Exploring Drain Pipe Sleeving: Techniques and Benefits
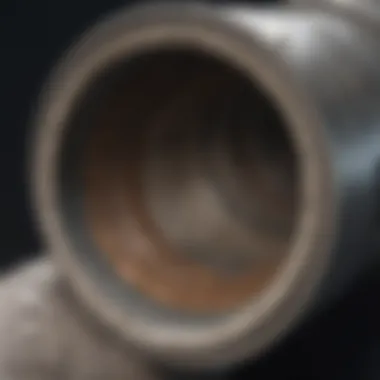
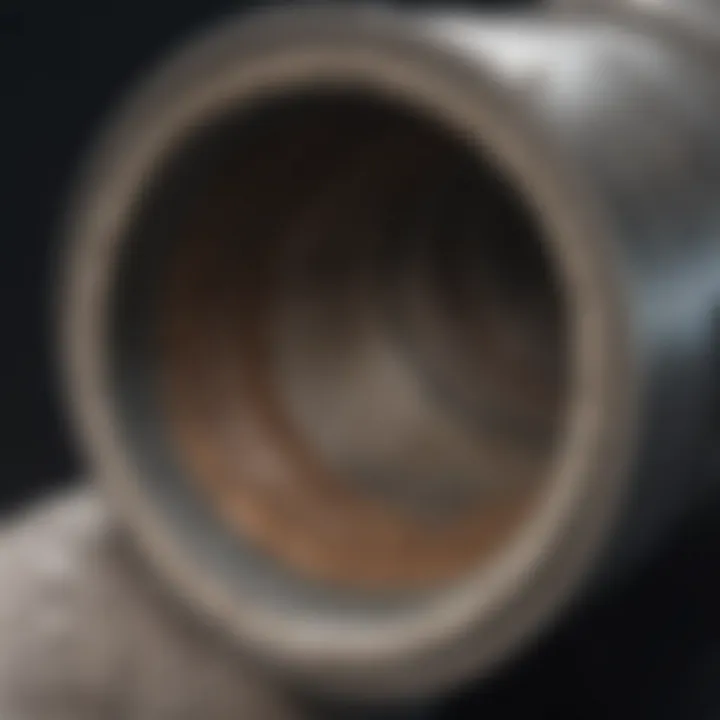
Intro
When it comes to the intricate web of modern infrastructure, drainage systems often lurk in the shadows, uncelebrated yet crucial. These systems are the unsung heroes that whisk away excess water, preventing flooding and ensuring smooth functioning of urban environments. Yet, even these stalwarts of engineering face challenges over time, particularly when subjected to the wear and tear of harsh elements and environmental factors. This is where the practice of sleeving drain pipes comes into play, offering a remedy to enhance functionality and lifespan.
Imagine a drain pipe, once robust, gradually succumbing to corrosion, root intrusion, and just plain age. Sleeving presents an effective workaround—it's akin to giving these pipes a second skin. The idea is straightforward but profound: by encasing existing pipes with protective materials, we can fortify them against future hazards. This article delves into not just the theoretical aspects but also dives into practical techniques, material options, and the manifold benefits of sleeving.
Whether it's a residential undertaking or a commercial project, understanding how to implement this process can save you headaches down the line. Now, let’s explore the broader horizons of sleeving in drainage systems.
Intro to Sleeving Drain Pipes
In the realm of drainage systems, the concept of sleeving drain pipes emerges as an innovative solution to common challenges faced by engineers and property owners alike. As we seek to protect our infrastructure from the effects of wear and tear, sleeving serves not just as a repair method, but as a proactive strategy to enhance the durability and efficiency of piping systems. This article stands as a guide through the intricacies of this practice, shedding light on its myriad benefits and implications.
The importance of sleeving cannot be overstated. For many, drain pipes are hidden beneath layers of concrete and soil, often forgotten until they malfunction. Regular maintenance can only go so far, and eventually, the elements wreak havoc on even the sturdiest materials. Here, sleeving offers a compelling alternative to traditional replacement. Rather than excavating existing infrastructure—a costly and time-consuming endeavor—sleeving allows for revamping and reinforcing existing pipes, thus preserving their functionality and extending their service life.
This process not only provides considerable cost savings but also minimizes disruption to the surrounding environment and communities. Imagine a bustling city where road closures and construction noises are avoided because a simple sleeve was applied to remedy a faulty pipe. Now, that’s a win-win situation. Further, sleeving drains the need for new materials, contributing to a more sustainable approach to resource management. As we explore the various methods, materials, and advantages related to sleeving, we unlock a treasure trove of information that practitioners in the field should not overlook.
"Utilizing sleeving techniques in drainage systems is akin to giving pipes a second chance, ensuring they withstand the test of time."
Understanding the Concept of Sleeving
At its core, sleeving involves inserting a new pipe into an existing one without the need for complete excavation. This practice may conjure images of surgical precision, as the parent pipe is carefully encased in a sleeve that offers additional protection against corrosion, damage, and blockages. The material used for the sleeve is selected based on the specific needs of the drain system and the nature of the underlying issues—whether it's salty water wear or tree root intrusion.
Sleeving acts as a barrier, preventing further deterioration by isolating the original pipe from external threats. It comes in various forms, including flexible materials that can adapt to shifting grounds, making it versatile across many environments. Simply put, sleeving is like giving your plumbing system a sturdy, protective coat to fend off the elements.
Historical Context of Sleeving in Drainage Systems
The practice of sleeving has its roots in ancient engineering techniques, where civilizations relied on durable materials to manage wastewater and storm drainage. However, modern sleeving as we know it began to gain traction in the mid-20th century as technology advanced. Initially, the focus was on simply repairing leaks. Over time, it evolved into a foresighted approach aimed at preventing issues before they arise.
In many urban areas, where old clay drainage systems blend with newer materials, sleeving represents a method of marrying the two technologies without significant overhauls. By integrating sleeving into the maintenance playbook, municipalities have managed to keep infrastructure up to standards while dealing with budget constraints. It's remarkable how a method with such a rich history continues to form the foundation of current and future drainage innovations.
Rationale for Sleeving Drain Pipes
In any drainage system, factors such as material degradation, environmental conditions, and usage play a significant role in a pipe’s longevity and reliability. Thus, understanding the rationale for sleeving drain pipes is essential for making informed decisions about maintenance and upgrades. The benefits of sleeving extend beyond mere patching - they fundamentally enhance the structural integrity, fluid dynamics, and lifespan of existing piping.
Preventing Structural Damage
Structural damage in drainage systems can lead to significant challenges. When pipes corrode or crack, they not only risk collapse but also can cause serious flooding and water damage to surrounding areas. The process of sleeving helps mitigate these risks by providing an additional layer of protection against external forces.
- Reinforcement: Sleeves act as a support system, bearing loads that would otherwise put stress on the original pipe. This is especially crucial in urban environments where soil movement can be more prevalent.
- Corrosion Resistance: Materials like polyethylene and steel sleeves resist chemical reactions that lead to deterioration, significantly prolonging the life of drainage systems.
- Sealing Gaps: By snugly fitting over existing pipes, sleeves also minimize the chances of water escaping, thus preventing soil erosion and subsidence around the pipe.
In essence, sleeving is like giving an old pipe a sturdy new jacket, providing it with strength and resilience needed to stand the test of time.
Enhancing Fluid Flow Efficiency
Drainage systems thrive on efficiency. Any obstacles or blockages in fluid flow can lead to a host of issues, from slow drains to unpleasant odors from stagnant water. Sleeving enhances this flow in several key ways:
- Smooth Interior Surface: Sleeves can create a smoother surface compared to old, rough pipes, allowing water to travel faster and reducing friction. Imagine a river flowing smoothly over a flat stone as opposed to over a rocky surface.
- Reduced Blockage Potential: With fewer crevices where debris can collect, the risk of blockages decreases. This ensures consistent fluid movement.
- Optimized Pipe Diameter: Sometimes, new sleeeves can slightly adjust the diameter for improved water flow without needing a complete overhaul of the existing infrastructure.
The result? A more efficient system that promotes effective drainage during heavy rainfall or snowmelt, preventing potential backups.
Prolonging Service Life of Existing Pipes
Lastly, one of the most compelling reasons for sleeving drainage pipes is the extension of service life. Regular replacement of pipes can be both costly and disruptive. By opting for sleeving, property owners can achieve:
- Cost savings: There’s a less severe financial impact compared to replacing entire systems. Property managers and homeowners alike can save substantial amounts in both materials and labor.
- Less Downtime: Sleeving involves less digging and disruption, leading to quicker repairs and minimal inconvenience. For example, a sleeving project might only take days instead of weeks compared to complete replacements.
- Eco-Friendliness: Reusing existing infrastructure minimizes material waste and utilizes fewer resources, aligning with sustainable practices.
Common Materials for Sleeving
When discussing the practice of sleeving drain pipes, it's crucial to dive into the varieties of materials that come into play. Each type of material brings with it unique properties, benefits, and considerations that ultimately affect the overall performance and durability of drainage systems. In essence, selecting the right material for sleeving is not just about comfort but also about efficacy in the long run. Let's explore some of the most common materials used in this application.
Polyethylene as a Versatile Option
Polyethylene is indeed one of the most widely used materials for sleeving. It's lightweight yet robust, making it a popular choice for installers. Its chemical resistance is a significant plus, allowing it to stand firm against a range of corrosive agents present in wastewater. This material can be easily crafted to match desired specifications, whether it’s thinner walls for smaller pipes or thicker ones for more demanding environments.
The flexibility of polyethylene also lends it an edge in various applications, especially when it comes to urban drainage systems. Its ease of installation is often a time-saver, reducing labor costs significantly. Moreover, its smooth inner surface helps promote efficient fluid flow, thereby minimizing blockages that might typically plague other materials.
This versatility, combined with a strong resistance to environmental factors, rightfully marks polyethylene as a go-to option in the realm of sleeving.
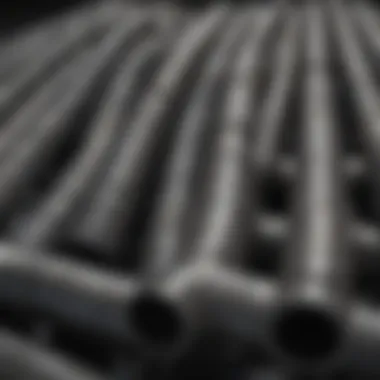
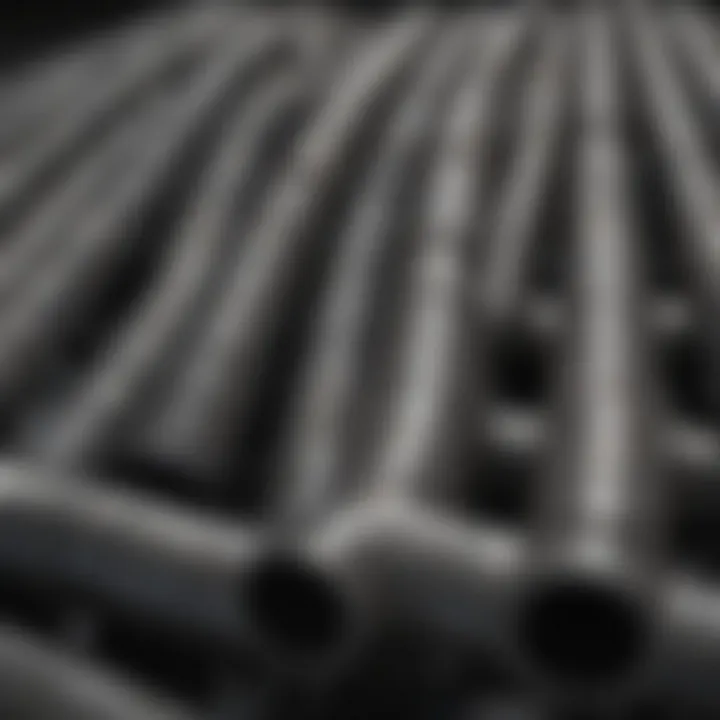
Steel Sleeves for Added Strength
Though polyethylene has its merits, steel isn't too far behind in the conversation—especially when ruggedness is paramount. Steel sleeves offer enhanced structural integrity making them an ideal choice in scenarios where external pressures are significant. Applying steel sleeves in older, corroded pipes can add a necessary layer of strength that is often needed to prolong service life.
It's worth noting, however, that steel comes with its own set of considerations. For instance, while it provides excellent support, it’s susceptible to corrosion, necessitating protective coatings or galvanization to prolong its lifespan. In many industrial applications, where high pressures and difficult environments are the norm, steel's tensile strength becomes a valuable asset that often outweighs the challenges it presents, making it a favored choice in low-flow situations.
Concrete and Its Applications
Concrete may not jump immediately to mind when talking about sleeving materials, but it definitely deserves a shout-out. This material stands out because of its inherent durability and resistance to harsh environmental conditions. Concrete sleeves can support heavier loads and are particularly useful in larger drainage systems or municipal projects where weight and volume are concerns.
In applications like stormwater drainage, the longevity of concrete makes it a prudent choice. However, it’s essential to manage water infiltration meticulously to avoid potential structural damage due to hydrostatic pressure.
Moreover, concrete is often viewed through the lens of sustainability in drainage practices. It's a reusable material that, when combined with modern techniques, can help lower the carbon footprint associated with drainage construction.
Innovative Composite Materials
Innovation leads the way in many industries, drainage included. Today, various composite materials are gaining ground as alternatives for traditional sleeving methods. These composites, often designed to take advantage of the best attributes of different materials, marry the lightweight nature of polymer with the robustness of metals.
One notable composite application is the use of fiberglass-reinforced plastic (FRP). These materials boast high resistance to corrosion, making them ideal for long-term use in harsh conditions. Moreover, their flexibility during installation enhances adaptability to existing structures, providing seamless integration with minimal disruption.
The adaptability and efficiency these composite materials offer make them worth considering for modern projects. They’re showing up particularly in systems demanding higher resiliency without the added weight that steel or concrete brings.
In short, the choice of material for sleeving drain pipes depends on various factors including environmental conditions, load requirements, and installation ease. Understanding the properties of each material can lead to informed decisions that enhance the longevity and efficiency of drainage systems.
By delving into these common materials for sleeving, one begins to see that each has specific roles to play within different contexts. With proper consideration, the choice of materials contributes significantly to the overall effectiveness of drainage systems, ultimately setting the stage for success.
Techniques for Sleeving Drain Pipes
The effectiveness of sleeving drain pipes hinges on the techniques employed during the process. Understanding these techniques is crucial for ensuring that the sleeved pipes perform optimally over time. Different methods come with their own sets of advantages, challenges, and applications, making the selection of the right technique pivotal. By focusing on the methods outlined below, one can not only enhance the durability of drainage systems but also optimize costs and time required for maintenance.
In-situ Sleeving Methods
In-situ sleeving methods involve repairing existing pipes without removing them entirely from their location. This technique grants several benefits, especially for urban environments where digging and disruption could cause significant inconveniences. A common method includes using a liner, typically made of fiberglass or resin-saturated material, which is inserted into the deteriorating pipe and inflated. Once cured, this forms a new, robust pipe within the old one.
The importance of this approach lies in its ability to minimize service interruption and reduce labor costs. After all, why uproot a whole system when you can pilot a solution right within the existing structure? This method can often be completed within a few hours, allowing the drainage to function almost immediately.
Pre-manufactured Sleeving Solutions
Pre-manufactured solutions provide a different angle, as they entail using sleeves crafted beforehand to fit specific sizes and shapes of pipes. These sleeves are typically made from durable materials such as polyethylene or steel, designed to be slid over the existing pipe. The primary benefit here is the fast installation process; these sleeves can be quickly deployed in a fraction of the time required for other methods.
However, careful consideration of the dimensions is needed. Not every sleeve will fit perfectly onto an existing pipe, which might necessitate some additional adjustments. Ensuring a good fit can help avoid complications down the line, making pre-manufactured solutions an efficient but often less flexible option compared to in-situ methods.
Trenchless Technology Applications
In the realm of advanced techniques, trenchless technology stands out as a game-changer for sleeving applications. This innovative approach allows professionals to replace or repair pipes without extensive excavation. Techniques like horizontal directional drilling enable new sleeves to be placed underground without disturbing the surface above.
The advantages of trenchless technology are multifold. Trenching can lead to significant disturbances and longer project timelines. In contrast, trenchless methods drastically cut down on these issues. Not only does it mitigate the mess, but the efficiency in time and labor makes it a desirable choice for many projects, especially in densely populated areas.
"By adopting trenchless methods, companies can minimize workflow interruptions and restore functionality faster, making it a prime choice in modern drainage practices."
In summary, the chosen technique for sleeving drain pipes significantly impacts the efficiency and effectiveness of the repair or replacement process. Both in-situ and pre-manufactured methods present unique advantages, while trenchless technology marks a forward-thinking approach to pipe care. Each technique has its considerations, making informed selection integral to successful outcomes.
Advantages of Sleeving Drain Pipes
Understanding the advantages of sleeving drain pipes is crucial in assessing the best practices for maintaining infrastructure. Sleeving can significantly enhance system performance while addressing various environmental and economic concerns. This section provides an in-depth exploration of the advantages associated with the sleeving method.
Cost-Effectiveness of Sleeving Compared to Replacement
When faced with deteriorating drain pipes, the instinct to replace them often seems like the only solution. However, sleeving provides a more cost-efficient alternative. The initial expense of replacing pipes can include not just the material but also extensive labor and potential disruption to the surrounding environment. Sleeving minimizes both labor costs and materials.
- Lower Labor Intensity: Sleeving is significantly less labor-intensive than complete replacements. The process often requires fewer workers and reduced time on-site, which translates to savings.
- Material Savings: Using sleeves means that only a fraction of the original pipe needs to be replaced or repaired. By delivering a new layer within the existing structure, the cost of sourcing new materials is dramatically lowered.
- Extended Life: Through sleeving, the lifespan of the original pipe can be effectively extended, thus delaying the need for any costly interventions in the future.
"Investing in sleeving today saves you from a world of expenses tomorrow."
Reduced Environmental Impact
In today’s world, environmental considerations weigh heavily on decision-making in construction and maintenance. Sleeving drains is not only kind to your budget; it is also a gentle approach to Mother Earth.
- Less Disruption: Unlike traditional pipe replacement that often uproots landscaping and alters drainage pathways, sleeving requires minimal excavation. This ensures that surrounding ecosystems remain undisturbed.
- Waste Reduction: When replacing pipes, waste is an unavoidable byproduct. Sleeving utilizes existing materials effectively, drastically reducing waste material sent to landfills.
- Sustainable Practices: Many sleeving materials are recyclable, promoting a circular economy that aligns with modern environmental policies and regulations. Choosing to sleeve reinforces a commitment to sustainability in both urban and rural settings.
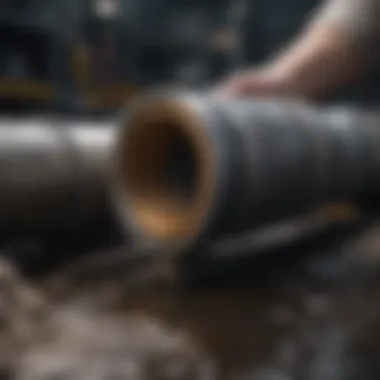
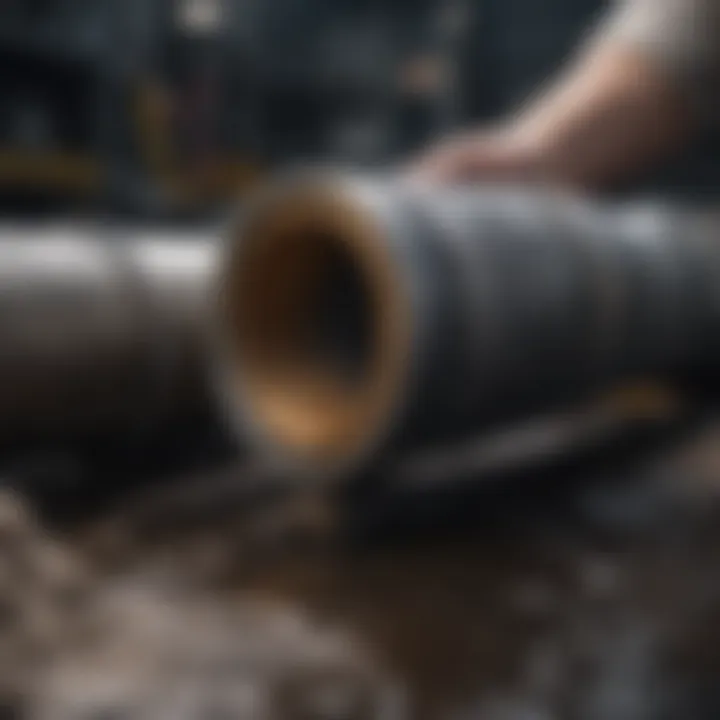
Versatile Applications in Various Settings
The versatility of sleeving drain pipes emerges as one of its predominant benefits. It suits various settings including residential, commercial, and industrial applications, thus offering broad usability.
- Residential Use: Homeowners may find sleeving beneficial in dealing with aging drainage systems without the need for intrusive replacements. It allows for quick repairs that maintain property aesthetics.
- Commercial Projects: Large businesses, especially those in urban areas, benefit from sleeving by minimizing downtime. The less disruptive nature of sleeving means that operations can continue while repairs occur.
- Agricultural Settings: Farms often rely on functioning drain systems to prevent flooding or soil erosion; sleeving can be a quick fix in these situations, enhancing productivity without extensive construction work.
In summary, the advantages of sleeving drain pipes offer a compelling narrative for maintaining and enhancing drainage systems. The economic benefits, environmental consciousness, and versatile applications highlight the importance of considering this method for anyone involved in infrastructure management or maintenance.
Challenges and Considerations in Sleeving
Identifying the hurdles and essential considerations in sleeving drain pipes is crucial for ensuring successful outcomes in various residential and commercial projects. While sleeving offers many advantages, neglecting these challenges could lead to significant issues down the road. Ensuring an effective sleeving process requires careful assessment of the existing conditions, material compatibility, and adherence to regulatory protocols. Each of these factors plays a significant role in the ultimate success of the sleeving initiative.
Assessing Existing Condition of Drain Pipes
Before any sleeving work begins, it is vital to assess the existing condition of the drain pipes involved. This inspection helps to determine the degree of deterioration and identifies any structural weaknesses that could influence the sleeving process. Key aspects to evaluate include:
- Cracks and Corrosion: Detecting any cracks or signs of corrosion early can prevent more extensive damage later.
- Blockages: Clogged pipes can lead to pressure buildup, complicating the sleeving process and impacting fluid flow.
- Material Integrity: Understanding the current material can provide insights into the best sleeving material or technique to use.
A thorough inspection prepares the groundwork for a tailored approach to the sleeving project, addressing specific issues rather than adopting a one-size-fits-all strategy.
Compatibility of Materials
Material compatibility is another critical factor in the sleeving process. The selected sleeve must not only fit the existing pipe but also be compatible with it in terms of thermal expansion, chemical resistance, and overall durability. Here are some considerations:
- Thermal Properties: Different materials expand or contract in response to temperature changes. Mismatched materials can lead to stress and failures.
- Chemical Resistance: Depending on the drainage system’s application, exposure to various chemicals must be considered to avoid degradation of the sleeve.
- Mechanical Properties: The sleeve should provide sufficient support to accommodate the existing pipe's ability to withstand external loads.
Choosing the right materials can ensure long-lasting performance and reduce maintenance needs in the future.
Regulatory Compliance and Standards
Finally, adhering to regulatory compliance and established standards is essential in any engineering or construction project. Each region might have its own codes and regulations that govern drainage systems, which can include:
- Building Codes: Local and national building codes dictate acceptable materials and techniques for sleeving to ensure public safety.
- Environmental Regulations: Understanding the impact of sleeving on surrounding ecosystems is vital. Certain materials may require environmental assessments before usage.
- Quality Control Standards: Implementing relevant quality control measures helps ensure the integrity and durability of the work performed.
Ignoring these regulations can lead to project delays or legal complications, undermining the project's efficiency and integrity.
"Thoroughly preparing and considering these challenges can make the difference between a successful installation and ongoing problems that might haunt future operations."
Maintenance of Sleeved Drain Pipes
Maintaining sleeved drain pipes is a linchpin in ensuring the longevity and efficiency of drainage systems. Regular upkeep is not merely a recommendation; it's an essential commitment to protect your investment and to enhance the performance of the pipes. When drainage systems are allowed to fall into disrepair, the consequences can be both costly and troublesome, resulting in significant water damage and expensive repair costs. Thus, integrating a proactive maintenance approach is key.
Routine Inspection Practices
Routine inspections are like regular check-ups at a doctor’s office; they help catch potential issues before they balloon into costly disasters. These inspections should be scheduled periodically, typically bi-annually or after significant weather events. Key points to consider during inspections include:
- Visual Checks: Look for any signs of wear or deterioration on the sleeves. Cracks, leaks, or shifting can indicate problems that need addressing.
- Flow Assessment: Observing the flow of water can help assess whether blockages or constrictions exist. Any irregular flow patterns can be a red flag.
- Environmental Factors: Be mindful of surrounding vegetation and soil conditions. Roots or erosion can impact the integrity of the pipes.
A point to consider here is the accessibility of the sleeves. If they are buried deep underground or behind walls, it may be less straightforward. Utilizing tools like cameras can help in these tricky situations.
Dealing with Potential Blockages
Blockages can feel like a ticking time bomb in any drainage system. These issues can quickly escalate, leading to backups that can damage both the sleeving and the existing pipes. To effectively manage potential blockages, consider the following strategies:
- Routine Flushing: Regularly flushing the pipes can help clear out debris. This doesn’t take much time and can prevent bigger issues down the line.
- Root Control Measures: If tree roots are infiltrating the system, mechanical or chemical treatments can be taken. However, be cautious with chemical solutions, as they can leach into surrounding soil.
- Probe and Inspect: For significant blockages, using a specialized probe can help identify the nature and location of the obstruction.
As highlighted, proactive measures can significantly reduce the risks associated with blockages.
Longevity and Upkeep Strategies
Fostering the longevity of sleeved drain pipes requires commitment and foresight. Here are some strategies to keep them in tip-top shape:
- Scheduled Maintenance: Set up a maintenance schedule that includes inspections, clean-outs, and repairs. This will ensure minor issues don’t evolve into major concerns.
- Investing in Quality Materials: Use high-quality sleeve materials that can withstand environmental stress. As they say, “buy cheap, buy twice.”
- Educate Users: If the drainage system is in a communal or shared area, educating all stakeholders about proper usage and maintenance can prevent misuse.
Staying ahead of potential issues is vital for achieving maximum performance from sleeved drain pipes.
"Preventive maintenance is the key to a long-lasting system, as it keeps hidden problems at bay and ensures optimal performance."
Taking the time and effort to invest in the maintenance of sleeved drain pipes can yield substantial returns in terms of efficiency, longevity, and overall drainage health.
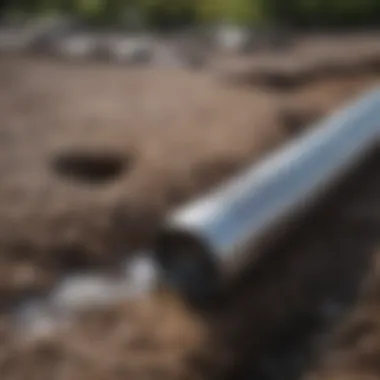
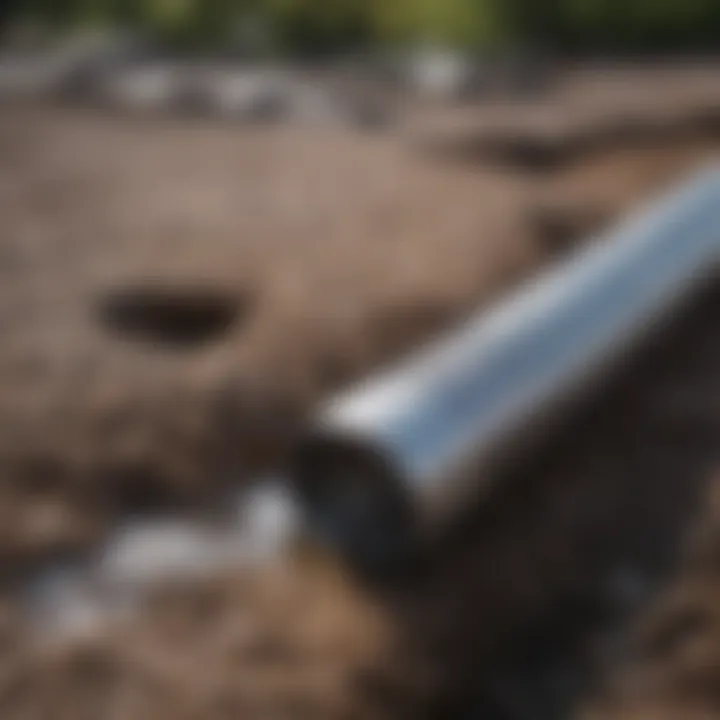
Environmental Impact of Sleeving Practices
The environmental implications of sleeving practices are crucial to understanding the overall benefits this method brings to drainage systems. In today’s world, where sustainability reigns supreme, effective waste management and resource conservation have become guiding principles for many industries. Sleeving drain pipes not only addresses structural and functional issues but also plays an integral role in minimizing ecological footprints. Let’s dive deeper into how sleeving contributes positively to our environment.
Reduction of Waste
One prominent advantage of sleeving is its ability to significantly reduce waste. Traditionally, when drain pipes fail or become damaged, the common reaction is to replace them entirely. This approach not only generates large amounts of debris but also consumes new resources to manufacture replacement pipes. However, sleeving emerges as an alternative that mitigates this problem. By encasing existing pipes in protective sleeves, the need for complete removal is eliminated.
This practice drastically reduces the amount of industrial waste produced. The materials that would normally end up in landfills—such as old pipes—are preserved by layering new materials over them. Consequently, sleeving helps alleviate the pressure on waste disposal sites, contributing to an overall cleaner environment. Furthermore, fewer materials sourced for new pipes means lower production costs and reduced energy consumption associated with manufacturing.
"Turning old into new: sleeving not just repairs but redefines drainage efficiency while treading lightly on our planet."
Resource Conservation Through Repair
In the sphere of sustainability, conservation is paramount. Sleeving drain pipes not only extends the life of existing infrastructure but also ensures that valuable resources are used more judiciously. With new technologies and advanced materials being utilized, a well-implemented sleeving solution can effectively restore the original function of a draining system without the need for new materials.
Through sleeving, repairs are made possible without disturbing the landscape and (in many cases) without interrupting the flow of water. This directly translates to less resource depletion—both raw materials and energy used in the repair process. Some of the innovative materials being used today, like high-density polyethylene or steel, offer durability and longevity. The durability of these materials means they are only replaced infrequently, unlike cheaper alternatives that wear down quickly.
In rural areas, where budget constraints might limit access to new materials, sleeving becomes even more significant. Farmers and local communities can maintain their drainage systems without incurring heavy expenses and while conserving both monetary and environmental resources.
In summary, the environmental impacts of sleeving practices can hardly be overstated. Reducing waste and conserving resources through repair are integral to maintaining a sustainable future. The method is not just about enhancing the performance of drainage systems; it symbolizes a shift towards responsible environmental stewardship.
Case Studies: Successful Sleeving Applications
The inclusion of real-life case studies in the discussion of sleeving drain pipes underscores the practicality of this method in varying contexts. These case studies illuminate not only the process itself but also the tangible benefits that come from adopting sleeving techniques. They provide insight into how different materials and methods work in both urban infrastructure and rural applications, revealing challenges overcome and advantages gained.
Urban Infrastructure Projects
In urban environments, where drainage systems are crucial for managing stormwater and preventing flooding, sleeving has gained considerable traction. A notable example can be found in Chicago’s ongoing rehabilitation project. The city faced significant issues with its aging drain pipes, many of which were crumbling and causing backups during heavy rain. Instead of opting for complete replacement, which would be both cost and time prohibitive, officials decided to sleeve the existing pipes with high-density polyethylene.
This decision yielded a few remarkable advantages:
- Cost Efficiency: By using sleeves, the city saved an estimated 40% on materials and labor compared to full pipe replacement.
- Reduced Disruption: Minimizing excavation allowed local businesses to operate with fewer interruptions and kept traffic flowing, which is critical in bustling urban areas.
- Longevity and Performance: The sleeving process improved flow capacity and added years to the lifespan of the existing infrastructure, which brought further confidence to the ongoing efforts.
The case exemplifies how urban centers can creatively address systemic shortcomings while safeguarding community interests.
Rural and Agricultural Uses
In more rural settings, the application of sleeving has also proven beneficial, particularly for agricultural drainage systems. Take the instance of a farming community in central California that faced recurring issues with blockages in their drainage network, affecting irrigation and leading to crop losses. Instead of digging up their entire irrigation system, they opted for composite sleeving.
This has shown impressive results due to:
- Sustainability: By preserving the existing pipes, farmers not only conserved resources but also adhered to local regulations aimed at minimizing environmental impact.
- Enhanced Functionality: The new sleeves also featured specialized drainage characteristics, which improved water flow during key growth periods.
- Community Collaboration: Local farmers banded together to share costs and techniques, fostering a community spirit as they tackled drainage challenges jointly.
These case studies reveal a broader understanding of the functionality and cost-effectiveness of sleeving in both urban and rural settings, emphasizing its growing significance in modern drainage solutions.
By looking at these practical examples, we can appreciate not just the theoretical benefits of sleeving drain pipes but also its application in real-world scenarios, drawing lessons and inspiration for future projects.
Future of Sleeving Drain Systems
The future of sleeving drain systems is an essential consideration for anyone involved in drainage infrastructure—be it engineers, researchers, or policymakers. As urbanization continues to rise and environmental concerns heighten, sleeving presents a proactive approach that paves the way for enhanced drainage management. The importance of this topic lies not just in maintaining existing systems, but also in shaping the development of more resilient infrastructures that can withstand the test of time.
Sleeving plays a critical role in both expanding and reinforcing current systems. The benefits range from reduced costs associated with traditional pipe replacement to improved performance through innovative technologies. Moreover, sleeving can provide long-term solutions to the pressing challenge of managing aging pipeline networks, which are common in many urban areas. With an ever-growing demand for sustainable practices in construction and maintenance, sleeving becomes not just a necessity, but a wise investment.
Emerging Technologies in Sleeving
Emerging technologies continue to transform the way we approach sleeving drain pipes. One of the noteworthy advancements includes the development of smart sleeves equipped with sensors. These sensors can monitor the structural integrity of the pipe in real-time, detecting issues like corrosion or warping before they escalate into major failures. This proactive identification of potential problems can save significant time and resources in maintenance and repairs.
Furthermore, advancements in materials science have led to the creation of lighter, more durable composite materials which enhance both the flexibility and strength of sleeves. These newer composites are not only resistant to environmental degradation but also improve overall fluid flow efficiency within the system.
Examples of these technologies include:
- Polymeric sleeves that adapt to varying temperatures, reducing stress and fatigue risks.
- Nanotechnology that is employed to develop coatings resistant to biofouling, thus maintaining flow rates.
- Augmented reality tools used in planning and conducting installation, allowing for precise alignment and fitting of sleeves.
Trends Influencing Drainage Practices
Numerous trends are influencing the future of drainage practices. One significant factor is the growing awareness of sustainability in construction. Green building practices now prioritize methods that minimize environmental impact. Sleeving aligns perfectly with this goal, as it conserves resources by utilizing less material and reducing the need for intensive excavation work.
Additionally, regulatory shifts are imposing stricter requirements for drainage systems. These regulations often favor solutions that are adaptable and resilient. The sleeving technique not only meets these needs but also offers a pathway to comply with evolving standards.
Lastly, public investment in infrastructure is increasingly focused on long-term performance rather than short-term fixes. This trend is leading to a robust interest in sleeving methods, recognizing them as viable solutions to meet growing infrastructure demands.
"The evolution in sleeving techniques, driven by technology and sustainability, is a testament to the way engineering adapts to new challenges and opportunities."
In summary, the future of sleeving drain systems appears promising, filled with innovative technologies and influenced by significant trends. An understanding of these changes holds the key to enhancing efficiency and sustainability in drainage management, making it imperative for stakeholders to remain informed and adaptable.