastly, the advantages of implementing real-time monitoring systems deserve attention. These systems can provide immediate feedback during reactor operations, promoting adjustments that can enhance yield or improve safety protocols. Real-time data also contributes valuable insights for future optimizations.
As this research progresses, the insights gained will not only enhance our understanding but will also serve to inform industry practices, guiding the next generation of chain reactors.
Closure
The conclusion of this article serves to encapsulate the key insights gleaned from the exploration of chain reactors. This section is critical not only as a recap but also as a lens focusing on the implications of the findings across various domains. By synthesizing information from previous sections, we underscore the importance of chain reactors in numerous applications from chemical synthesis to environmental management. The structured format of the discourse allows for a clear understanding of both the advantages these systems offer and the challenges they encounter within practical contexts.
Summary of Key Insights
Chain reactors are fundamentally versatile tools in both laboratory and industrial settings. Their capacity to facilitate continuous processes makes them particularly suited for large-scale chemical production while maintaining efficient energy use. Here are some key insights:
- Diverse Applications: Chain reactors occupy a pivotal role in pharmaceuticals, environmental science, and chemical engineering.
- Reaction Mechanisms: Understanding the kinetics and energy transfer mechanisms in these reactors enhances process optimization.
- Design Considerations: Material selection and reactor geometry directly affect performance and scalability, highlighting the need for careful design.
- Technological Advancements: Innovations in automation and materials are increasingly improving the efficiency and versatility of these systems.
The integration of sustainable practices in the design and operation of chain reactors is paramount for reducing environmental footprints. As researchers and practitioners examine these facets, the underlying principles and guidelines will empower future endeavors in chain reactor technology.
Implications for the Future
The exploration of chain reactors opens avenues for profound advancements in multiple fields. Continued research is essential in addressing existing challenges, such as:
- Enhancing Efficiency: Further studies into reaction kinetics and energy management can lead to significant performance improvements.
- Environmental Sustainability: Innovations aimed at minimizing waste generation and maximizing output are crucial as industries face increasing regulatory pressures.
- Broader Applications: As new catalysts and materials are developed, the potential applications for chain reactors will continue to grow.
- Interdisciplinary Collaboration: The intersection of chemistry, engineering, and environmental science will drive the future of chain reactor technologies.
In summary, the implications of this research stretch beyond academic boundaries, impacting industries heavily reliant on efficient processes. Stakeholders are encouraged to leverage the insights provided to cultivate further developments in chain reactor systems.