Electric Rock Drills: Performance, Safety, and Sustainability
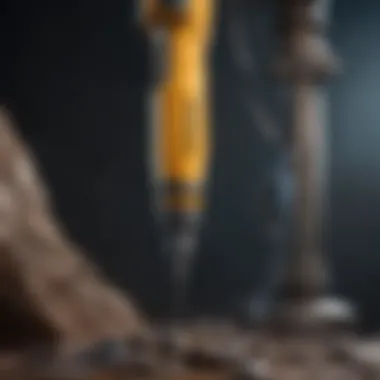
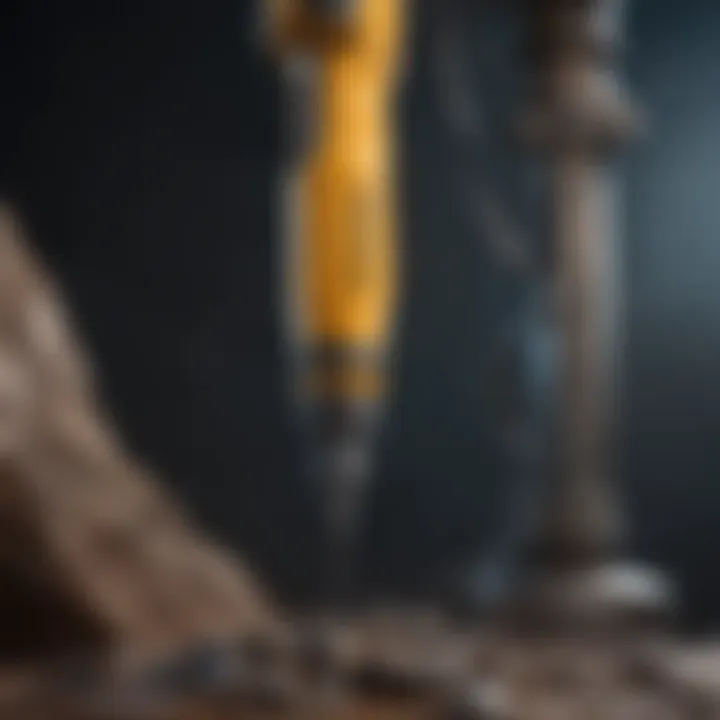
Intro
In recent years, the field of construction and excavation has seen significant advancements, particularly in the tools used for rock drilling. Electric rock drills have emerged as a vital component in this evolution. This technology blends efficiency with environmental considerations, aligning with modern mandates for sustainability. Understanding the operational nuances of electric rock drills is essential for professionals engaged in engineering and construction disciplines.
The focus of this article is to provide a detailed examination of electric rock drills, exploring their design, operational mechanisms, applications, and the safety protocols necessary for their effective use. We aim to deliver critical insights that are indispensable for researchers, educators, and industry practitioners seeking to enhance productivity while minimizing ecological footprints.
Research Overview
Summary of Key Findings
Electric rock drills demonstrate superior performance metrics over traditional pneumatic models. Notably, their operational costs are lower, and they produce reduced noise levels, making them suitable for urban projects where noise pollution is a concern. Furthermore, advancements in battery technology have enabled these drills to operate efficiently for longer periods before needing a recharge. This shift not only boosts productivity but also favors eco-friendly practices, as electric models emit no exhaust gases.
Other studies highlight the importance of ergonomics in design. Modern electric rock drills are being engineered with operator comfort in mind, reducing fatigue and injury risk during prolonged use.
Significance of Research
The significance of electric rock drills in construction cannot be understated. As industries increasingly adopt sustainable solutions, understanding these tools becomes essential for compliance with environmental regulations and for leading the charge towards greener operational practices. Additionally, comprehending their design and functionality aids in selecting the appropriate model for specific tasks, ultimately optimizing project outcomes.
Methodology
Research Design
This article employs a qualitative approach, integrating case studies and expert interviews. By analyzing various projects where electric rock drills have been implemented, deeper insights into their long-term benefits and challenges can be uncovered. Detailed evaluations of operational performance metrics provide a solid foundation for recommendations.
Data Collection Methods
Data was gathered through multiple channels, including:
- Field observations in construction sites
- Interviews with industry experts and professionals
- Comprehensive literature review of existing research
These methods allowed for an accurate representation of current trends and practices surrounding electric rock drills, ensuring a thorough understanding of their role in modern excavation.
Foreword to Electric Rock Drills
Electric rock drills have emerged as a pivotal technology within the fields of construction and mining. Their importance cannot be overstated, as they significantly improve efficiency and precision in drilling operations. This section will elaborate on the definition and historical context behind electric rock drills, providing a foundational understanding of their role in modern applications.
Definition and Overview
Electric rock drills are specialized tools used for penetrating various materials, primarily rock or hard soil. Unlike pneumatic drills, which rely on compressed air, electric rock drills operate using electric power. This mechanism allows them to deliver more consistent torque and speed, leading to enhanced performance and reduced downtime. Furthermore, the absence of air pressure systems minimizes potential maintenance issues, offering improved reliability. They are widely utilized in several applications ranging from construction to geological surveys, showcasing their versatility and importance in the industry.
Historical Context
The development of electric rock drills traces back to the industrial revolution when technological advancements began to facilitate mechanized drilling processes. Early drills, initially powered by steam or hand, evolved as electrical engineering progressed. The advent of power sources such as electric motors allowed for lighter designs and more efficient operation. Over the decades, as mining and construction techniques evolved, so did electric rock drills. The shift from pneumatic to electric systems marked a significant turning point. By the late 20th century, electric rock drills had firmly established themselves as a standard in the industry, leading to innovations that continue shaping the practices we see today.
In summary, electric rock drills represent a significant advancement in drilling technology, playing a crucial role in enhancing operational efficiency across various sectors.
Technical Specifications
Understanding the technical specifications of electric rock drills is vital for evaluating their performance, efficiency, and suitability for various applications. These specifications encompass key elements like power supply mechanisms, motor types, and drill bit variations, each contributing to the drill's overall functionality and effectiveness. Knowledge of these specifications allows professionals in construction and mining to select the appropriate equipment tailored to their specific needs, enhancing productivity and operational efficiency.
Power Supply Mechanisms
Power supply mechanisms are fundamental to the operation of electric rock drills. These mechanisms determine how energy flows to the motor and ultimately affects the drill's performance. Two primary types of power supply systems exist: corded, which relies on a direct electrical connection, and battery-powered systems that offer mobility without the constraints of cords.
Corded electric rock drills generally provide consistent power, leading to higher efficiency and longer operation times. They are especially beneficial for intensive drilling tasks in fixed locations. Conversely, battery-operated drills offer significant flexibility and portability. However, factors such as battery life and charging times must be considered when opting for these systems.
The choice of power supply impacts not only the drill's operational capacity but also its suitability for specific tasks in varied environments.
Key considerations in selecting a power supply mechanism include:
- Power Output: Measured in Watts, higher values correlate to better performance.
- Durability: The robustness of power systems to withstand harsh conditions.
- Versatility: Ability to perform multiple functions or drill various materials.
Motor Types
The type of motor employed in electric rock drills significantly influences their performance characteristics. Common motor configurations include brushed and brushless motors.
Brushed motors have been traditionally used due to their simpler construction and lower costs. They provide adequate torque and are reliable for many applications. However, they tend to produce more heat and require more maintenance over time.
On the other hand, brushless motors are increasingly favored. They offer higher efficiency, increased power-to-weight ratios, and lower maintenance requirements. This efficiency translates into longer usage times and reduced heat generation during operation. Understanding these motor types allows professionals to make informed choices about maintenance and operational expectations.
Drill Bit Variations
The choice of drill bit is another critical aspect of electric rock drills. Different applications demand various drill bit configurations to achieve optimal results. Key variations include:
- Carbide-tipped bits: Ideal for hard materials like concrete or stone.
- Diamond bits: Offer superior cutting effectiveness for tough rocks and are favored in mining applications.
- Twist drill bits: Common for general-purpose drilling in softer materials.
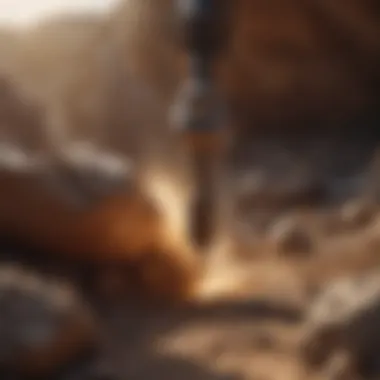

Each drill bit type has unique characteristics that influence performance factors like drilling speed, penetration depth, and material compatibility. Furthermore, considerations such as wear resistance and heat dissipation also play important roles in selecting the right bit for a given task.
In summary, the technical specifications of electric rock drills are crucial for their effective application in various settings, directly impacting performance, efficiency, and the overall success of drilling operations.
Types of Electric Rock Drills
The section on types of electric rock drills is crucial as it lays the foundation for understanding specific tools available in the market. Knowledge about various categories helps operators and engineers select the most suitable drill for their needs. Each type of electric rock drill has unique features, advantages, and operational contexts that make it valuable for particular applications. Exploring these differences aids in informed decision-making and enhances efficiency in drill operation.
Rotary Electric Rock Drills
Rotary electric rock drills are primarily designed for drilling in rock formations by using a rotational motion. These drills work by effectively rotating a drill bit against the rock surface, allowing for efficient penetration. The main advantage of rotary drills is their ability to penetrate hard rock layers with precision. They can be used in various applications, including construction, mining, and geological surveys.
Some key characteristics of rotary electric rock drills include:
- High drilling speed: These drills typically achieve faster drilling rates compared to other types, which can improve overall productivity.
- Versatility: Rotary drills can be equipped with different types of drill bits, allowing them to adapt to various rock conditions.
- Less maintenance: They require less frequent maintenance due to fewer moving parts involved in the drilling process.
However, rotary drills may face limitations in softer materials, where penetration can be slower and less efficient. Overall, their robustness makes them a preferred option in many heavy-duty applications.
Percussion Electric Rock Drills
Percussion electric rock drills operate using a hammering action combined with rotation. This dual functioning enhances their ability to break and penetrate through hard materials. The hammer mechanism delivers powerful blows at regular intervals as the drill bit rotates, making it particularly effective in drilling through tough rock.
The benefits of percussion drills include:
- Enhanced breaking capability: They can shatter rock better than rotary drills alone, especially in very hard geological formations.
- Efficiency in boulder drilling: When encountering hard spots, percussion drills can continue to progress efficiently compared to rotary drills.
- Dual operational modes: Many percussion drills can switch between rotary and percussive modes, offering flexibility based on situational needs.
Despite their advantages, percussion drills can lead to higher vibrations and noise levels, necessitating considerations for operator well-being and equipment longevity.
Top-Hammer vs. Down-The-Hole Drills
When it comes to choosing between top-hammer and down-the-hole (DTH) drills, understanding their operational principles is essential.
Top-hammer drills have the hammer located above the drill bit. They work by delivering impacts down through the drill string, breaking the rock at the bit. This type is common in surface applications, such as quarrying and road construction.
- Pros: Often lighter and more portable than DTH drills; suitable for varied ground conditions.
- Cons: Limited penetration depth; less effective in very hard rock.
Down-the-hole drills, in contrast, have the hammer positioned directly at the drill bit. This design allows for a more efficient transfer of impact energy, facilitating deeper drilling.
- Pros: Excellent performance in hard, deep rock formations; faster drilling rates in demanding environments.
- Cons: Typically bulkier, making them harder to move; higher operational costs due to heavy equipment needs.
Each type suits specific drilling applications, and understanding these differences can significantly influence operational success and efficiency. Selecting between them requires a detailed assessment of the drilling environment, rock hardness, and project requirements.
Operational Efficiency
Operational efficiency is a crucial aspect in the utilization of electric rock drills, impacting both productivity and cost-effectiveness. The concept encompasses how effectively resources, including time, materials, and energy, are used to achieve desired outcomes. In this context, electric rock drills must not just perform tasks; they must do so efficiently to justify their operational costs and improve overall project timelines.
Performance Metrics
Performance metrics serve as the yardstick for evaluating the efficacy of electric rock drills in various applications. These metrics include drilling speed, penetration rate, and energy consumption.
- Drilling Speed: Refers to the rate at which the drill can make a hole. Higher speeds generally translate into shorter project durations, meaning projects can be completed faster.
- Penetration Rate: This metric indicates how quickly a drill can penetrate various rock types. Faster penetration can significantly enhance productivity on construction and mining sites.
- Energy Consumption: Monitoring the energy used during operation has become increasingly important, especially with the focus on sustainability. Drills that optimize energy use reduce costs and lower environmental impacts.
To track effectiveness, operators often use a combination of these metrics to assess the performance of different drill types. Such analysis also aids in making data-driven decisions for equipment selection.
Comparative Analysis with Pneumatic Drills
Comparing electric rock drills with pneumatic drills reveals significant differences in operational efficiency.
- Energy Source: Electric drills are powered directly by electricity, which can lead to consistent performance without the need for compressed air, a key advantage in terms of reliability. Pneumatic drills rely on air compressors that can introduce variability in performance depending on the available air pressure.
- Maintenance Needs: Electric rock drills typically require less maintenance than their pneumatic counterparts. While pneumatic drills often need regular checks on hoses and fittings, electric drills have simpler mechanics, usually leading to reduced downtime for repairs.
- Environmental Impact: Electric drills generate less noise pollution and air emissions compared to pneumatic drills, making them suitable for urban projects where noise restrictions may apply.
- Cost-Effectiveness: Evidence suggests that while the initial investment for electric drills can be higher, their operational costs are often lower over time, particularly when factoring in energy savings and reduced maintenance requirements.
"The choice between electric and pneumatic drills often hinges on the specific requirements of the project, including environmental considerations and operational costs."
Applications of Electric Rock Drills
Electric rock drills find significant utility across various industries, notably within construction, mining, and geological surveying. Their multifunctionality and adaptability make them indispensable tools, allowing for the execution of tasks with precision and efficiency. The importance of exploring these applications lies in understanding how electric rock drills enhance operational capabilities while contributing to safety and sustainability.
Construction Industry
In the construction sector, electric rock drills are employed for multiple purposes, including foundation work, road construction, and demolition. These drills provide high torque and speed, enabling operators to bore through dense materials such as concrete and reinforced structures. The efficiency of electric rock drills translates to quick project turnarounds, minimizing costly delays.
- Strength and Efficiency: Electric drills can achieve more consistent results than their pneumatic counterparts. As a result, tasks like anchoring and installing rebar happen at a faster rate.
- Reduced Noise Pollution: Operating with less noise is another significant benefit. In urban settings, where noise levels can be a concern, electric rock drills mitigate disturbances.
- Lower Maintenance: Compared to pneumatic versions, electric models generally require less maintenance. Reduced downtime allows construction projects to remain on schedule.
Mining Operations
Mining operations leverage electric rock drills for their capacity to perform in rugged environments. These drills are crucial for tasks such as drilling or blasting for mineral extraction. The utilization of electric rock drills in mining not only improves productivity but also supports safety protocols by minimizing human error.
- Precision in Operations: Electric rock drills allow for accurate drilling, facilitating controlled extraction. This precision reduces waste and maximizes resource recovery.
- Energy Efficiency: Many electric drills are designed to consume less energy while still delivering powerful performance. Enhanced energy efficiency benefits both the environment and the operation's bottom line.
- Safety Enhancements: Incorporating electric rock drills can lead to improved health conditions for operators by minimizing exposure to harmful fumes associated with traditional diesel-powered drills.
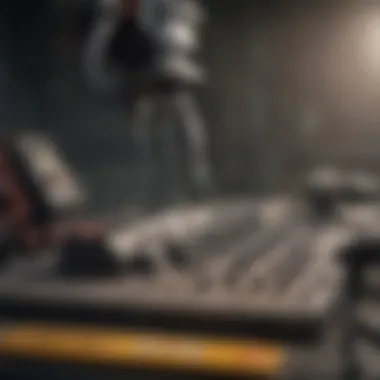
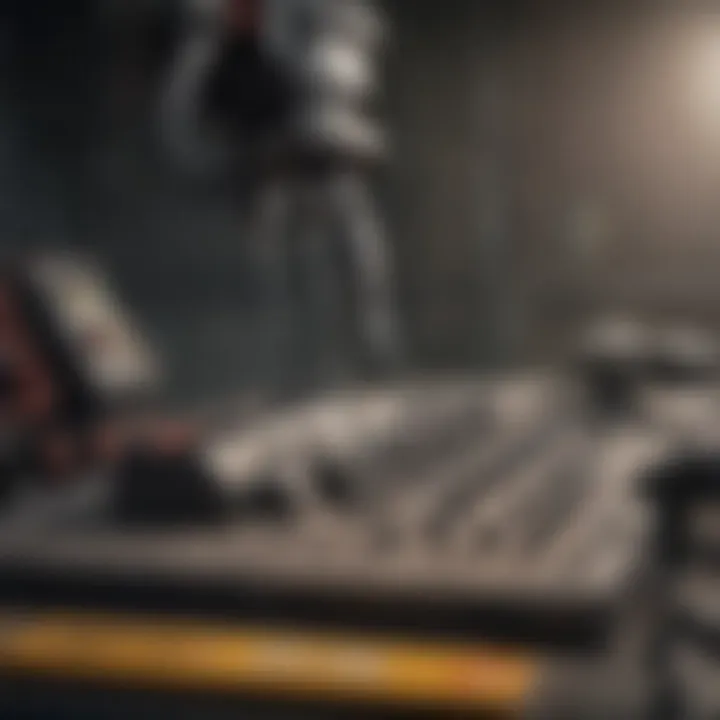
Geological Surveys
Electic rock drills are also vital in geological surveys for their ability to collect samples from beneath the Earth's surface. With the rising need for natural resource management and environmental assessments, these drills enhance the capabilities of geologists.
- Sample Collection: The drills enable operators to extract core samples efficiently, which are essential for analysis in geological studies. Accurate sample collection informs better decision-making regarding resource management.
- Versatility and Mobility: Electric models are often more portable than pneumatic drills. This mobility is advantageous for field surveys requiring flexibility in various terrains.
- Environmental Impact: Electric rock drills significantly reduce the carbon footprint of geological surveys. Using them aligns with contemporary sustainability goals, supporting environmentally conscious practices.
In summary, electric rock drills serve a pivotal role in construction, mining, and geological surveys. Their efficiency, safety, and environmental considerations make them valuable assets in these industries. Understanding their applications is essential for enhancing operational outcomes and ensuring compliance with modern standards.
Safety Considerations
Safety considerations are crucial in the operation of electric rock drills. This section addresses the elements that underlie comprehensive risk management and protective equipment. Ensuring safety protects both workers and equipment, reducing the likelihood of accidents and injuries.
Risk Management Protocols
Risk management protocols involve systematic procedures designed to identify, assess, and mitigate risks. Regularly conducting risk assessments helps to recognize potential hazards associated with using electric rock drills. Important steps include:
- Hazard Identification: This can be done by analyzing the work environment and equipment. It focuses on factors like ground stability and electrical systems.
- Risk Evaluation: Once hazards are identified, evaluating the risks to determine the likelihood and consequences is necessary. This involves grading risks and prioritizing them according to their potential impact.
- Control Measures: It is vital to implement measures that eliminate or minimize risks. Control methods might include training workers, ensuring machinery is well-maintained, and employing safe operating procedures.
A culture of safety needs to be promoted, where workers are encouraged to report unsafe conditions and practices. This engagement fosters a proactive approach to safety in the workplace.
Protective Equipment Requirements
Using the proper protective equipment (PPE) reduces the chance of injury during drilling operations. The specific equipment required may vary based on the work conditions and regulations but commonly includes:
- Helmets: Protect against falling objects and impacts. A hard hat is essential on construction sites.
- Eye Protection: Safety glasses or goggles shield against flying debris and dust.
- Ear Protection: Electric rock drills can generate substantial noise. Earplugs or earmuffs help to prevent hearing loss.
- Gloves: Durable gloves protect hands from cuts, abrasions, and electrical hazards.
- Dust Masks: In environments with high dust levels, masks reduce inhalation of harmful dust particles.
Adhering to PPE requirements not only enhances individual safety but also encourages a collective sense of responsibility towards maintaining a safe working environment.
It is essential to remember that safety is not a one-time effort but an ongoing commitment.
By reinforcing safety protocols and providing proper equipment, professionals can minimize risks and operate electric rock drills effectively. This focus on safety ensures that projects proceed without costly delays and helps protect everyone involved.
Environmental Impact
The impact of electric rock drills on the environment is an essential aspect to evaluate in modern excavation and construction practices. Their adoption highlights a growing concern for sustainability and the ecological footprint of construction activities. Electric rock drills offer an alternative to traditional pneumatic systems, which are often more harmful to the environment due to combustion and associated emissions. By understanding the environmental considerations linked to these tools, stakeholders can make informed decisions that align with global sustainability goals.
Sustainability Considerations
Sustainability in construction is increasingly becoming a priority as industries strive to reduce their carbon emissions and energy consumption. Electric rock drills contribute positively to this effort by utilizing electricity as their primary power source. This shift away from fossil fuels not only enhances energy efficiency but also supports the use of renewable energy sources. If powered by green electricity, the operational carbon footprint of electric rock drills can be minimized significantly.
Moreover, electric models typically have a longer lifespan than their pneumatic counterparts. This longevity reduces the need for frequent replacements and ultimately cuts down on waste. Additionally, because electric rock drills are less noisy, they help decrease the auditory pollution often associated with construction sites, leading to a more positive impact on nearby communities and wildlife.
Noise and Pollution Management
Noise pollution is a critical issue in urban contexts. Electric rock drills provide a viable solution to this problem, as they operate at lower decibel levels than pneumatic drills. This characteristic is especially beneficial in densely populated areas where strict noise regulations are in place. The reduced noise can improve worker safety and enhance comfort levels for surrounding residents.
On the pollution front, electric rock drills emit fewer harmful gases compared to those powered by diesel or gas. Traditional drills can release volatile organic compounds and particulate matter, contributing to air quality degradation. In contrast, electric drills do not produce these emissions directly, significantly lowering the potential for environmental harm.
"Electric rock drills facilitate cleaner operations, fostering a healthier environment for both workers and local communities."
Technological Innovations
Technological innovations are pivotal in driving the efficiency and performance of electric rock drills. These advancements shape how drills operate, increasing their capabilities and shaping their future in diverse applications. Notably, innovations in battery technology and automation lead to significant gains in operational efficiency and environmental sustainability.
Advancements in Battery Technology
The development of battery technology is essential in enhancing the performance of electric rock drills. Modern drills benefit from lithium-ion batteries which provide a higher energy density compared to traditional battery types. These batteries not only extend the operational time but also reduce the overall weight of the equipment. This can be crucial in improving maneuverability in various drilling conditions.
Some advantages of these advancements include:
- Extended Runtime: Longer operational periods between charges improve productivity in the field.
- Rapid Charging: New charging technologies allow batteries to recharge faster, reducing downtime.
- Durability: Advanced designs increase the cycle life of batteries, making them more cost-effective over time.
The technical efforts in optimizing battery performance translate to more robust, efficient drilling operations, making electric rock drills more competitive against pneumatic alternatives.
Automation and Smart Drilling Systems
Automation has introduced a new realm of possibilities for the electric rock drilling industry. Smart drilling systems utilize sensors and artificial intelligence to monitor drilling conditions in real-time. This information enables the adjustment of parameters without human intervention, leading to enhanced precision and safety.
Key features of smart drilling systems may include:
- Real-Time Data Collection: Continuous monitoring of parameters such as pressure and temperature.
- Predictive Maintenance: Using data analytics to forecast when equipment will need servicing, thus minimizing unexpected failures.
- Operator Assistance: Advanced systems can guide operators through complex processes, reducing the risk of human error.
The impact of automation cannot be overstated. It not only improves safety but also enhances overall efficiency in drilling operations. The transition towards these smart systems represents a significant evolution in the realm of electric rock drills, ensuring that they remain vital tools in construction, mining, and other fields.
"Advancements in battery technology and automation are transforming the operational landscape of electric rock drills, ensuring they meet modern demands effectively."
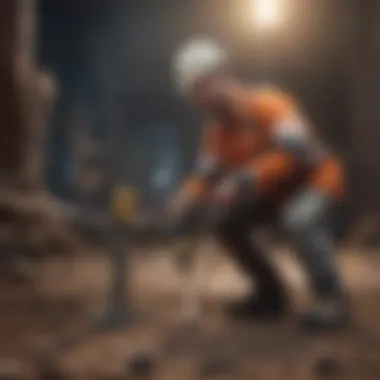
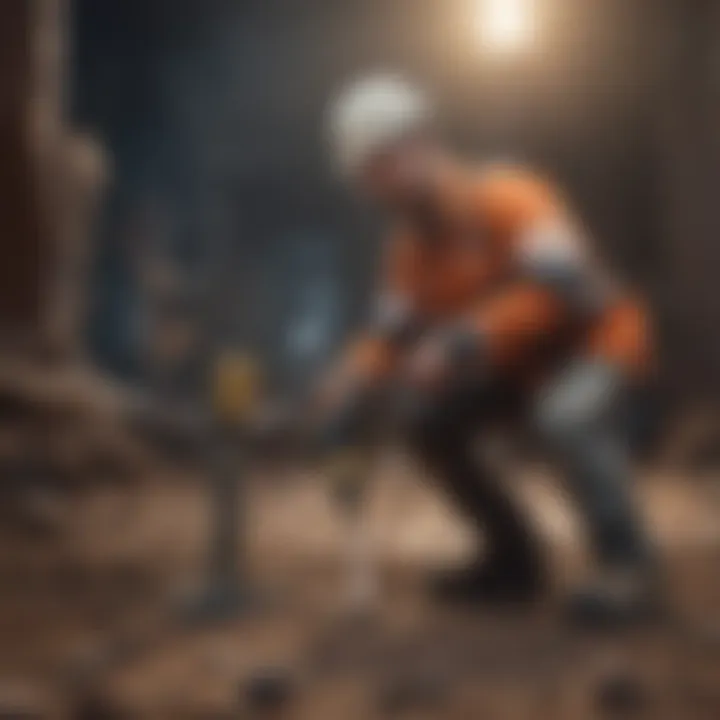
Cost Analysis
Cost analysis is a critical component in the evaluation of electric rock drills. Understanding the financial implications ensures that stakeholders make informed decisions regarding their use in various applications. Cost analysis covers both initial investment and long-term savings, allowing for comprehensive insight into the feasibility of adopting electric rock drills over their lifespan.
Initial Investment vs. Long-term Savings
When considering electric rock drills, the initial investment often raises concerns for businesses and contractors. The upfront costs typically involve the price of the drill itself, which can vary based on specifications and capabilities. Additionally, installation and setup may incur extra expenses.
However, the financial assessment should not end there. Long-term savings become an important counterbalance to these initial costs. Electric rock drills tend to be more energy-efficient than their pneumatic counterparts, translating to lower operational energy expenses over time. Moreover, maintenance requirements for electric models are usually less demanding, leading to reduced upkeep costs. Such savings can be crucial for companies focused on balancing budgets against productivity gains.
To illustrate this, consider the following factors that contribute to long-term savings:
- Energy Consumption: Electric rock drills use less energy compared to traditional drills.
- Maintenance Costs: They have fewer moving parts, which decreases the likelihood of expensive repairs.
- Increased Productivity: Their effectiveness can lead to faster project completion times, minimizing downtime.
Operational Costs Comparison
The operational costs of electric rock drills involve various expenses that accumulate during their usage. A thorough comparison with other drilling technologies, particularly pneumatic drills, reveals distinct advantages of electric models.
- Energy Efficiency: Electric drills typically offer better energy usage. Lower energy requirements can significantly reduce monthly utility bills in both short and long terms.
- Maintenance Expenses: Often linked to the simplicity of electric drill designs, ongoing maintenance costs tend to be lower, affecting the overall budget favorably.
- Downtime and Productivity: With advancements in battery technology and automation, electric rock drills can operate continuously without significant interruptions. This efficiency often results in lower labor costs, as projects progress more swiftly.
In summary, while the initial investment in electric rock drills might seem substantial, it is essential to evaluate long-term savings and operational costs. A detailed cost analysis provides a holistic understanding, enabling stakeholders to align their financial planning with the benefits achieved through electric drilling technology.
Regulatory Standards and Compliance
Regulatory standards and compliance play a crucial role in the development and operation of electric rock drills. These standards are essential for ensuring safety, efficiency, and environmental responsibility in their use. Compliance with these regulations not only helps in protecting operators from potential hazards but also contributes to the sustainability of the operations. Understanding the landscape of these regulations is important for manufacturers, operators, and users alike.
Industry Regulations Overview
The landscape of industry regulations surrounding electric rock drills encompasses a range of guidelines and standards. These regulations address several key areas, including operational safety, worker health, and environmental protection. Important regulatory bodies include the Occupational Safety and Health Administration (OSHA) and the Environmental Protection Agency (EPA). Compliance with their standards can involve rigorous assessments and frequent inspections.
In many regions, the adherence to industry standards is often mandatory. For example, the ISO 9001 standard ensures quality management systems are in place. Furthermore, local regulations may also dictate specific requirements for operation and maintenance practices of electric rock drills. The following points highlight these aspects:
- Safety Protocols: Regulations minimize risks of accidents and injuries during drilling operations.
- Environmental Guidelines: Ensure that drilling activities do not adversely affect the surrounding ecosystem.
- Performance Standards: Help maintain equipment efficiency and reliability through structured maintenance practices.
Compliance Challenges
While regulatory standards are crucial, the path to achieving compliance is often fraught with challenges. Companies may face hurdles such as the following:
- Complexity of Regulations: The multitude of standards can be overwhelming, especially for organizations operating in different jurisdictions. Understanding and implementing varied regulations require significant resources.
- Cost Implications: Achieving compliance often involves substantial financial input towards training, equipment updates, and recurring inspections.
- Evolving Standards: Regulations can change frequently, necessitating continuous education and updates to protocols. Organizations must stay alert to maintain compliance.
"Non-compliance can lead to severe penalties, including fines and operational shutdowns."
Future Trends
The future trends in electric rock drills are crucial for understanding how this technology will evolve in the coming years. As industries demand greater efficiency and sustainability, innovations in drilling technology will address these needs while ensuring safety. Companies face pressures regarding environmental impact, operational costs, and performance. Staying updated on these trends helps professionals make informed decisions.
Emerging Drill Technologies
Emerging technologies in electric rock drills signify a paradigm shift in how drilling is conducted. Modern drill designs are integrating advancements in materials science, resulting in lighter and more durable drill bodies. For instance, carbon fiber composites are increasingly used to reduce weight without compromising strength. Mitigating the strain on operators during prolonged use is a significant consideration here.
Furthermore, the development of high-torque brushless motors enhances power efficiency. These motors offer better performance in challenging conditions compared to traditional options. The integration of automation is another trend, leading to drill rigs that can perform complex tasks visually unattended. These rigs employ machine learning algorithms that adapt drilling parameters in real time based on feedback from various sensors.
"Automation and smart technologies are revolutionizing drilling patterns, making operations not only faster but also more precise."
More companies are exploring modular drilling systems. These systems allow for the interchangeability of components based on specific project needs. This flexibility leads to cost-effective solutions that can adapt to varied geological conditions, enhancing productivity.
Impact of Digitalization on Drilling Techniques
Digitalization has transformed drilling operations significantly. The implementation of Internet of Things (IoT) devices allows for real-time data collection and monitoring. This capability leads to improved decision-making based on accurate drilling performance metrics. Engineers can monitor system health, adjust techniques, and troubleshoot issues remotely, ultimately minimizing downtime.
Moreover, autonomous drilling systems are being developed, reducing reliance on human participation. These systems can analyze geological data, adjust the drilling path as necessary, and operate with minimal intervention. Higher levels of precision and reduced error rates are observable benefits. However, this also raises considerations related to workforce needs and training.
Data analytics play a vital role in optimizing drilling strategies. By utilizing predictive analytics, companies can analyze historical data for better future performance. This insight helps in resource allocation and planning of drilling operations.
Culmination
In this article, the conclusion presents an essential synthesis of the various facets related to electric rock drills. This segment captures the significance of the previous discussions, emphasizing the overall impact that electric rock drills have on the fields of construction, mining, and geological surveys. From a technical point of view, the efficiency and adaptability of electric rock drills have proven them to be vital tools in modern engineering practices.
Summary of Key Findings
The analysis throughout this article underscores several key points regarding electric rock drills:
- Efficiency: Electric rock drills showcase a notable improvement in performance metrics when compared to traditional pneumatic options.
- Environmental Impact: The sustainability aspect of using electric over diesel-driven machinery contributes to reduced emissions, aligning with modern environmental regulations.
- Technological Advancements: Innovations such as enhanced battery technology and automated systems have revolutionized how drilling operations are carried out, leading to increased productivity.
- Safety Protocols: Implementing robust safety measures in the operational procedures of electric rock drills minimizes risks and promotes a safer working environment.
"The integration of electric rock drills within the industry not only optimizes operational costs but also supports the transition towards more environmentally sound practices."
Implications for Future Research
Future exploration in the realm of electric rock drills is paramount. As industries increasingly prioritize automation and efficiency, there is a growing need for comprehensive research in the following areas:
- Enhanced Efficiency Models: Further studies should investigate how electric rock drills can be optimized to reduce energy consumption while maintaining high productivity levels.
- Battery Innovations: Research on alternative energy sources and improved battery technologies could lead to electric drills that are even more efficient and eco-friendly.
- Automation and Smart Systems: The ongoing development of smart drilling technologies offers substantial opportunities to improve operation precision and data acquisition in real-time.
- Long-term Durability and Maintenance: Understanding the lifespan and maintenance needs of electric rock drills can provide critical insight toward achieving sustainable operational costs.
In summary, this conclusion underlines the multifaceted importance of electric rock drills in modern contexts, while highlighting avenues for future exploration and development.