Modern Foundry: Innovations in Metal Casting
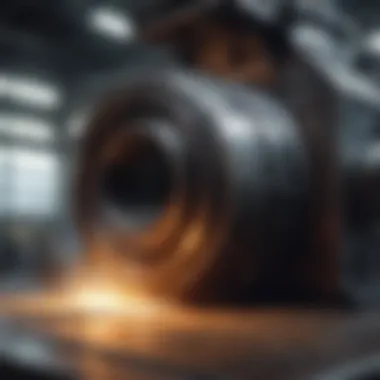
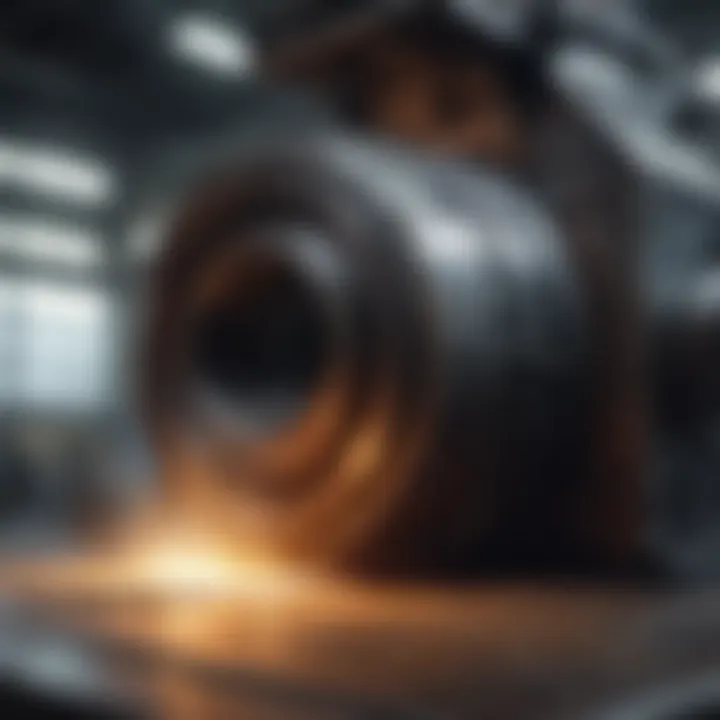
Intro
The landscape of manufacturing is continually evolving, and one area that has seen significant transformation is the foundry sector. This article delves into various aspects of modern foundries, highlighting their pivotal role in contemporary manufacturing processes. Traditional foundries utilized methods that have been refined over decades, but the modern foundry is different. It is shaped by advancements in technology, the rise of new materials, and emerging methodologies that push boundaries previously thought insurmountable.
Research Overview
Summary of Key Findings
The research conducted reveals several key findings about modern foundries:
- Technological Advancements: The incorporation of automated systems and digital tools has markedly improved efficiency and precision in metal casting.
- Sustainability: Modern foundries are now adopting practices that minimize waste and reduce environmental impact, aligning with global sustainability goals.
- Material Innovation: New alloys and materials are redefining possibilities within the foundry, allowing for stronger and more lightweight components.
- Integration of AI and Machine Learning: The use of artificial intelligence is streamlining operational processes and quality control, enhancing decision-making capabilities in the sector.
Each of these elements shapes the future of metal casting, making it crucial for stakeholders in the industry to stay informed about ongoing developments.
Significance of Research
Understanding the evolution of foundries is essential for several reasons. Firstly, it provides insights into the sustainability challenges that manufacturing faces today. Secondly, it reveals opportunities for innovation that can significantly improve production efficiency. Lastly, it helps stakeholders comprehend how technology can drive competitive advantages in metal casting.
Modern foundries symbolize not just a shift in method but also in mindset. The focus is now on remaining relevant in a fast-changing sector, where adaptability and forward-thinking are paramount.
Methodology
Research Design
The approach taken for this research combines qualitative and quantitative methods. The qualitative aspect involves analyzing case studies of notable modern foundry operations that showcase the adoption of new technologies and practices. The quantitative part includes gathering empirical data on production metrics before and after the implementation of these advancements.
Data Collection Methods
Data was collected from various reputable sources, including industry reports, academic journals, and interviews with professionals in the foundry sector. This multi-faceted approach ensures a comprehensive understanding of the modern foundry landscape.
By integrating these insights, stakeholders can align their strategies to meet the challenges and opportunities of the contemporary manufacturing environment.
Preface to Modern Foundry
Understanding the modern foundry is essential to grasp the evolution of contemporary manufacturing processes. This section addresses several key aspects including the operational changes, technological advancements, and the broader significance of foundries in the current industrial landscape. Modern foundries do not merely serve as production facilities; they embody the intersection of innovation and tradition, facilitating the transition from outdated practices to more efficient and sustainable methods.
Definition and Overview
A modern foundry can be defined as a facility where metals are melted, molded, and cast to create various components essential for multiple industries. Unlike traditional foundries, modern counterparts leverage sophisticated technology and new methodologies that enhance productivity and precision. At the core of a modern foundry is the integration of various technologies such as automation, robotics, and digital tools, which streamline operations and elevate the overall quality of the products produced.
The importance of precision is underscored by the wide range of applications these castings serve. They can be found in everything from automotive parts and aerospace components to intricate industrial machinery. Thus, the role of a modern foundry extends beyond mere manufacturing, greatly influencing the efficiency and performance of final products.
Historical Context
The history of foundries traces back thousands of years, marking a critical point in the transition from ancient craftsmanship to modern manufacturing. Initially, foundries were simple setups where artisans melted metals in rudimentary furnaces. These early foundries primarily focused on small-scale production, which limited the range and complexity of items manufactured. With the advent of the Industrial Revolution in the 18th century, the industry began to experience significant changes. The introduction of steam power and mechanization led to larger facilities with increased production capabilities.
As time progressed, innovations in materials and processes became more pronounced, leading to the formulation of specialized alloys and improvement in casting techniques. In the late 20th and early 21st centuries, the push toward automation and sustainable practices transformed the foundry landscape even further. Today, modern foundries are not just about casting metals; they serve as hubs for research, experimentation, and the implementation of advanced manufacturing technologies. This historical evolution sets the stage for understanding the complex dynamics and significance of modern foundries in today’s industrial context.
Technological Innovations in Foundries
Technological innovations are essential in modern foundries. They enhance efficiency, reduce costs, and improve the quality of metal casting. The adaptation of new technologies shifts the industry from traditional methods. Innovations also respond to the growing demands for more sustainable and precise production processes. As foundries embrace these advancements, they can better compete in a challenging market.
Additive Manufacturing Techniques
Additive manufacturing is transforming how manufacturers approach casting. This technique, often referred to as 3D printing, allows the creation of complex geometries that were difficult or impossible with traditional methods. For instance, Selective Laser Sintering (SLS) and Fused Deposition Modeling (FDM) are two methods that enable the rapid prototyping of mold designs.
Benefits of additive manufacturing in foundries include:
- Reduced material waste, as only the necessary amount of material is used.
- Faster production times, allowing for quicker turnaround on projects.
- Enhanced design flexibility, fostering innovation in product development.
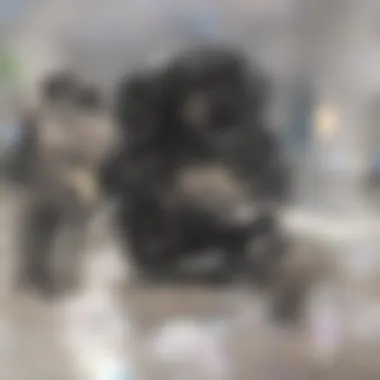
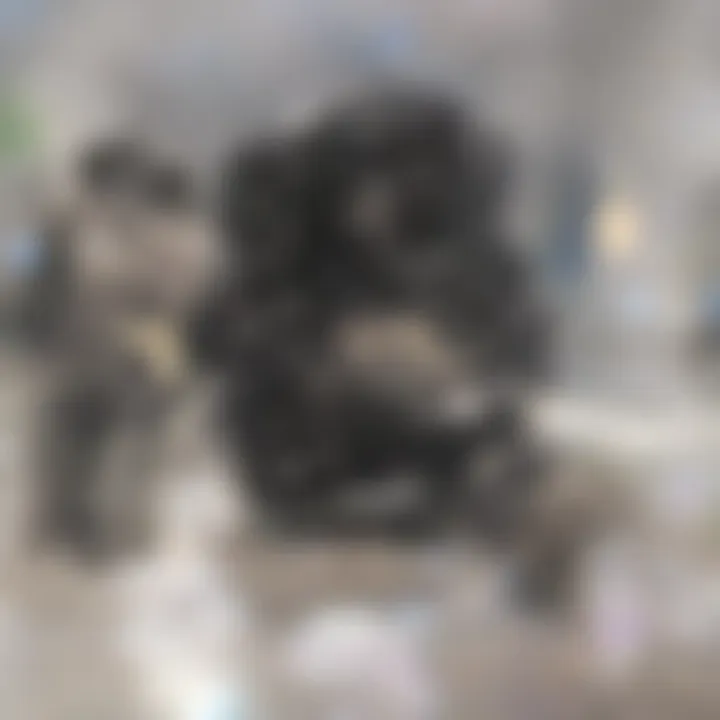
While additive manufacturing holds great potential, challenges remain. These include cost factors related to machinery and materials, as well as the learning curve associated with integrating new technologies into established processes.
Advanced Automation Solutions
The implementation of advanced automation in foundries optimizes operations. Automation can streamline processes, reduce human error, and increase production rates. Technologies like automated pouring systems and intelligent molding reduce manual labor while ensuring consistent quality in cast products.
Key advantages of automation include:
- Improved safety by minimizing human exposure to hazardous environments.
- Higher consistency in production, leading to fewer defects.
- Better resource management, optimizing energy usage and materials.
However, the transition to automated systems might require significant initial investment and training. Foundries must consider how to balance automation with the skilled labor necessary for quality assurance.
Integration of Robotics
Integrating robotics into foundry processes represents a significant advancement. Robots can perform repetitive and labor-intensive tasks, such as handling molten metal or performing inspections, which increases precision and efficiency.
The role of robotics includes:
- Material handling, which reduces the risk of injury while moving heavy loads.
- Quality inspections, using advanced vision systems to detect defects that human inspectors might miss.
- Complex assembly tasks, which can be performed with high levels of accuracy and speed.
Robotic systems can also adapt to changing production needs, making them a versatile asset in modern foundries. However, the effective integration of robotics requires careful planning and design to ensure compatibility with existing processes.
"The role of technology in foundries cannot be understated. Innovations drive efficiency and sustainability, ensuring the industry can meet modern demands."
Materials Used in Modern Foundries
The selection of materials in modern foundries is crucial in defining the quality and performance of cast products. This section discusses various materials, focusing on ferrous and non-ferrous alloys, as well as the evolving trend towards sustainable materials. The benefits and considerations of each category will help readers understand their implications on production efficiency, environmental impact, and product characteristics.
Ferrous Alloys
Ferrous alloys contain iron as the primary constituent. They are noted for their high strength and durability, making them essential in various applications. Common ferrous alloys include cast iron and steel, which are widely used in automotive and construction industries. Cast iron, in particular, has excellent casting properties, allowing for complex shapes to be manufactured with relative ease. Steel, on the other hand, offers superior ductility and tensile strength, suitable for structural applications.
When considering ferrous alloys, it is important to account for factors such as carbon content, which greatly affects the material properties. Higher carbon content increases hardness but reduces ductility. Thus, understanding the desired characteristics of the final product will influence alloy selection.
Non-Ferrous Alloys
Non-ferrous alloys do not contain a significant amount of iron. This category includes aluminum, copper, brass, and bronze, among others. These materials are prized for their unique properties, such as lower weight, corrosion resistance, and electrical conductivity. Aluminum alloys are widely used in aerospace and automotive applications due to their lightweight nature, which helps improve fuel efficiency.
Copper and its alloys, like brass and bronze, are used extensively in electrical applications due to their high conductivity and resistance to corrosion. The choice of non-ferrous materials often depends on the specific requirements of the product, such as strength, weight, and resistance to environmental factors.
An important consideration is the processing method, as some non-ferrous alloys may require specialized techniques to achieve optimal results during casting.
Sustainable Materials
Sustainability in material selection is becoming increasingly essential in foundry practices. The use of sustainable materials not only reduces environmental impact but also aligns with modern manufacturers' goals of corporate responsibility. One significant trend is the recycling of scrap metal, which can reduce the need for virgin materials and decrease energy consumption during production.
Additionally, there is growing interest in bio-based materials and composites. These materials demonstrate lower environmental footprints while still meeting performance standards. For instance, some foundries are experimenting with bio-resins or other renewable feedstocks to produce mold materials, significantly reducing dependence on fossil-based resources.
Sustainable material usage often enhances the reputation of foundries in the marketplace, appealing to a customer base that values eco-friendly practices.
The modern foundry prioritizes the use of sustainable materials, which has implications for product lifecycle management and overall industry practices.
The Role of Simulation in Foundry Processes
In modern foundry operations, simulation has assumed an indispensable role. Its incorporation into the foundry processes profoundly enhances efficiency and precision. Simulation enables various stages of metal casting to be analyzed and optimized before actual production begins. The primary benefit of using simulation is the ability to visualize potential outcomes, identify issues, and implement solutions in a virtual environment. This approach minimizes errors and reduces materials waste, ultimately leading to cost savings and improved product quality.
The benefits of simulation can be outlined as follows:
- Accuracy in Design: Simulation tools allow designers to create precise models of cast products. This precision aids in ensuring that the final output meets the required specifications.
- Risk Mitigation: By simulating different scenarios, engineers can predict potential failures or defects in a controlled environment. Understanding these risks helps in proactively addressing them before reaching the physical production stage.
- Time Efficiency: Simulation reduces the time spent on prototyping. Manufacturers can test multiple designs and configurations quickly, which is critical in fast-paced markets.
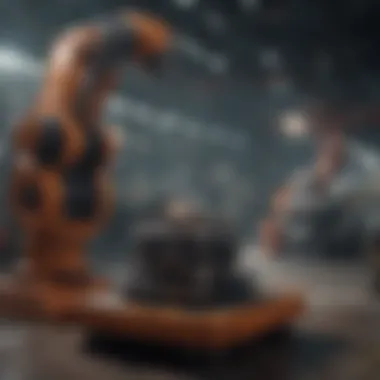
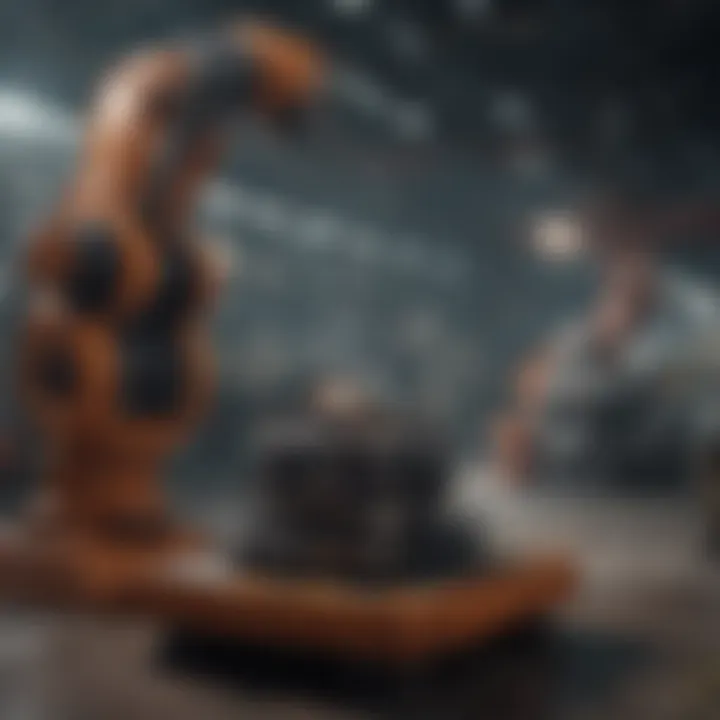
Given these factors, the role of simulation in foundries extends beyond mere convenience. It signifies a strategic shift towards data-driven decision-making and rigorous scientific methodology in metal casting.
Computer-Aided Design (CAD)
Computer-Aided Design, commonly known as CAD, is a fundamental element in the modern foundry simulation process. CAD software provides the tools necessary for creating detailed 3D models of components that are to be cast. This software not only enhances design accuracy but also facilitates the visualization of complex geometries.
One notable advantage of CAD in foundries is its ability to incorporate specifications directly from clients or engineers. It allows for quick modifications to designs, thereby making adjustments easier and less time-consuming. Furthermore, CAD systems can integrate with other software solutions, such as those used for casting simulations, to create a seamless workflow from design to production.
Casting Simulation Software
Casting simulation software serves to augment the traditional practices of foundry work. This software simulates the entire casting process, enabling engineers to foresee how molten metal behaves within a mold. Key features of these programs include the ability to analyze flow patterns, assess cooling rates, and identify potential solidification defects before production begins.
Utilizing casting simulation software offers numerous advantages:
- Thermal Analysis: Users can examine heat distribution and cooling rates to predict how a casting will solidify. This insight is vital for avoiding defects such as shrinkage.
- Flow Simulation: Understanding how molten metal fills molds helps in optimizing gating systems. This optimization reduces air entrainment and minimizes material wastage.
- Stress Analysis: Engineers can predict the stresses that cast components will encounter during service. Such knowledge is critical for ensuring long-term performance and reliability.
Sustainability Practices in Foundries
Sustainability practices in foundries are increasingly critical, as industries face heightened scrutiny regarding their environmental impact. The modern foundry must balance efficient production with responsible stewardship of resources. Adopting sustainable practices not only minimizes the ecological footprint but can also lead to economic advantages. Cost savings through efficiency, compliance with regulations, and enhanced public perception are prominent motivations for implementing these practices.
Waste Reduction Strategies
Waste reduction is a cornerstone of sustainability in foundries. It focuses on minimizing scrap metal and other byproducts during production. Foundries often employ methods such as lean manufacturing principles. Here are some common strategies:
- Process Optimization: Streamlining operations to use materials more efficiently reduces excess waste.
- Material Substitution: Switching to materials that generate less waste during processing can be beneficial. For instance, using eco-friendly binding agents can minimize hazardous waste.
- Byproduct Recovery: Implementing systems to capture and reuse byproducts can help transform potential waste into valuable resources.
"Waste is a resource in the wrong place." This highlights the idea that through innovation, waste materials can be utilized effectively.
Energy Efficiency Improvements
Energy efficiency improvements are vital to enhance the sustainability of modern foundries. The demand for energy is high in metal casting, but by adopting more efficient practices, foundries can significantly reduce their consumption. Some approaches include:
- Upgrading Equipment: Using state-of-the-art machinery that requires less energy can lead to substantial savings over time.
- Heat Recovery Systems: Capturing waste heat for use in other processes can drastically cut energy needs. This practice not only improves efficiency but also reduces operational costs.
- Smart Energy Management Systems: Integrating smart technologies that monitor energy usage allow for real-time adjustments, ensuring optimal energy consumption.
Recycling of Materials
Recycling is another key aspect of sustainability in foundries. The recycling of scrap metal can significantly reduce the need for virgin materials. Foundries that adopt robust recycling protocols contribute to a circular economy. Factors to consider include:
- Closed-loop Recycling: This process involves reprocessing scrap from the casting process back into production. This limits waste and reduces sourcing needs.
- Partnering with Recycling Firms: Collaborating with specialized firms can streamline recycling efforts and improve overall efficiency.
- Employee Training: Educating all staff on the importance of recycling can foster a culture of sustainability within the foundry.
Quality Control and Standards
Quality control and standards are critical components in the operation of modern foundries. They ensure that products meet specific requirements, enhancing reliability and customer satisfaction. The effectiveness of quality control directly impacts the overall efficiency of the foundry operations, production costs, and market competitiveness. Establishing stringent standards is essential as it helps to maintain consistency in product quality. Moreover, these practices protect companies from liability issues associated with defective products.
Inspection Techniques
Inspection techniques form the backbone of quality control in foundries. Various methods are employed to assess the integrity and quality of cast components. These techniques include visual inspections, dimensional checks, and non-destructive testing (NDT).
- Visual Inspections: Simple yet effective, these assessments can reveal surface defects, cracks, and other visible flaws. Inspectors examine components closely, looking for any aberrations that may compromise quality.
- Dimensional Checks: This technique involves measuring the physical dimensions of a product against predetermined tolerances. Tools like calipers and micrometers are commonly used in this process. Accurate dimensional checks ensure that products fit correctly in their intended applications.
- Non-Destructive Testing (NDT): NDT methods, such as ultrasonic testing or radiography, allow for the evaluation of materials without causing damage. These advanced techniques help in detecting internal flaws that may not be visible on the surface. This ensures that even the most critical components adhere to safety and performance standards.
"Quality control is not just a technical requirement but a fundamental necessity for long-term success in the foundry industry."
Quality Assurance Protocols
Quality assurance protocols in modern foundries encompass a systematic approach to ensuring product quality throughout the manufacturing process. These protocols guide workers in maintaining consistent quality and provide a roadmap for corrective actions when deviations occur.
Key elements of quality assurance protocols include:
- Standard Operating Procedures (SOPs): Clearly defined SOPs ensure that every step of the production process meets the required standards. Employees are trained and guided on these procedures to minimize errors.
- Documentation and Traceability: Keeping detailed records of materials, processing parameters, and inspection results is crucial. This documentation is essential for tracing any defects back to their source, facilitating continuous improvement efforts.
- Audits and Compliance Checks: Regular internal and external audits verify that processes align with stipulated standards. Compliance with industry guidelines, such as ISO 9001, reinforces quality assurance efforts.
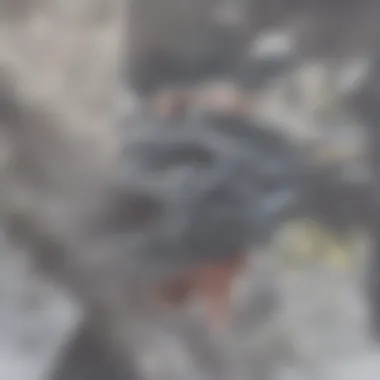
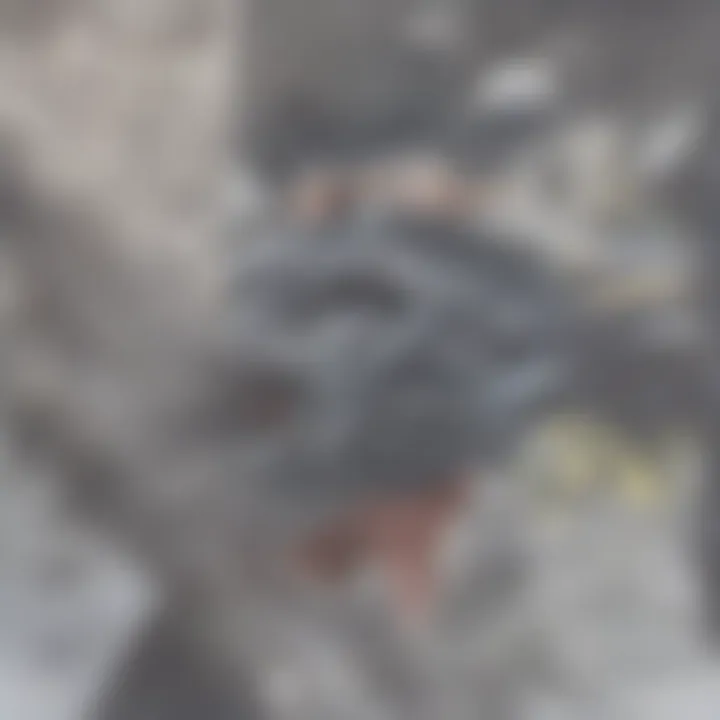
Economic Impact of Modern Foundries
The economic significance of modern foundries cannot be understated. They serve as a crucial segment in the broader manufacturing industry, impacting both local and global markets. Modern foundries produce various metal components essential for different sectors, including automotive, aerospace, and construction. This section examines the economic aspects that define modern foundries, addressing market trends, growth opportunities, and the competitive landscape.
Market Trends and Growth Opportunities
In today’s market, several trends affect how foundries operate. The demand for lightweight, strong components is increasing, driving innovations in material science. Advanced alloys and metal composites are gaining traction. They offer superior properties while meeting the stringent requirements of various applications. This trend opens numerous growth opportunities for established foundries willing to adapt and innovate.
Additionally, as sustainable practices become more integral, foundries are expected to adjust their operations to reduce waste and minimize energy consumption. Companies adopting green technologies could see an influx of investment, appealing to environmentally conscious consumers and regulators alike. These advancements foster not only operational efficiency but also potential new revenue streams.
Moreover, the growth of additive manufacturing and other digital fabrication techniques presents yet another avenue to explore. Foundries that integrate these technologies can improve design capabilities and enhance production efficiency. Such shifts not only create benefits but also encourage market expansion.
In summary, modern foundries are at the intersection of traditional manufacturing and cutting-edge technologies, positioning themselves for significant growth in a rapidly evolving landscape.
Global Competitiveness
The global competitiveness of foundries hinges on a variety of factors. Countries that invest heavily in innovation, research, and skilled labor tend to excel in producing quality metal components. Regions like Asia, particularly China and India, are rising as powerhouses in the foundry sector. They capitalize on lower labor costs and an increasing domestic demand for manufactured goods.
Furthermore, many foundries are forming strategic partnerships to enhance their competitive edge. Collaborations between academia and industry help in developing new technologies and processes, ensuring continuous innovation.
Economic policies also play a pivotal role. Government incentives for sustainable practices can elevate a country's foundries in the global market. Firms that adapt to regulations and invest in sustainability not only comply with standards but also showcase their commitment to responsibility, boosting their attractiveness to clients.
"The foundry industry is not just about traditional processes; it is an evolving landscape driven by innovation and sustainability strategies that redefine competitiveness."
Ultimately, modern foundries must navigate these competitive challenges through adaptation and strategic foresight. Being aware of market shifts and adjusting accordingly will prove essential for sustained economic success.
Future Directions in Foundry Technology
The landscape of foundry technology is evolving rapidly and is increasingly shaped by innovative practices and methodologies. Understanding the future directions in foundry technology is crucial for stakeholders in the metal casting industry. These advancements not only promise to optimize production processes but also contribute significantly to sustainability and economic competitiveness. The integration of new technologies is reshaping the entire workflow in foundries, making it vital for professionals to stay informed and adapt accordingly.
Emerging Technologies
Emerging technologies represent a vital aspect of the future of foundry practices. They encompass a range of advancements, from innovative materials to revolutionary production techniques. Key areas include:
- 3D Printing: Also known as additive manufacturing, 3D printing has begun to transform how foundries produce parts. It allows for intricate designs that were once impossible with traditional methods.
- Artificial Intelligence: Integration of AI into foundry processes improves predictive maintenance and enhances quality control. AI algorithms can analyze data in real-time, identify patterns, and predict equipment failures before they occur.
- Digital Twin Technology: This concept involves creating a digital replica of physical foundries. It aids in process optimization and efficiency, allowing for better resource management.
These technologies not only boost efficiency but also allow for customization and adaptability in production. Foundries employing such technologies may significantly reduce lead times and costs, while increasing overall product quality.
Industry 4. Integration
The concept of Industry 4.0 emphasizes the interconnectivity between machines, systems, and data. In foundries, this integration is particularly beneficial as it enhances operational accuracy and efficiency. Key factors include:
- Smart Manufacturing: By utilizing IoT devices, foundries can achieve real-time insights into production. This leads to better decision-making and streamlined operations.
- Data Analytics: Leveraging big data helps foundries to gain deeper insights into their processes. It allows for enhanced quality control and waste reduction strategies.
- Flexible Automation: Modern foundries are moving towards flexible automation systems that can adapt to varying production needs without significant downtime.
Such integration of Industry 4.0 principles not only advances manufacturing capabilities but also contributes to sustainability by optimizing resource use.
"The future of foundry technology is not just about new machines; it's about integrating intelligence and connectivity across the entire production process."
As foundries embrace these future directions, they position themselves to remain competitive in an ever-evolving industry.
Ending
The conclusion serves as a crucial component in synthesizing the various themes presented throughout the article. It encapsulates the insights drawn from the comprehensive examination of modern foundries. In this section, the importance of understanding modern foundries cannot be overstated. These facilities are pivotal in shaping the future of manufacturing as they embrace new innovations and contribute to economic growth.
Summary of Key Insights
In reviewing the key insights derived from the article, we observe several noteworthy points:
- Technological Advancements: Modern foundries have integrated cutting-edge technologies like additive manufacturing and automation. These innovations enhance efficiency, reduce waste, and improve product quality.
- Material Selection: The use of diverse materials, including sustainable options, helps foundries meet regulatory requirements and industry demands. Understanding material properties is vital for successful casting processes.
- Simulation Tools: The application of computer-aided design and casting simulation software significantly reduces errors and promotes cost-effective production.
- Sustainability Practices: Foundries are increasingly focusing on sustainable practices. Waste reduction and energy efficiency not only benefit the environment but also contribute to operational cost savings.
- Economic Impact: Modern foundries play a significant role in global markets. Their ability to adapt and innovate directly correlates with their competitiveness in the industry.
Final Thoughts on the Future of Modern Foundries
Looking ahead, the future of modern foundries is promising yet requires continuous adaptability to emerging trends. As Industry 4.0 gains momentum, the integration of intelligent systems will redefine operational capabilities. Being attuned to industry trends, materials science evolution, and advancements in simulation technology will be essential for sustaining competitive advantage.
Furthermore, the continued focus on sustainability will likely reshape practices within the industry. This commitment not only aligns with global initiatives but also resonates with consumer preferences for environmentally friendly products.
"Modern foundries must embrace innovation not just for profit but for long-term viability in a rapidly changing world."