Understanding the Plastic Production Process
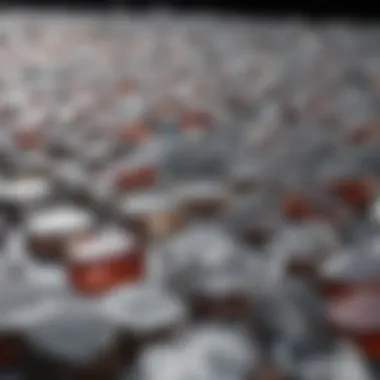
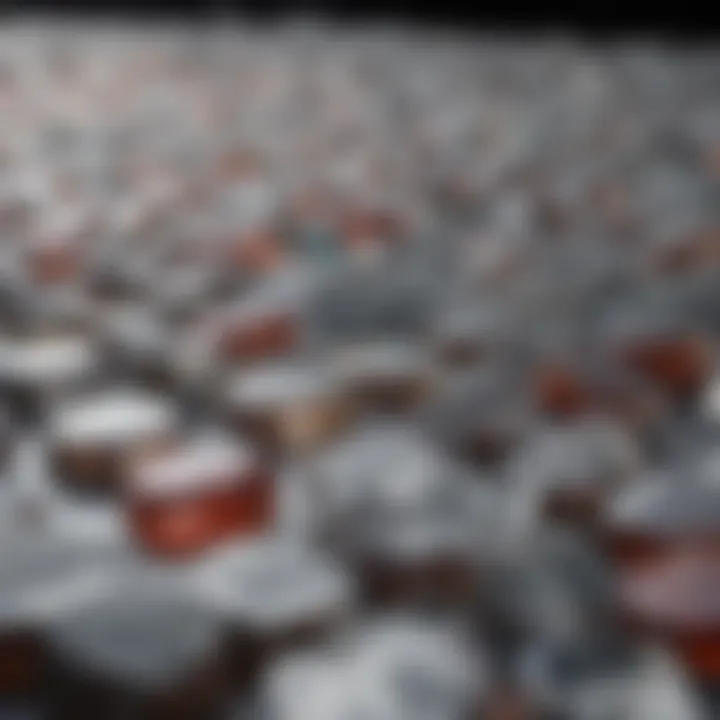
Intro
Plastic has woven itself into the fabric of daily life, appearing in everything from packaging materials to intricate electronic components. The very mention of plastic often conjures images of convenience and innovation, yet behind this ubiquitous material lies a complex tapestry of processes and reactions. Understanding how plastic is produced not only sheds light on its significance in modern society but also on the environmental consequences that come with its production. In this article, we will explore the raw materials, the chemical processes, and the technological advancements that drive the plastic industry, all while keeping an eye on sustainability efforts and the future of plastics in our ever-changing world.
Research Overview
Summary of Key Findings
The lifecycle of plastic production begins with natural resources such as crude oil and natural gas. Through various chemical transformations, these resources are turned into polymers capable of being molded into countless forms. Innovations in manufacturing processes have greatly increased efficiency, yet concerns about pollution and waste generation have led to calls for improved recycling methods and environmentally-friendly alternatives.
Key points include:
- The role of hydrocarbon feedstocks in polymer synthesis.
- Innovative technologies that enhance production efficiency, such as 3D printing.
- An overview of the environmental impact stemming from plastic waste.
Significance of Research
This research is of utmost importance because it highlights the intricate relationship between society and material science. As plastic continues to be a staple in numerous industries, understanding its production processes paves the way for innovation in sustainability practices. Gaining insights into these processes can equip both individuals and corporations with the knowledge to make informed decisions about plastic use and disposal, which is increasingly essential in today's environmentally-aware consumer culture.
Methodology
Research Design
To delve into the various aspects of plastic production, a mixed-methods approach can be highly effective. This encompasses qualitative analyses of environmental impacts and quantitative data on production efficiencies and material usage. By examining case studies from various regions of the world, researchers can pinpoint how different methodologies are applied in practice.
Data Collection Methods
Data may be gathered through a combination of:
- Interviews with industry experts
- Surveys targeting production companies
- Analysis of existing literature on plastic manufacturing
Utilizing these diverse methods ensures a comprehensive overview of the plastic landscape, emphasizing varied practices and innovative solutions that are emerging globally.
"Examining plastic production not only reveals the complexity of materials we often take for granted but also informs modern challenges in sustainability and environmental stewardship."
Through this groundwork, the subsequent sections will explore the processes involved from raw material extraction to the recycling pathways vital for the reduction of environmental damage.
This overview set the stage for a more in-depth examination of each step in plastic production, paving the way for a thoughtful discussion on the future of this essential material.
Preface to Plastic
Understanding plastic is essential in today's world where it's an omnipresent material. The modern consumer's life is intertwined with plastic products, from everyday items to advanced technological applications. The processing of plastics plays a significant role in driving both economic growth and innovative solutions to many challenges.
Definition of Plastic
Plastic refers to a wide range of synthetic or semi-synthetic materials that have the capability to be molded into various forms. At its core, plastic is polymer-based. The term is derived from the Greek word "plastikos," meaning "capable of being shaped or molded." Plastics can be rigid or flexible depending on formulation and processing conditions.
Common types include:
- Polyethylene (PE): Most widely used plastic, found in bags and bottles.
- Polyvinyl Chloride (PVC): Used in pipes and electrical cable insulation.
- Polystyrene (PS): Employed in disposable cups and packaging materials.
These materials are further divided into thermoplastics, which can be reheated and reshaped, and thermosetting plastics, which harden permanently after being set.
Historical Context
The history of plastic is a fascinating saga that spans over a century. The first synthetic plastic, Bakelite, was created in 1907 by Leo Baekeland. It marked the beginning of a new era where flexible and resilient materials could be produced on a large scale. Following Bakelite, the development of nylon in the 1930s by Wallace Carothers heralded the dawn of synthetic fibers, which reshaped industries like textiles and consumer goods.
In the post-World War II era, plastic replacements surged, driven by mass production and a growing consumer culture. This also brought forth an array of concerns regarding durability, disposal, and environmental impact, leading to the current focus on sustainability. For instance, at present, approximately 8 million tons of plastic end up in the oceans each year. This historical backdrop is vital for grasping the environmental implications and the need for innovation in recycling and sustainable practices.
Raw Materials Used in Plastic Production
The topic of raw materials is critical in understanding the overall process of plastic production. It serves as the backbone for everything that follows, making it essential for one to grasp the nuances involved in sourcing these materials. The selection of raw materials defines not only the properties of the finished plastic but also its environmental impact, production cost, and availability. Without these raw inputs, the intricate dance of polymerization, molding, and manipulation that characterizes plastic manufacturing wouldnât even begin.
Natural Resources
Petroleum
Petroleum stands out as the primary raw material for producing most common plastics. It is refined into various hydrocarbons that serve as the building blocks for polymers. Characteristics of petroleum include high energy content and its versatility in creating a wide range of plastic types, from soft flexible films to rigid containers. One key advantage is availability; it is abundant and relatively easy to extract in many regions worldwide. However, reliance on petroleum has a flip side, as its extraction and use have significant environmental consequences, contributing to pollution and greenhouse gas emissions. This contradiction showcases the challenge faced by the industry: balancing the immediate benefits with long-term sustainability goals.
Natural Gas
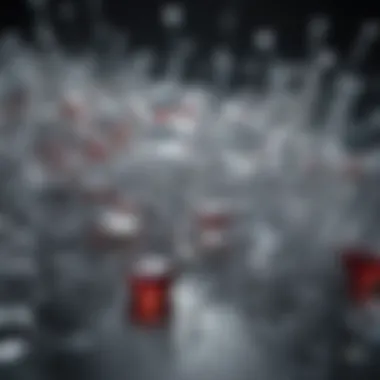
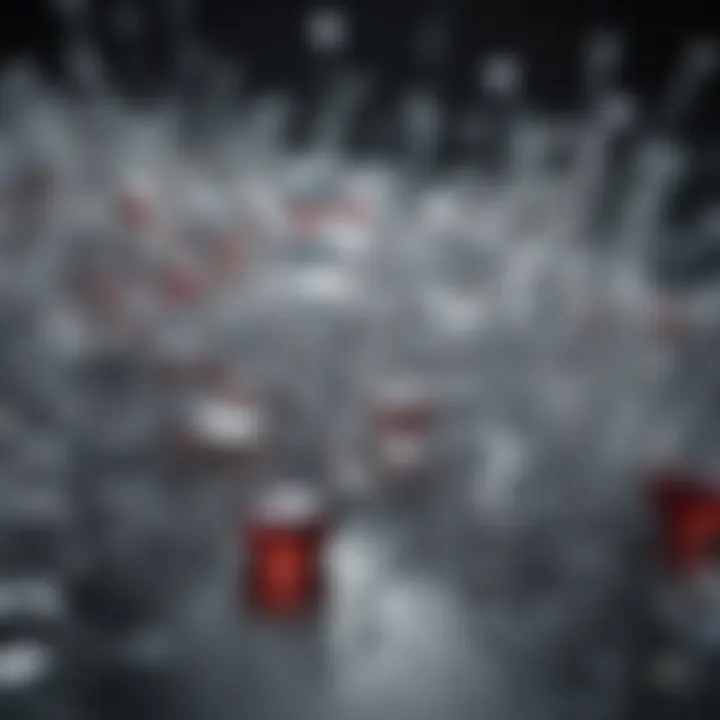
Natural gas emerges as another prominent resource, particularly in the production of polyethylene and polypropylene. Its key feature is that it can be cleaner than petroleum in terms of emissions when burned or used. This aspect makes it an appealing choice for manufacturers striving to lower their carbon footprint. The unique attribute of natural gas is its relatively low carbon content compared to other fossil fuels. Yet, the extraction and potential for leakage during transportation raise concerns that cannot be overlooked. Thus, though it offers certain advantages, it's imperative to proceed with caution, considering the broader environmental implications of its use.
Cellulose
Cellulose, a natural polymer sourced mainly from plants, provides an intriguing counterpoint to fossil fuels. Utilizing cellulose aligns with the concept of renewable resources, which is increasingly relevant today. Cellulose-based plastics can biodegrade under certain conditions, presenting an advantage in reducing waste. Moreover, their compatibility with various additives opens doors for creating bio-composites that can be equally strong as traditional plastics. However, the production of cellulose involves agricultural processes, which could put pressure on land use and biodiversity if not managed properly. Thus, while cellulose offers unique benefits, one must evaluate the ecological footprint of its sourcing.
Synthetic Alternatives
Coal
Coal is an often overlooked raw material in plastic production. Its primary advantage lies in being one of the most abundant sources of energy, and it can be transformed into products like benzene, toluene, and xyleneâkey precursors in making plastics. The crux of coalâs appeal comes from its low cost and extensive availability, especially in regions rich in coal deposits. However, one cannot ignore the highly detrimental environmental effects associated with coal mining and combustion. The high carbon emissions and pollution it generates stand in stark contrast to the goals of sustainable production practices.
Bio-based Materials
Bio-based materials are gaining traction as a sustainable alternative to traditional raw materials. They are produced from renewable resources, thus promising a lower environmental impact. A significant characteristic of these materials is the potential to reduce reliance on fossil fuels, which aligns with global sustainability initiatives. The notable feature of bio-based plastics is their ability to be designed for specific applications while still being more eco-friendly. However, challenges remainâlike reliability, scalability, and costâthat make it difficult to replace petroleum-based plastics entirely. Navigating through these complexities is crucial as we forge ahead into a landscape increasingly concerned with sustainability.
Chemical Processes in Plastic Manufacturing
The realm of plastic manufacturing hinges on several critical chemical processes. These techniques not only sculpt the physical attributes of plastic but also have a direct impact on its functionality and environmental footprint. The chemical intricacies involved play a crucial role in defining how plastics perform, their longevity, and their impact when they eventually find their way into the environment. Thus, understanding these processes is vital not only for manufacturers but also for those concerned with the wider ecological effects.
Polymerization Techniques
Polymerization stands at the heart of plastic creation. This pivotal reaction process links small molecules, known as monomers, into long-chain structures called polymers, which are the essence of plastics. There are two primary pathways to achieve this â addition and condensation polymerization â each with its own unique characteristics and implications.
Addition Polymerization
In addition polymerization, monomers possessing a double bond or some reactive group join together without the loss of any byproduct. This simplicity is a key trait that makes addition polymerization widely appreciated in the production of materials like polyethylene and polystyrene. Its appeal lies in its ability to create high molecular weight polymers rapidly and efficiently.
The major benefit here is that the process can be initiated using a variety of catalysts or heat, allowing for flexibility in manufacturing. A unique feature of this method is the potential for custom-tailored properties in the final product, enabling manufacturers to tweak characteristics such as clarity, hardness, and temperature resistance. However, it may also lead to disadvantages such as chain transfer reactions which can change the molecular weight of the resultant polymer, potentially affecting its performance.
Condensation Polymerization
Condensation polymerization, on the other hand, is a bit more complex. In this process, monomers join together, releasing a small molecule, typically water or methanol, as a byproduct. This characteristic is what makes this method significant in producing materials like nylon and polyester.
One of the key features of condensation polymerization is the formation of more rigid and high-strength materials due to the cross-linking of chains during the reaction. This gives manufacturers an edge when designing applications that require durability. However, the byproduct generation is a double-edged sword; it means thereâs a need for additional processing to remove these byproducts, which can complicate production and increase costs.
Extrusion
Extrusion is an essential manufacturing process whereby plastic is melted and formed into continuous shapes. This involves feeding plastic pellets into an extruder where theyâre heated before being forced through a die. The flexibility to create various shapesâsuch as pipes, sheets, and filmsâmakes extrusion a go-to technique in the industry. Furthermore, extrusion integrates seamlessly with additional processes like blow molding, streamlining workflows and reducing production costs. However, it is essential to monitor temperature closely to avoid degradation of the material, as improperly managed conditions can lead to quality concerns.
Injection Molding
Injection molding is another key method widely utilized in the production of plastic products. In this process, melted plastic is injected into a mold where it cools and solidifies into the desired shape. One crucial benefit of injection molding is its ability to produce large volumes of highly complex shapes in a consistent and efficient manner. High precision is often required, especially for intricate designs, which makes the process ideal for items such as automotive parts and household goods. Nevertheless, the initial setup cost for molds could be a downside, especially for smaller runs; however, once established, the per-unit cost typically drops.
"Understanding these chemical processes not only facilitates superior product design but also informs better practices regarding sustainability and environmental stewardship"
The Role of Additives in Plastic Production
When discussing the fabric of plastic production, one cannot overlook the significance of additives. These compounds serve crucial roles in enhancing the properties of plastic materials, ensuring they meet specific application standards. The presence of additives can turn a basic polymer into a multifaceted material, capable of fulfilling numerous requirements in diverse industries.
Additives can offer a host of benefits, such as improving durability, enhancing aesthetic appeal, and ensuring stability under varying environmental conditions. As products manufactured from plastic become even more embedded in our daily lives, understanding these additives is essential for anyone in the field, from manufacturers to consumers.
Colorants and Fillers
Colorants and fillers hold a pivotal position in the additive landscape. Colorants provide the aesthetic element, permitting plastics to exhibit a wide palette of colors, making them more appealing to consumers. This is especially true in the packaging sector, where a striking visual can be a deciding factor for potential buyers.
Fillers, on the other hand, primarily serve functional purposes. They are incorporated to increase the volume of the material, reduce costs, and alter physical properties like strength and rigidity. Various types of fillers can be employed:
- Calcium carbonate: Often used for its cost-effectiveness and ability to reinforce plastic.
- Talc: Known for improving stiffness and heat resistance.
Despite the advantages, using fillers requires careful consideration. Adding too much can lead to lack of flexibility or make the final product brittle. Striking the right balance involves science and a touch of art.
"The right additive can make or break a plastic product; it's not just about adding ingredients but about elevating performance."
Stabilizers and Modifiers
Stabilizers and modifiers are another key category of additives, playing a significant role in enhancing the longevity and usability of plastics. Stabilizers help to mitigate degradation caused by environmental factors, such as heat and light. Without these protective additives, plastic can weaken and deteriorate over time, leading to potential failures in performance.
Modifiers adjust the properties of plastics to better suit their intended use. For example:
- Impact modifiers: Enhance the toughness of the material, ensuring it can withstand rough handling.
- Processing aids: Facilitate smoother manufacturing processes, making it easier for manufacturers to create complex shapes or improve the flow of the molten plastic.
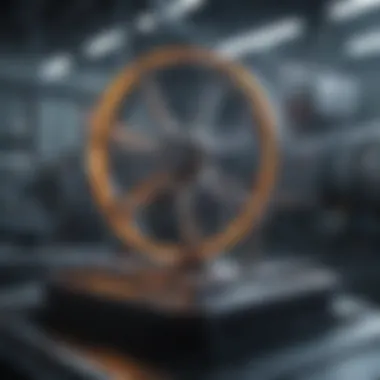
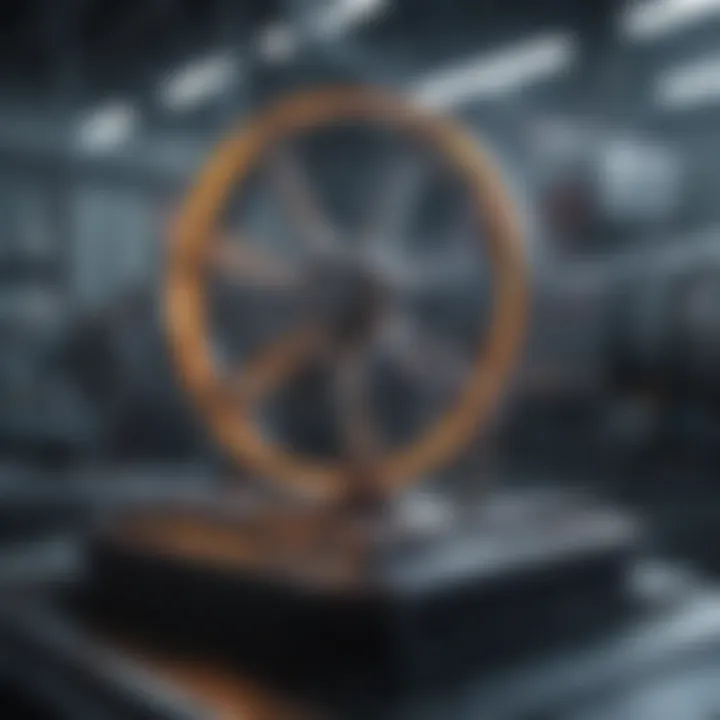
Through their various applications, stabilizers and modifiers highlight the complexity of plastic production and the extent to which additives can impact the final product's integrity and functionality. Thus, understanding their roles is critical for anyone engaging with plastic materials today.
Manufacturing Processes Involved
The manufacturing processes involved in plastic production play a foundational role in determining the characteristics and usability of the final plastic products. Each method brings its own set of advantages, requirements, and specificities that cater to various applications throughout numerous industries. Understanding these processes is crucial not only for production efficiency but also for ensuring that the materials produced meet the diverse needs of consumers.
Each technique is designed to shape plastic materials in ways that can be optimized for functionality, design, and performance. The choice of manufacturing process often depends on the desired properties of the final product, cost considerations, and environmental impacts. On the whole, these processes are the heartbeat of plastic productionâthrough them, raw materials are transfigured into the essential commodities we rely on daily.
Blow Molding
Blow molding is a prominent manufacturing technique used primarily to create hollow plastic products. The process begins by heating a thermoplastic material until it is soft and pliable. This softened plastic is then formed into a preform shape and inflated with air, much like blowing up a balloon. Once the plastic cools and solidifies, the hollow object is formed.
This technique is particularly beneficial for producing a variety of containers, like bottles and tanks, due to its efficiency and scalability. The ability to create lightweight yet strong structures can significantly reduce material costs while maintaining product integrity. However, blow molding also requires careful control of temperature and pressure to avoid defects, which might result in uneven wall thickness or other structural issues.
Moreover, blow molding can be further divided into several subtypes, including:
- Extrusion Blow Molding: This method involves extruding a tube of molten plastic which is then captured in a mold.
- Injection Blow Molding: In this variation, a preform is first injected and then blow-molded, allowing for greater precision in the final product.
As the demand for eco-friendly packaging rises, blow molding technology is also adapting, with a focus on incorporating recycled materials into the process. This innovation not only aligns with current sustainability efforts but also enhances the overall appeal of products made through this method.
Thermoforming
Thermoforming is another essential process in the plastic manufacturing realm. It involves heating a plastic sheet until it becomes pliable, then forming it over a mold to create various shapes and designs. Once cooled, the plastic retains its new shapeâa beneficial trait for many industries.
Compared to other methods, thermoforming is noted for its simplicity and cost-effectiveness, especially when producing larger components. The process is widely utilized in creating trays, containers, and even parts for appliances. It offers advantages such as:
- Flexibility: Thermoforming can accommodate a wide range of plastic types, giving manufacturers the ability to select materials that best fit their production goals.
- Reduced Waste: Since the material can often be reused or recycled during production, thermoforming contributes positively to overall resource efficiency.
Yet, it is important to acknowledge that while thermoforming excels in speed and efficiency, it may not achieve the same level of precision as injection molding. This could be a critical consideration for applications where minute details are paramount.
In an era where sustainability is sought after, both blow molding and thermoforming are evolving. The exploration of alternative materials and processes enhances the industry's ability to adapt to increasingly stringent environmental regulations and consumer expectations.
"Manufacturing processes such as blow molding and thermoforming are critical to understanding plastic production; they shape not only the material but also the future of product innovation and sustainability."
Quality Control Measures
Quality control in plastic production stands as a vital pillar, ensuring that the end products meet the necessary specifications and safety standards. It's not just about making plastic items; itâs also about ensuring they perform reliably in their designated roles. In the fast-paced world of plastic manufacturing, overlooking quality control can lead to faulty products that may not only be ineffective but could pose safety hazards.
By implementing quality control measures, manufacturers can catch defects early, saving time and money while also protecting their reputation. This process typically involves a series of tests and evaluations throughout production, aiming to identify and correct any issues before the product reaches the market.
Testing Methods
Testing methods fall under the umbrella of quality control, and these methods are designed to evaluate various properties of the plastic products. The effectiveness and safety of plastic products hinge on thorough testing, and two primary methods stand out: Mechanical Properties Testing and Chemical Resistance Testing.
Mechanical Properties Testing
Mechanical properties testing examines the physical characteristics of plastics under various conditions. It determines how a plastic behaves under stress, such as tension, compression, and shear. This testing is crucial because it helps predict durability and functionality of plastic products in real-world applications, making it a beneficial choice in the article.
One of the key characteristics of mechanical properties testing is its focus on metrics like tensile strength, elasticity, and impact resistance. These characteristics give insight into how a product will respond when put to the test. For instance, understanding the tensile strength tells us how much force the material can handle before it deforms, which is vital for applications like construction or automotive components.
A unique feature of mechanical properties testing is its versatility. It can be conducted using various techniques, from simple methods like tensile testing to complex assessments like dynamic mechanical analysis. However, the downside is that these tests can be time-consuming and require specialized equipment, potentially leading to increased production costs if not managed well.
Chemical Resistance Testing
On the other hand, chemical resistance testing gauges how well a plastic can withstand exposure to chemicals, be it solvents, acids, or bases. This aspect is crucial in applications where plastics are used in harsh environments, such as laboratory settings or chemical plants.
The key characteristic of chemical resistance testing is that it provides the data needed to ensure product longevity and safety under specific conditions. This makes it an invaluable method for manufacturers looking to produce high-quality, reliable plastic. It indicates which materials are suitable for specific applications and assists in selecting the right polymers for optimal performance.
A unique feature of this testing method is its focus on real-world scenarios. Manufacturers can simulate conditions that the product might face, thereby predicting its behavior in actual use. However, like mechanical testing, it comes with drawbacks. It may require extensive testing over various chemicals, making it a resource-intensive process.
"Qualit control is not an extra step; it is an essential part of production that safeguards both the manufacturer and the user."
In summary, the quality control measures in plastic production, particularly through mechanical properties testing and chemical resistance testing, play a pivotal role in delivering safe and effective plastic products to the market. By prioritizing these methods, manufacturers can ensure they meet standards while also protecting their investments and consumers.
Environmental Impact of Plastic Production
The environmental impact of plastic production is pivotal in understanding not only the lifecycle of plastic materials but also their ramifications on our planet. It encompasses vital aspects that many often overlook, and this section aims to shed light on both the negative effects and potential paths forward. As we navigate through the various components of plastic manufacturing, it becomes clear that balancing production with sustainability is no small feat.
By examining the carbon footprint and water usage, we can grasp how these factors intertwine with environmental health, economic viability, and responsible stewardship of our planet.
Carbon Footprint
Plastics, while exceedingly versatile, come with a significant baggage in the form of carbon emissions. The production process is energy-intensive. Itâs estimated that the plastic industry contributes to a hefty share of global greenhouse gas emissions. The energy consumed primarily stems from fossil fuels, notably during the extraction of raw materials and polymer processing.
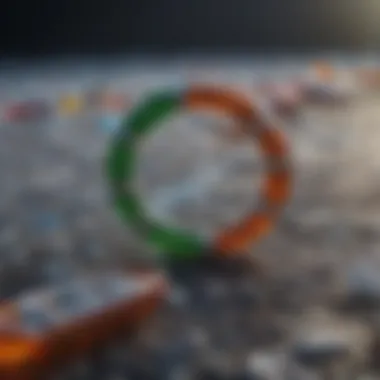
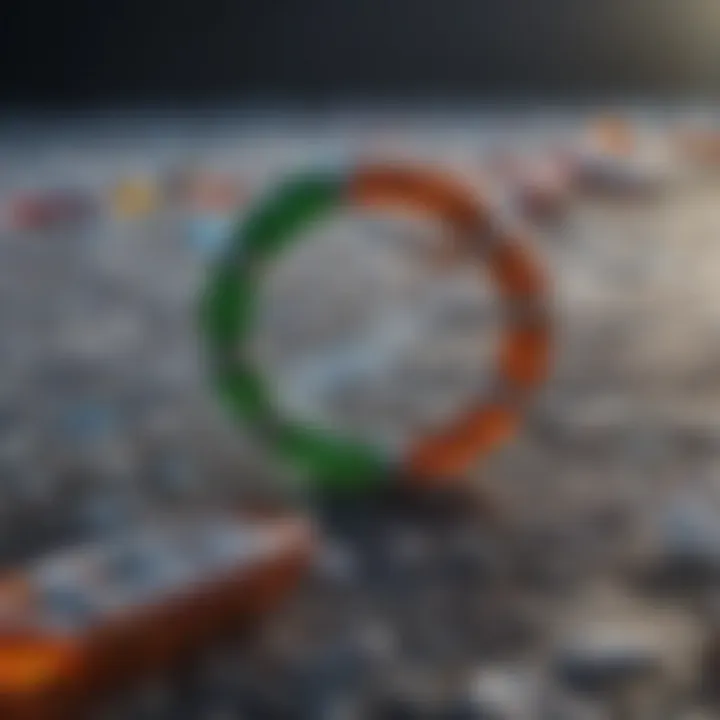
- Statistics show that for every ton of plastic produced, around 3 tons of greenhouse gases are emitted. This staggering figure underlines the urgency for reform in manufacturing practices.
Transitioning to cleaner energy sources, like solar or wind, for processing can drastically reduce these emissions. The advancement of carbon capture technologies is also a glimmer of hope in this venture. However, embracing these changes requires collaboration across the industry, engaging policymakers, businesses, and consumers alike.
"If we wish to shift the tide of climate change, tackling the carbon footprint of plastics is not just importantâitâs imperative."
Water Usage
Another critical yet often overlooked aspect of plastic production is water consumption. The production of plastics can be a thirsty process. Water is utilized in various stages, from cooling and washing to producing the materials themselves. This heavy use of water not only raises concerns about resource availability but could also affect local ecosystems.
In particular, regions that are already facing water scarcity can suffer greatly. Itâs essential to establish practices that minimize water wastage and optimize usage across the production lifecycle. Some measures include:
- Implementing closed-loop water systems that recycle and treat used water.
- Exploring alternative raw materials that require less water during processing.
- Enforcing stricter policies on water usage in facilities that produce plastics.
Through these adjustments, the industry can aim to lessen its impact on local water systems and better align itself with responsible environmental practices.
In sum, understanding the environmental impact of plastic production is essential for grappling with the broader implications of our plastic consumption habits. As the world leans towards improved recycling practices and sustainable alternatives, it is critical that discussions around carbon footprint and water usage remain at the forefront. Addressing these aspects diligently can pave the way for a more sustainable future.
Recycling and Sustainability Efforts
The pressing need for recycling and sustainability efforts in the plastic production process canât be overstated. With rising levels of plastic pollution, this topic holds significant relevance within the framework of modern manufacturing practices. These initiatives not only foster environmental preservation but also pave the way for innovative approaches that can transform waste management into resource management. Understanding the multifaceted benefits of these efforts cultivates a deeper appreciation for their crucial role in shaping a sustainable future.
Current Recycling Technologies
Mechanical Recycling
Mechanical recycling stands as a cornerstone in the field of plastic sustainability. This process involves the physical breakdown of plastic waste into smaller particles, enabling it to be remolded into new products without altering its chemical structure. The simplicity and efficiency of mechanical recycling make it a popular choice in recycling facilities worldwide. One of the main advantages of this method is that it typically requires less energy compared to chemical recycling, thus contributing to lower overall carbon emissions.
However, one unique feature of mechanical recycling is its limitations regarding the types of plastics that can be recycled. For instance, thermosets, which are often used in products like electronics and kitchenware, cannot be reprocessed through this method. As such, while mechanical recycling plays a significant role, it's not a one-size-fits-all solution. Therefore, reliance solely on this method can lead to challenges, especially with complex waste streams.
Chemical Recycling
On the other hand, chemical recycling offers a distinct approach. It breaks down plastic waste at the molecular level, converting it back into monomers or other basic chemicals. This process has the potential to recycle a broader range of plastics compared to mechanical recycling, including those considered non-recyclable through traditional means. A key characteristic of chemical recycling is its ability to produce high-quality recycled materials that can potentially be reused in brand-new products, preserving the integrity of the material.
Yet, this method isnât without its challenges. Chemical recycling often requires significant energy input and can be costlier to implement than mechanical processes. Additionally, there are concerns regarding the byproducts generated during the chemical breakdown process. These considerations necessitate a careful evaluation of when to employ this technology, highlighting a need for balanced approaches that leverage the strengths of both mechanical and chemical recycling.
Strategies for Sustainable Practices
Biodegradable Plastics
Biodegradable plastics present a promising solution in the quest for sustainability. These materials are designed to decompose naturally over time, differentiating them from traditional plastics that can linger in the environment for centuries. A notable advantage is that they can minimize landfill contributions and reduce the overall plastic footprint considerably. Biodegradable plastics are often made from renewable materials such as cornstarch, which can lead the path toward more environmentally-friendly plastic production.
Nevertheless, a major caveat is that biodegradable plastics often require specific conditions to break down effectively. If they end up in regular landfills, the absence of the right environmental factors may hinder their decomposition. Moreover, they can still release greenhouse gases if not managed correctly after disposal, making careful planning and effective waste management essential to maximize their potential benefits.
Reducing Plastic Waste
Reducing plastic waste is perhaps one of the most critical strategies in addressing plastic pollution. This can range from embracing minimalist packaging solutions to enhancing the lifecycle of plastic-based products. One key characteristic of this approach is its focus on prevention rather than just management. By targeting the sources of plastic production and consumption, it encourages industries and consumers to rethink their usage patterns.
The unique feature of this approach lies in encouraging practices like reusing containers and opting for alternative materials wherever possible. In contrast to recycling, reducing waste has immediate benefits: it cuts down the arrival of new plastics and discourages unnecessary production. Yet, the challenge remains in changing consumer behaviors and inspiring commitment to sustainable habits, which requires collaboration between businesses, governments, and the public.
"In reducing plastic waste, we turn the tide from mere remediation to proactive stewardship of our environment."
In summary, recycling and sustainability efforts play an indispensable role in reshaping the future of plastic production. Emphasizing current recycling technologies and sustainable practices, we can navigate the complexities of plastic's environmental impact and work toward a circular economy where waste is minimized, and resources are reused. Understanding these facets equips us with the insights needed to advocate for changes that prioritize both innovation and environmental welfare.
Future Prospects in Plastic Manufacturing
The realm of plastic manufacturing is on the cusp of significant transformation. As society becomes increasingly rattled by environmental concerns, the future of plastics is being scrutinized and reimagined. This article will explore the pivotal elements that lie ahead for this industry, focusing on innovations in material sourcing and the emergence of cutting-edge technologies. These prospects are not merely trends; they represent a paradigm shift in how plastics can be sustainable, economically viable, and environmentally conscious.
Innovations in Material Sourcing
As environmental issues take center stage, innovative material sourcing has emerged as one of the most critical areas for future development. Traditionally, plastic production relied heavily on fossil fuelsâprimarily petroleumâwhich has raised eyebrows globally due to pollution and global warming. However, there is an ongoing movement toward alternative sources of materials.
A notable trend is the use of bio-based plastics, made from renewable biomass like corn starch or sugarcane. These alternatives inherently reduce dependence on fossil fuels, boosting sustainability. Some companies are even exploring the potential of waste materials as feedstock. For instance, plastics can be derived from used cooking oil or agricultural waste, fostering a circular economy where refuse becomes raw material.
Moreover, advancements in synthetic biology offer exciting prospects. Researchers are experimenting with engineered microorganisms that produce plastic-like materials through fermentation. This creates the potential for plastics that degrade more easily, tackling the ever-pressing issue of plastic waste. As these innovations evolve, they promise not just to change the sourcing of materials but also to redefine the very notion of what plastic can be.
Emerging Technologies
Progress in technology can dramatically change the landscape of plastic manufacturing. Automation is already on the rise, with smart manufacturing systems that incorporate digitization and the Internet of Things (IoT). These systems enable manufacturers to streamline production processes, monitor efficiency, and reduce wasteâall critical factors for an industry under scrutiny for its environmental impact.
3D printing is another revolutionary technology making waves. This method allows for the creation of complex designs using only the necessary amount of material, drastically reducing scrap waste. Furthermore, as bio-based filaments are developed, the potential for creating items that are both functional and eco-friendly continues to grow.
Recycling technologies are also on the cutting edge of innovation. Chemical recycling processes capable of breaking down plastics into their original monomers can facilitate the reuse of materials in new products without quality loss. This contrasts with traditional mechanical recycling, which often degrades the material's quality. As these technologies develop, they could eliminate a significant portion of waste generated by plastic production, helping to address the environmental concerns surrounding this material's lifecycle.
"The evolution of plastic production is not just about manufacturing; it's about rethinking our relationship with materials and their lifecycle in society."
In summary, the future of plastic manufacturing holds exciting prospects. The innovations in material sourcing and emerging technologies signal a shift towards a more responsible industry. As these developments unfold, the potential for creating sustainable and environmentally friendly plastics seems more tangible than ever. Understanding these trends is essential for students, researchers, and professionals invested in creating a more sustainable future.