In-Depth Analysis of Lithium Battery Manufacturing Processes
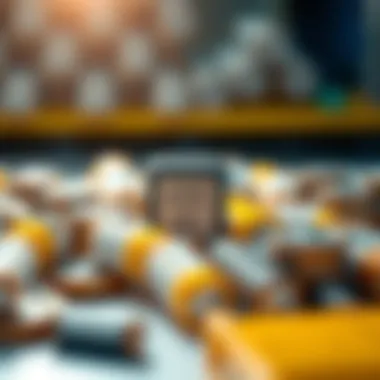
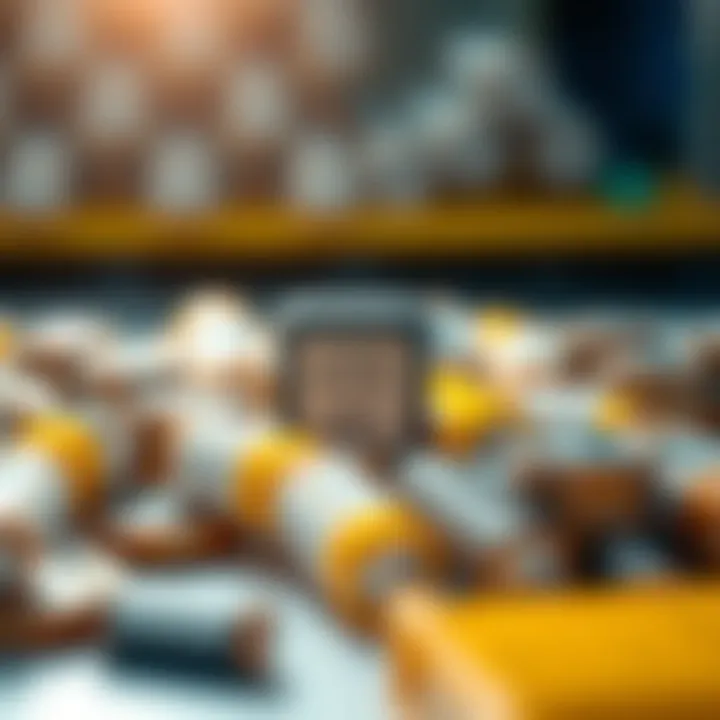
Research Overview
Lithium batteries have become an integral part of modern technology, particularly in the realm of portable electronics and electric vehicles. Understanding the nuances in their manufacturing can pave the way for advanced applications and innovations. Not only does this research provide insights into the underlying processes, but it also sheds light on the significant challenges the industry faces, such as sourcing materials sustainably and enhancing production efficiency.
Summary of Key Findings
Through an in-depth analysis, several key findings emerge:
- Material Significance: The essential materials in lithium battery production include lithium, cobalt, and nickel, each contributing unique properties that affect battery performance and longevity.
- Technological Innovations: Advanced techniques, like dry electrode coating and solid-state battery technology, are being explored to improve energy density and safety.
- Environmental Impact: Concerns regarding the environmental footprint of lithium sourcing and battery disposal are becoming increasingly prominent. Methods to minimize waste and improve recycling processes are vital.
Significance of Research
This research is particularly relevant today. As the demand for batteries surges, especially with the rise of electric vehicles, understanding the manufacturing process is crucial for academics, researchers, and industry professionals. Findings not only illuminate current practices but also highlight future challenges and opportunities in the lithium battery sector. Additionally, it offers a foundation for developing strategies that address environmental and ethical considerations in the industry.
Methodology
In order to effectively examine the complexities of lithium battery manufacturing, a thorough methodology was implemented.
Research Design
The research is grounded in a mixed-methods approach, combining qualitative interviews with industry experts and quantitative analysis of production data. This dual approach ensures a holistic understanding of both the technical and operational facets of battery manufacturing.
Data Collection Methods
The following methods were used to gather information:
- Interviews: Engaged with experts across the lithium battery supply chain, from material suppliers to manufacturers.
- Surveys: Conducted surveys to gather insight on production techniques and challenges faced by manufacturers.
- Literature Review: Analyzed existing research and publications to contextualize findings within the broader industry landscape.
"A thorough understanding of lithium battery manufacturing processes not only aids in enhancing efficiency but also opens the door to innovative solutions for current environmental challenges."
This comprehensive examination of lithium battery manufacturing delves into key processes, challenges, and future innovations that shape this critical field.
Foreword to Lithium Batteries
Lithium batteries have become the cornerstone of contemporary energy storage solutions. Their significance can't be overstated, as they power everything from smartphones to electric vehicles, marking a transformative phase in technology. The journey of understanding these batteries begins with unraveling their core components and appreciating the role they play in our daily lives.
Historical Context
The history of lithium batteries stretches back to the 20th century, with the first commercial lithium battery developed in the late 1970s. Before that, the landscape of batteries was dominated by lead-acid and nickel-cadmium options. A turning point came when researchers, John Goodenough and colleagues, invented the lithium-cobalt oxide cathode, setting the stage for a new generation of energy storage systems.
These developments did not happen in a vacuum. The increasing demand for portable electronics, combined with the growing concern over energy efficiency, propelled the lithium battery into the spotlight. Companies such as Sony led the charge in commercializing these batteries, introducing them into consumer electronics like camcorders and later laptops. This historical perspective showcases how innovation has paved the way for today's sophisticated battery designs, continually pushing the limits of what is possible.
Importance in Modern Technology
Fast-forward to today, and lithium batteries are not just a luxury — they are integral to global infrastructure. As we move towards a greener economy, the importance of lithium batteries becomes even more pronounced. Their higher energy density and longer cycle life compared to traditional battery types make them ideal for electric vehicles and renewable energy storage.
In addition to electric vehicles, they play a pivotal role in various sectors:
- Renewable Energy: Lithium batteries are key for storing solar and wind energy, helping manage the intermittent nature of these sources.
- Consumer Electronics: From smartwatches to tablets, lithium batteries provide the necessary power to keep our devices running efficiently.
- Medical Devices: Many modern medical devices rely on lithium batteries for portability and reliability, such as in pacemakers and portable diagnostic equipment.
"The shift toward lithium-ion technology has revolutionized how we approach energy storage, ushering in a new age of efficiency and accessibility."
Key Components of Lithium Batteries
Understanding the key components of lithium batteries is crucial for grasping how they function and their role in various applications. Each part contributes significantly to the overall efficiency, capacity, and safety of batteries used in everything from electric vehicles to consumer electronics. This section aims to provide detailed insight into the essential elements that make lithium batteries tick and the importance of these components in today’s battery technology landscape.
Lithium and Its Properties
Lithium, the lightest metal, plays a pivotal role in the effectiveness of lithium batteries. Its unique properties make it an ideal choice for energy storage. Being highly electropositive allows lithium to easily lose electrons, providing high energy density, which translates into longer battery life per charge. Moreover, lithium is favorable because it has a low atomic mass, making it incredibly efficient in terms of weight.
What’s more, lithium ions can move swiftly through the electrolyte during charge and discharge cycles, leading to rapid power delivery. This property is vital for applications demanding immediate energy, like electric cars that accelerate swiftly. However, the reactivity of lithium can be a double-edged sword, necessitating careful management within battery chemistry to prevent potential hazards.
Some key characteristics of lithium include:
- High electrochemical potential: Essential for voltage generation.
- Low density: Keeps overall battery weight down.
- Thermal stability: Important for safety in high-stress environments.
Electrolytes and Their Functions
Electrolytes are the unsung heroes of lithium batteries, serving as the medium through which lithium ions travel between the anode and cathode. Their role is critical; without a proper electrolyte, energy absorption and discharge would be nearly impossible. They typically exist in liquid or solid state and must possess high ionic conductivity while being stable under various operating conditions.
The most common electrolyte in lithium batteries is lithium salt dissolved in an organic solvent. However, with advancements, solid-state electrolytes are beginning to gain traction due to their potential to enhance safety and energy density.
One notable property of electrolytes is their ability to dissolve lithium salts without facilitating conductive pathways for undesirable side reactions, ensuring battery efficiency and longevity. A few essential functions include:
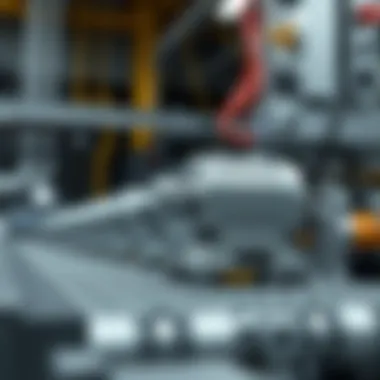
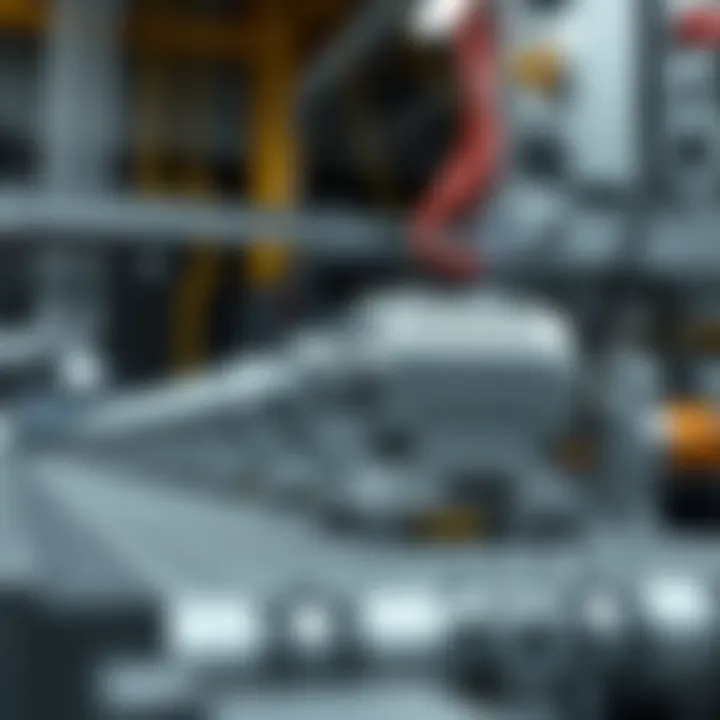
- Conducting ions: Enabling movement necessary for charge and discharge.
- Prohibiting short-circuiting: Essential for maintaining safety and functionality.
- Dissolving lithium salts: Allowing seamless ion transport.
Anodes and Cathodes: Materials Breakdown
Both anodes and cathodes are critical to the charging and discharging process in lithium batteries. Each electrode serves distinct functions and is composed of different materials, impacting performance, capacity, and overall efficiency.
Anodes:
The anode is primarily responsible for hosting lithium ions when the battery is charging. The most common material used for anodes is graphite due to its excellent ability to intercalate lithium atoms. However, emerging materials like silicon are drawing attention because they can store even more lithium, significantly increasing energy density. Some of the challenges with silicon include expansion upon lithium ion absorption, which can degrade battery structure over time.
Cathodes:
The cathode, on the flip side, releases lithium ions during the discharge process. Materials used in cathodes include lithium cobalt oxide and lithium iron phosphate, both of which have different benefits and drawbacks. For instance, lithium cobalt oxide offers high energy density, making it suitable for smartphones, while lithium iron phosphate is favored for its safety and thermal stability in electric vehicles.
In summary, the choice of materials for both anodes and cathodes dramatically influences not only the performance but also the safety and cost-effectiveness of lithium batteries. Distinctions in material properties lead to varying applications across sectors, making it essential for manufacturers to carefully select these components based on end-use applications.
Quote:
Material Sourcing and Supply Chain Dynamics
The backbone of lithium battery manufacturing lies in its material sourcing and the intricate web of supply chain dynamics. Understanding this topic is crucial, as it sets the stage for the quality and efficiency of battery production. Each step in sourcing impacts not just the final product, but also the economic and environmental aspects surrounding battery manufacturing. Efficient material sourcing can lead to lower production costs, improved sustainability, and reduced environmental footprint.
Mining and Processing Lithium
The journey of lithium begins in the earth, where it is found chiefly in two forms: lithium brines and hard rock deposits. The most common method of lithium extraction is through evaporation ponds, primarily located in regions like the Salar de Atacama in Chile or the Lithium Triangle, which spans parts of Argentina, Bolivia, and Chile. Once extracted, lithium must undergo a series of processing steps, which typically include crushing, grinding, and chemical treatment to remove impurities.
Less frequently, lithium is mined from hard rock, like spodumene. This method involves traditional mining techniques—digging, blasting, and transporting ore—but is often more resource-intensive. Regardless of the method, the goal is to produce lithium carbonate or lithium hydroxide, both key inputs for battery manufacturing.
"The key to lithium battery efficiency lies in the purity of lithium sourced and the processing methods employed."
Global Supply Chain Analysis
The global landscape for lithium sourcing is noteworthy. Australia currently dominates the hard rock production of lithium, while countries in South America lead in lithium brine extraction. However, the supply chain is a multifaceted network, influenced by factors such as geopolitical tensions, trade regulations, and market demand.
- Key Players: Major contributors include Albemarle Corporation in the United States, SQM in Chile, and Tianqi Lithium from China. These companies have an essential role in shaping the supply chain and influencing lithium prices.
- Transport Logistics: Once lithium is extracted and processed, it must be shipped to manufacturing facilities worldwide. Shipping prices, routes, and regulations can dramatically affect delivery times and costs.
- Market Dynamics: Fluctuations in demand for electric vehicles and consumer electronics have made lithium a hot commodity in the markets. Increasing need drives not only supply but also a search for alternatives, which is vital for sectors vying for sustainability.
Challenges in Material Sourcing
While the potential for lithium battery production is seemingly limitless, hurdles abound in the sourcing of materials. Environmental concerns loom large over the mining of lithium, particularly in water-scarce regions. The evaporation process used in brine extraction requires vast amounts of water, leading to ecological concerns about local water supplies.
Additionally, there’s an ongoing battle for resources among manufacturers, often leading to over-exploitation of lithium-rich regions which can cause environmental degradation.
Consider a few of the primary challenges:
- Sustainability Issues: The extraction processes can harm local ecosystems and communities, raising questions about the sustainability of lithium sourcing.
- Resource Geopolitics: Countries reliant on lithium exports may leverage their resources for political advantage, which could disrupt supply chains.
- Regulatory Changes: Changes in environmental regulations can impose added challenges. Manufacturers need to stay adaptable to navigate these shifts smoothly.
By understanding the dynamics of material sourcing, the lithium battery sector can better address these challenges, paving the way for continued advancements in technology without compromising environmental integrity.
Lithium Battery Manufacturing Processes
The process of manufacturing lithium batteries is both complex and pivotal in the broader context of energy storage technology. Understanding the specifics of how lithium batteries come together is essential for anyone involved in their development, usage, or regulation. Each step in the manufacturing process contributes to the overall performance, safety, and sustainability of the final product. With increasing global demand for energy storage solutions, the manufacturing processes themselves are under constant scrutinization for efficiency and innovation.
Cell Assembly Techniques
The cell assembly stage is crucial as it brings together all components to form the energy storage unit. One notable technique in this phase is the dry electrode process. This involves applying the active material onto the current collector without using any solvents. This method not only reduces chemical waste but also enhances the energy density of the battery.
Other assembly techniques include:
- Layering: This method stacks the anode, separator, and cathode in alternating layers, optimizing energy flow.
- Tabbing: This includes connecting the electrodes through tabs, ensuring effective electron transfer and maintaining structural integrity.
These techniques not only speed up the manufacturing process but also play a significant role in improving the battery's overall cycle life. Optimizing each of these assembly methods can make a considerable difference in performance metrics such as charge time and capacity.
Electrode Fabrication
Electrode fabrication lays the foundation for lithium battery performance. High-quality electrodes are integral to a battery’s energy capacity, longevity, and efficiency. Generally, the fabrication process involves coating a conductive substrate with a slurry made of active material, binder, and solvent, but it extends well beyond that.
Key aspects of electrode fabrication include:
- Material Selection: Choosing appropriate materials for electrodes significantly affects conductivity and capacity. Common materials include graphite for anodes and lithium cobalt oxide for cathodes.
- Thickness Control: The thickness of the electrode layers can influence performance. Thicker electrodes may boost capacity, but they can also lead to longer charge times.
- Quality Assessments: Implementing strict quality controls during fabrication ensures the materials meet necessary specifications, preventing defects that could lead to battery failure.
Electrode fabrication is not merely a mechanical process; it heavily influences the electrochemical properties of the final product.
Sealing and Packaging
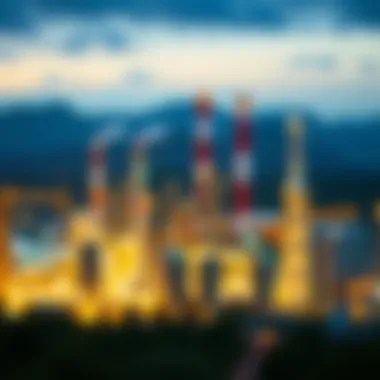
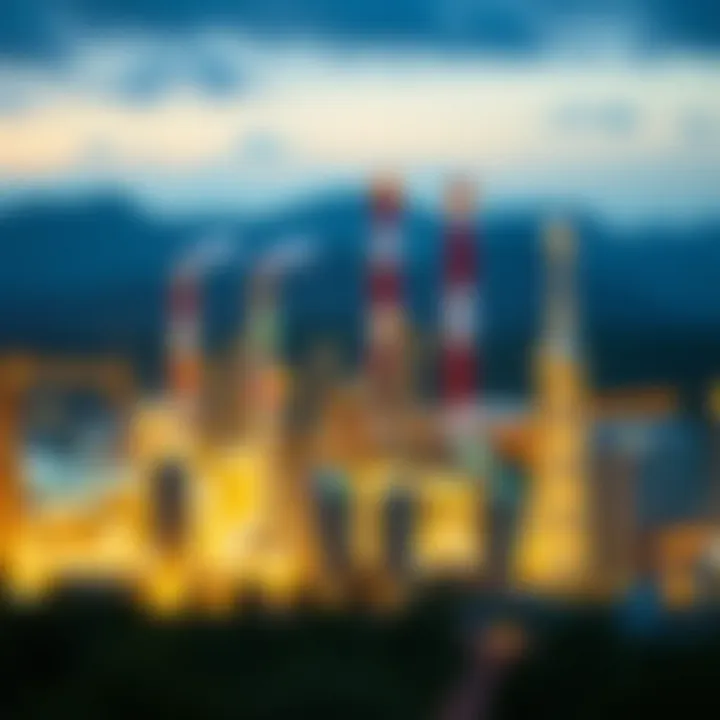
After the assembly and fabrication of lithium batteries, sealing and packaging become the last critical steps. This phase not only secures the integrity of the cells but also insulates them from external environmental factors like moisture and air, which can degrade performance over time. The choice of packaging material can affect both safety and efficiency.
"Proper sealing prevents risks like thermal runaway, a critical safety concern in lithium battery operation."
Important considerations for sealing and packaging include:
- Material Durability: Packaging should be made of robust materials that can withstand heat and mechanical stress.
- Thermal Management: Solutions that incorporate thermal control measures can prolong the lifespan and efficiency of the batteries.
- Automated Systems: Employing automation in the sealing process enhances consistency and reduces the risk of human error.
In essence, efficient sealing and effective packaging are integral to maintaining battery performance and safety across various applications, from consumer electronics to electric vehicles.
Technological Innovations in Battery Production
In recent years, the lithium battery industry has been a hotbed of technological advancements. These innovations are not just for show; they are pivotal in enhancing the efficiency, sustainability, and performance of lithium batteries. As demand for electric vehicles and renewable energy sources grows, the need for robust and efficient battery technology becomes increasingly critical. Without doubt, innovation in this domain has the potential to revolutionize not only battery production but also influence related fields such as energy storage and electric mobility.
Advanced Manufacturing Techniques
When one speaks about advanced manufacturing techniques, it encompasses a broad array of processes that aim to optimize production efficiency while ensuring high-quality end products. These methods integrate cutting-edge technology to enhance the consistency and performance of lithium batteries.
One notable technique is the use of dry electrode technology. Unlike traditional wet methods that require the addition of solvents, dry processes can reduce manufacturing time and improve energy density by eliminating unnecessary materials. This method significantly minimizes the environmental impact of production, addressing some of the ecological concerns highlighted earlier.
Furthermore, additive manufacturing, or 3D printing, is making waves. Its application allows for the creation of complex structures that are often impossible to achieve through conventional methods. By optimizing the design of batteries, engineers can improve energy storage capabilities and reduce waste. To illustrate, utilizing 3D printing in prototype development speeds up the design cycle and enhances customization, fulfilling specific requirements of various applications.
Key Benefits of Advanced Techniques
- Cost Efficiency: Reduction in material waste and lower production costs are fundamental advantages.
- Quality Improvement: Consistency and reliability of the battery cells are significantly enhanced, leading to better overall performance.
- Sustainability: Many advanced techniques focus on eco-friendliness, minimizing the carbon footprint associated with battery production.
Automation and Industry 4.
As the manufacturing landscape evolves, the advent of Industry 4.0 is set to reshape lithium battery production beyond recognition. This term describes the fourth industrial revolution, characterized by the integration of digital technologies, data exchange, and automation in manufacturing.
The rise of smart factories is one prominent aspect of this shift. In these environments, interconnected machines communicate with one another, sharing real-time data that enables optimization of production processes. For example, sensors can monitor equipment performance and predict maintenance needs, reducing downtime and enhancing overall efficiency.
Moreover, automation plays a crucial role in scaling up production. With robots handling repetitive tasks, the potential for human error decreases, which in turn enhances precision and safety. Additionally, automated systems can operate around the clock, responding to market demands swiftly while adhering to stringent quality standards.
“The integration of automation in lithium battery manufacturing will distinguish the leaders in the field from the followers, offering a competitive edge essential for survival in today's fast-paced market.”
Considerations for Implementation
- Investment Costs: Transitioning to automated systems can require sizable initial investments.
- Skilled Workforce: A well-trained workforce capable of managing and operating advanced technologies is essential.
- Continuous Improvement: Organizations must be committed to continual assessment and upgrading of their systems to keep pace with evolving technologies.
Quality Control in Lithium Battery Production
Quality control is the backbone of reliable lithium battery manufacturing. With the increasing demand for better performance, safety, and longevity of batteries in various applications—from electric vehicles to consumer electronics—ensuring the quality of each product has never been more critical.
Benefits of Quality Control
Quality control helps to prevent defects that can jeopardize safety and efficiency. It involves systematic testing and evaluation throughout the production process to ensure that each component meets specific standards. This not only safeguards the end-users but also enhances the reputation of manufacturing companies.
There are several key elements that make quality control essential in lithium battery production:
- Reliability: High-quality batteries contribute to the reliability of devices, ensuring they function as intended for extended periods.
- Safety: Defective batteries can lead to serious hazards such as overheating or fires. A robust quality control process minimizes these risks.
- Performance: Quality assurance optimizes battery performance, which directly relates to battery capacity and recharge cycles.
Considerations in Quality Control
Manufacturers must consider several factors when implementing quality control measures, including:
- Material Integrity: Using superior quality raw materials is the first step to ensuring that the battery has the potential for optimal performance.
- Process Monitoring: Continuous monitoring of manufacturing processes is indicative of how consistently the final products maintain desired features.
- Final Testing Protocols: A defined set of tests must verify each battery's functionality before it reaches consumers—these tests cover capacity, voltage, leakage, and cycle life, among others.
"In any manufacturing sector, but especially in battery production, rigorous testing acts as the guardian angel for product integrity and user safety."
Testing Methods
Testing methods vary greatly, as different aspects of the battery require distinct approaches. Among these, the most common testing techniques in lithium battery production include:
- Visual Inspections: Basic checks for physical defects in the battery cells, such as corrosion or tears in the packaging.
- Performance Testing: Evaluating the battery’s performance under simulated real-life conditions. This is particularly important for ensuring that batteries won’t drop in efficacy unexpectedly during use.
- Electrochemical Tests: These tests assess the battery's capability to hold charge, discharge rates, and overall stability across varying temperatures.
Standards and Certifications
Adhering to industry standards and certifications is pivotal for establishing quality control protocols. Compliance with these guidelines not only enhances safety but also builds consumer trust.
Below are some notable standards relevant to lithium battery manufacturing:
- ISO 9001: This is a standard that specifies requirements for a quality management system, ensuring that manufacturers consistently provide products that meet customer and regulatory requirements.
- UL Certification: Products that undergo UL certification have been rigorously tested to meet safety requirements significant to consumer electronics.
- IEC 62133: This international standard concerns the safety requirements for portable sealed secondary cells, particularly in relation to lithium batteries used in consumer electronics.
Ensuring compliance with the above standards is essential in optimizing quality control, instilling confidence in both manufacturers and end-users.
Environmental Impact of Lithium Battery Manufacturing
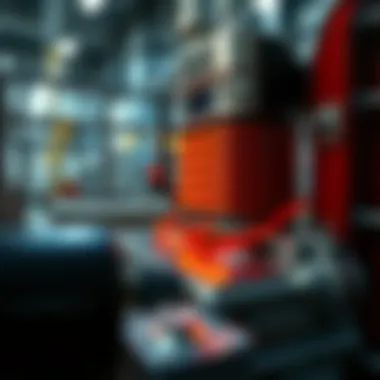
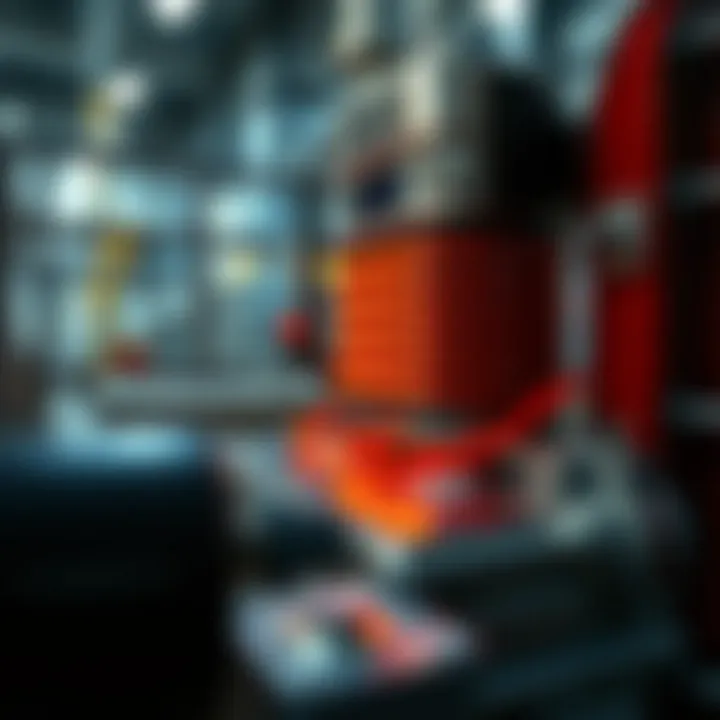
The production of lithium batteries has become a crucial topic in today’s tech-driven world, especially given our relentless hunt for cleaner energy solutions. While lithium batteries are heralded for their role in renewable energy, electric vehicles, and portable electronics, their production processes entail significant environmental considerations that cannot be overlooked.
Producing lithium batteries involves extensive resource extraction, with mining activities often affecting eco-systems. This topic serves as a reminder that while lithium technology enables sustainable practices, its manufacturing footprint can be quite substantial.
With these points in mind, this section delves into the specific ecological concerns in lithium sourcing, as well as the waste management strategies that can mitigate the environmental impact of these batteries.
Ecological Concerns in Lithium Sourcing
Lithium sourcing primarily occurs through hard rock mining and brine extraction. Each method has its own set of ecological implications.
- Hard Rock Mining: This technique involves removing vast swaths of earth to access lithium-rich ores. Such activity can result in deforestation, habitat loss, and soil erosion. It dramatically alters the landscape, often with lasting effects on local biodiversity. The disruption caused to flora and fauna can disturb ecosystems for generations.
- Brine Extraction: This process is often simpler on the surface but carries its own environmental baggage. Pumping brine from underground reserves can deplete groundwater supplies, which can lead to water scarcity in arid regions. Additionally, the evaporation of brine in large salt flats can result in chemical contamination of surrounding soil and water bodies, presenting risks for local communities and wildlife.
Both methods are not without their controversies. Environmental regulations vary widely across countries, with some regions lacking robust frameworks. This inconsistency raises ethical concerns regarding sustainable practices in lithium sourcing and highlights the need for stricter regulations and better practices in monitoring and protecting the environment.
“Because lithium is the backbone of the modern tech age, understanding its sourcing impacts is critical for sustainable development.”
Waste Management Strategies
Once lithium batteries reach the end of their life cycle, addressing the associated waste is imperative. Improper disposal can lead to environmental hazards, including leakage of toxic substances and heavy metals into the ground and water supplies.
To prevent such outcomes, several waste management strategies must be put into practice:
- Recycling Programs: Encouraging battery recycling can reduce waste while recovering precious materials like lithium, cobalt, and nickel. Properly recycling old batteries can lower the demand for newly mined materials, thus reducing the environmental toll.
- Battery Collection Initiatives: Mobilizing community efforts to collect used batteries for safe disposal or recycling is essential. Special collection bins in public places can facilitate this effort and raise awareness about the importance of recycling.
- Innovative Technologies: Developing more efficient recycling technologies can also ensure a higher yield of recoverable materials while reducing processing emissions.
- Legislation and Incentives: Governments can enhance recycling rates through legislation that mandates battery recycling and provides incentives for companies that adopt sustainable practices. This can help ensure that waste is managed responsibly, minimizing the environmental impact of battery production.
Future Trends and Challenges in the Industry
The landscape of lithium battery manufacturing is rapidly evolving, driven by advances in technology and increasing demand for sustainable solutions. Understanding the future trends and challenges in the industry is crucial as it sets the stage for innovations that can reshape energy storage and consumption. The next phase of battery development is not just about improving performance; it also encompasses environmental considerations, material sourcing, and new market dynamics.
Emerging Technologies in Battery Design
In recent years, emerging technologies have begun to redefine lithium battery design. From solid-state batteries to lithium-sulfur systems, these innovations promise to enhance energy density and safety. :
- Solid-State Batteries: By using a solid electrolyte instead of a liquid one, these batteries can significantly reduce flammability risks and increase energy density. This could mean smaller, lighter batteries that hold more energy.
- Lithium-Sulfur Batteries: They offer the potential for up to five times the energy density of conventional lithium-ion batteries. This is mainly due to sulfur's abundance and low cost.
- Flexible and Miniaturized Batteries: With the growth of wearable technology, there's a push for batteries that are not just small but also flexible. These innovations can integrate into fabrics or even skin, opening up new horizons for health monitoring and other applications.
"Emerging technologies provide not just solutions but also promise a new way of thinking about energy storage and consumption".
Moreover, advancements in recycling technologies are gaining traction. The need to reclaim valuable materials like lithium, cobalt, and nickel has never been more pressing, as it addresses concerns over resource depletion and environmental degradation. These technologies not only encourage sustainable practices but also optimize the entire lifecycle of batteries, making them more economically viable.
Demand and Market Prognosis
The market for lithium batteries is skyrocketing, poised for incredible growth over the next decade. Factors such as the rise of electric vehicles, renewable energy storage, and portable electronics are all fueling this demand. According to several industry forecasts, the lithium battery market could reach $100 billion by 2025.
Key elements influencing this demand include:
- Electric Vehicles (EVs): One of the major drivers is the accelerating production of EVs as countries push for cleaner transport solutions. Major companies like Tesla and traditional automakers are investing heavily in lithium-based technologies.
- Energy Storage Systems: Solar and wind energy are intermittent, thus creating a need for efficient storage solutions. Lithium batteries provide a reliable way to store energy generated from renewable sources.
- Consumer Electronics: Devices like smartphones and laptops continue to be fundamental consumers of lithium batteries, but the emergence of smart and interconnected devices is scaling this demand further.
However, the market prognosis isn’t without its challenges. The volatility in lithium prices, issues with mining and supply chain constraints, as well as regulatory pressures related to environmental impacts, are concerns that could impede growth.
Ending
The conclusion of this comprehensive examination on lithium battery manufacturing is crucial for readers who are keen on grasping the intricacies of this vital technology. As we face the pressing challenges of energy sustainability and increasing demand for portable power sources, understanding lithium battery production becomes paramount. It not only encapsulates the entire manufacturing journey — from sourcing raw materials to the quality control measures applied post-production — but also reflects on the situations that could impact future growth and innovation in this sector.
In summary, three significant elements emerge:
- Technological Innovation: The advancements in manufacturing processes are redefining the landscape, making production more efficient and environmentally friendly.
- Environmental Concerns: A growing awareness of ecological impacts means future manufacturing processes must align with sustainable practices to ensure responsible sourcing and waste management.
- Market Influences: Fluctuations in demand and market dynamics shape the availability and cost of materials, affecting both the production cycle and future research directions.
Understanding these factors not only benefits stakeholders in the battery supply chain but also ensures that consumers and researchers alike remain informed about the evolving nature of technology, sustainability, and market trends. As we move forward, these insights will serve as both a roadmap and a cautionary tale, highlighting the responsibilities of those involved in this industry.
Recap of Key Insights
Reflecting on the key insights from the exploration, a few critical points resonate:
- Lithium batteries are indispensable to contemporary technology, empowering everything from electric vehicles to portable electronics.
- The manufacturing processes are sophisticated, incorporating advanced materials and methods that optimize performance and longevity.
- A robust understanding of environmental implications is essential to navigate the sustainability challenges posed by lithium sourcing and battery production.
Ultimately, the insights shared within this article provide a comprehensive understanding of the current landscape, as well as anticipation of future developments that may arise as technology advances.
Implications for Future Research
Looking ahead, the implications for future research in lithium battery manufacturing are significant. Key areas that warrant attention include:
- Alternative Materials:
- Recycling Techniques:
- Innovation in Production:
- Market Dynamics:
- Exploring substitutes for lithium that may offer similar performance with minimized environmental impact.
- Developing more effective processes for battery recycling to recover valuable materials and reduce waste.
- Research into new manufacturing techniques that can enhance efficiency while remaining environmentally conscious.
- Continuing studies on how geopolitical and economic factors influence the availability of raw materials and the pricing of batteries.
Overall, encouraging innovation and sustainability in lithium battery manufacturing holds the promise of reshaping not just the industry but also its role in global energy consumption. For researchers, educators, and professionals, engaging deeply with these implications presents an opportunity to contribute to a lasting impact in advancing battery technologies for a more sustainable future.