Understanding Teflon: Composition and Applications
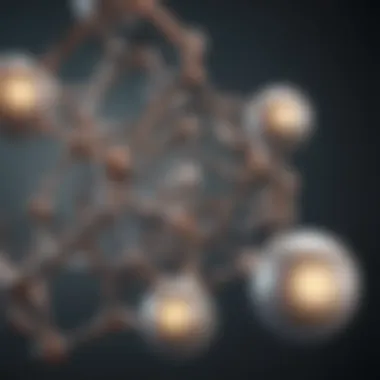
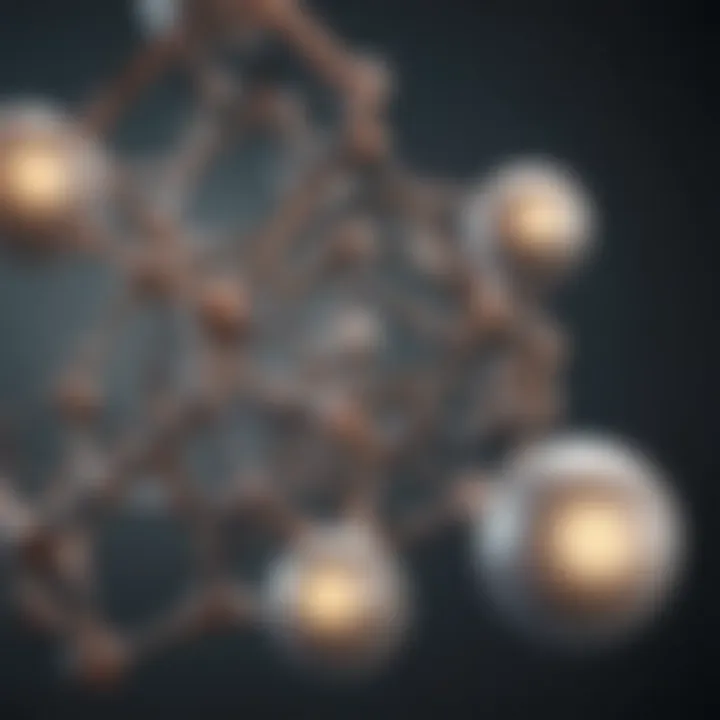
Intro
Research Overview
Summary of Key Findings
The exploration of Teflon's composition reveals several interesting aspects. The primary ingredient, tetrafluoroethylene, undergoes polymerization to create a long chain of carbon and fluorine atoms. This unique structure contributes to Teflon's non-stick and heat-resistant properties.
Here are some key components involved in Teflon's composition:
- Carbon Atoms: The backbone of PTFE, providing strength and stability.
- Fluorine Atoms: Essential for its non-reactive nature and resistance to high temperatures.
- Additives: Various additives enhance performance characteristics, such as durability and adhesion.
Significance of Research
Understanding Teflon's composition is vital for multiple reasons. As industries increasingly demand high-performance materials, insight into the molecular structure and properties of Teflon helps in engineering advanced solutions. Furthermore, the implications of Teflon’s environmental impact and safety are significant. With increasing regulations and safety standards, knowing the composition assists in evaluating risks associated with its use.
Methodology
Research Design
The research into Teflon's composition combines theoretical studies and practical applications. This dual approach allows for a comprehensive examination of the material at both the molecular level and its broader implications in real-world applications.
Data Collection Methods
Various methods are employed to analyze Teflon's composition:
- Spectroscopy: Techniques such as FTIR (Fourier Transform Infrared Spectroscopy) help identify chemical bonds.
- Chromatography: Used to separate and analyze components within Teflon.
- Industry Reports: Sourcing data from manufacturers provides insights into applications and safety assessments.
Understanding the chemical structure and its implications contributes to safer and more effective use of Teflon in varied fields.
In summary, the composition of Teflon is embedded in its structure and properties. This foundational knowledge is essential for future innovation and safety assessments in the material science field.
Intro to Teflon
Teflon, known scientifically as polytetrafluoroethylene (PTFE), plays a crucial role in various industries and applications. Its remarkable properties, such as non-stick surfaces and resistance to heat and chemicals, make it a preferred choice in many settings. Understanding Teflon is essential not only for professionals in material science but also for industries relying on its advantages. Here, we delve into the significance of Teflon's composition, historical context, and its current applications.
Historical Context
Teflon was discovered in 1938 by Dr. Roy Plunkett while he was conducting research for a refrigerant. The accidental creation of the material which was leftover in a pressurized container, led to an era of exploration in fluoropolymers. In the mid-20th century, its unique properties garnered attention from the military and aerospace sectors, leading to broader applications.
By the 1960s, Teflon gained popularity in household products, particularly non-stick cookware. Companies like DuPont, which marketed Teflon, helped establish the material as a household name. Its historical significance lies in its transformative impact on cooking, as it introduced a new standard in food preparation. Today, Teflon is seen not just as a mere product but a game-changer in manufacturing processes.
Teflon in Modern Applications
In contemporary contexts, Teflon's versatility extends beyond the kitchen. It is utilized in various spheres, including:
- Aerospace: Teflon is used for insulation on wiring and tubing, ensuring safety in aircraft.
- Automotive: It enhances performance in engines through its ability to withstand high temperatures.
- Medical Devices: Its chemical resistance makes it suitable for implants and surgical instruments.
This adaptability leads to numerous benefits, such as improving durability and reducing friction. The continued research into Teflon aims to maximize its potential, creating innovative solutions that address modern challenges. Whether in everyday items or specialized equipment, Teflon remains integral in diverse applications.
Chemical Composition of Teflon
The chemical composition of Teflon is fundamental to understanding its unique properties and applications. Teflon, known chemically as polytetrafluoroethylene (PTFE), is a fluoropolymer characterized by its non-stick qualities and remarkable chemical resistance. This section will explore the composition in detail, the benefits it brings, and considerations for its use.
Basics of Polytetrafluoroethylene (PTFE)
Polytetrafluoroethylene is a polymer that consists of repeated units of tetrafluoroethylene. The presence of fluorine atoms is key to Teflon's non-reactivity and low friction. The polymerization process of PTFE involves the free radical polymerization of tetrafluoroethylene gas. This creates long chains of carbon atoms with fluorine attached, resulting in a highly stable structure.
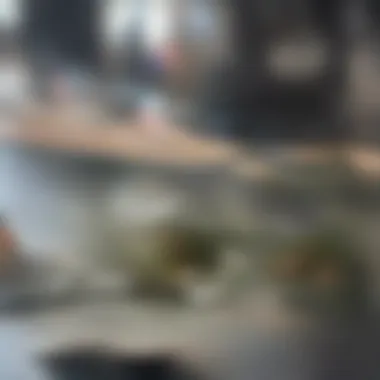
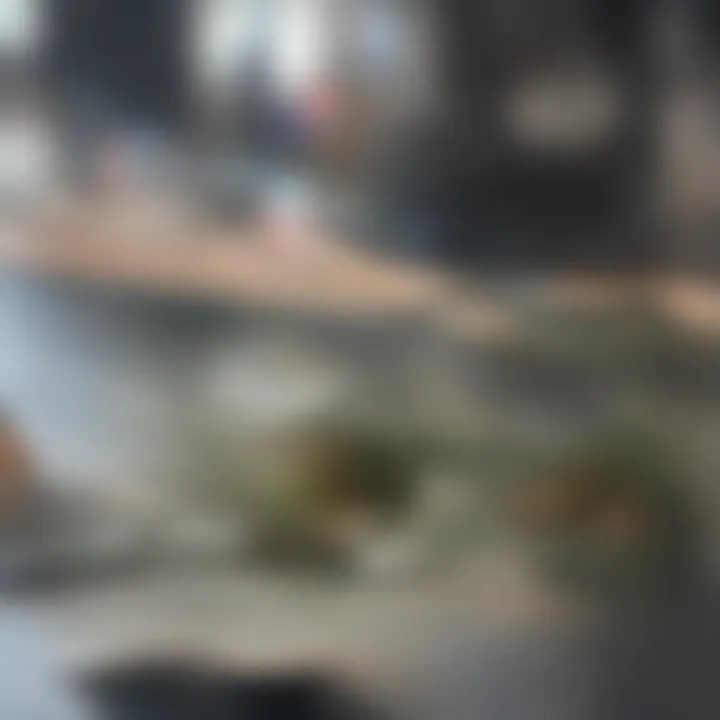
PTFE's stability is one of its greatest advantages. It can withstand high temperatures and harsh chemicals. Compared to other materials, PTFE exhibits superior performance, particularly in environments where chemical exposure is inevitable. This makes it ideal for a wide range of applications, from cookware to industrial coatings.
Molecular Structure
The molecular structure of Teflon influences its characteristics significantly. At the atomic level, PTFE is composed of carbon-carbon and carbon-fluorine bonds. The fluorine atoms envelop the carbon backbone, creating a barrier that repels other substances. As a result, Teflon does not adhere to most other materials, maintaining its surface integrity even under strain.
The structural configuration defines several properties:
- Low surface energy leads to its non-stick properties.
- High thermal stability allows it to function effectively at elevated temperatures, typically up to 260°C.
- Chemical inertness means it does not react with many substances, preventing degradation.
Understanding this molecular configuration is essential for material scientists who seek to develop new applications for Teflon and similar compounds.
Other Fluoropolymers
In addition to PTFE, there are various other fluoropolymers with similar characteristics but differing chemical structures. Examples include perfluoroalkoxy (PFA) and fluorinated ethylene propylene (FEP). These materials share some qualities with Teflon but may offer improved performance in specific applications.
- PFA: Often used in applications requiring more flexibility than PTFE provides.
- FEP: Has a lower melting point, making it easier to process while maintaining good chemical resistance.
These alternatives highlight the versatility of fluoropolymer chemistry and its significance in various industries. Understanding the distinctions between these compounds is vital for making informed decisions in material selection and application.
To summarize: The composition of Teflon, particularly the role of PTFE, defines its unique properties and extensive use in different fields. Knowledge of molecular structure and other fluoropolymers will enhance our insights into material science.
This exploration into Teflon's chemical composition establishes a foundation for understanding its advantages, applications, and the considerations necessary for appropriate use.
Manufacturing Process of Teflon
The manufacturing process of Teflon is a critical topic in understanding its composition and functionality. Teflon, primarily composed of polytetrafluoroethylene (PTFE), is renowned for its unique properties such as non-stick characteristics and exceptional thermal stability. Each phase of production plays a significant role in these attributes, thereby affecting the final product's quality.
Polymerization Techniques
Polymerization is the core technique used in creating Teflon. This process involves chemical reactions that join monomers into a long chain, forming polymers. Several methods can be employed for PTFE polymerization, including free radical polymerization. This requires careful control of reaction conditions to ensure optimal results. The techniques can be grouped mainly into two categories: suspension polymerization and emulsion polymerization.
- Suspension Polymerization: In this process, PTFE particles are formed in a heterogenous system. It allows for better control over the molecular weight and distribution.
- Emulsion Polymerization: This method utilizes surfactants to stabilize the latex particles, leading to a different molecular structure of PTFE, often impacting its physical properties.
These methods affect the overall properties of Teflon, including its melt flow characteristics and mechanical strength. The careful selection of polymerization technique based on desired applications is essential for achieving specific performance traits.
Production Methods
Production methods also significantly influence the large-scale manufacturing of Teflon. After polymerization, the resulting PTFE is usually processed into various forms including powders, granular forms, or coatings. The main production steps include:
- Milling: The polymer is milled into fine powders, facilitating its incorporation into various products.
- Extrusion: This method is commonly used for creating films and sheets of Teflon. The milled powder is heated and forced through a die, shaping it into a specific form.
- Sintering: In this essential step, the extruded Teflon is heated to a temperature where it begins to flow but below its melting point. This process enhances bonding between PTFE particles, improving overall strength.
Each production method not only dictates the shapes and sizes of Teflon products but influences their performance in various environments.
Quality Control Measures
Quality control measures are paramount in the Teflon manufacturing process. Ensuring that products meet specific performance specifications requires rigorous testing of both the raw materials and the finished products. Several methods are employed:
- Physical Testing: This includes tests for tensile strength, elongation, and thermal stability. Such measures determine how Teflon will perform under stress or temperature variations.
- Chemical Testing: Analyzing the resistance of Teflon to various chemicals is essential, especially given its applications in corrosive environments.
- Visual Inspection: Final products are visually inspected for consistency in quality, surface finishes, and absence of defects.
These strict quality control measures help in maintaining the reputation of Teflon as a high-performance material, ensuring that it meets the stringent requirements needed across its various applications.
"The focus on meticulous quality checks distinguishes Teflon products from others, underpinning its reliability in demanding scenarios."
Through these comprehensive steps in manufacturing, Teflon retains its status as a material of choice across multiple industries.
Properties of Teflon
Understanding the properties of Teflon is crucial for grasping its place in both commercial and industrial applications. Teflon, primarily known for its non-stick characteristics, arises from its unique chemical makeup, which grants it exceptional qualities. This section focuses on two critical properties: thermal stability and chemical resistance. These properties make Teflon suitable for diverse uses, from kitchenware to modern manufacturing processes.
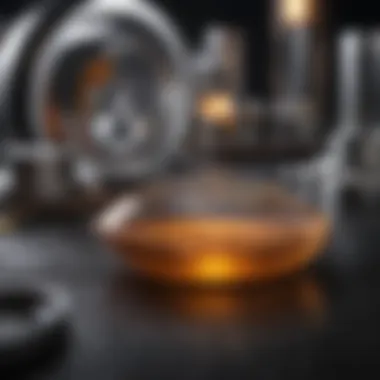

Thermal Stability
Thermal stability is one of Teflon's standout features. It can withstand high temperatures without degrading. Typically, Teflon can tolerate temperatures up to 260 degrees Celsius (500 degrees Fahrenheit) without losing its integrity. This stability is due to the strong carbon-fluorine bonds prevalent in its molecular structure. The robustness of these bonds means that Teflon retains its properties even when exposed to extreme heat, making it an ideal material for items like cookware and various industrial components where heat is a major factor.
However, it is noteworthy that while Teflon remains stable up to high temperatures, overheating can lead to the release of toxic fumes. Thus, understanding the limits of its thermal capacity is essential for safe use. In practical applications, this property allows Teflon to perform effectively in a variety of environments, including those subjected to high thermal cycles.
Chemical Resistance
The chemical resistance of Teflon is another integral aspect of its performance. It is impervious to many corrosive substances, including acids and bases. This resistance stems from the strong and stable chemical structure, which does not react easily with other materials. Teflon's ability to resist chemical degradation extends its usability in sectors such as pharmaceuticals and chemical processing, where harsh chemicals are commonplace.
Teflon’s unmatched chemical resistance allows it to maintain its properties in challenging environments, which has made it a go-to choice for many industrial applications.
Despite its strong resistance, it's important to note that certain highly reactive substances, like elemental fluorine or sodium, can still affect Teflon. Thus, careful consideration should be given regarding the specific chemicals with which Teflon may contact.
Applications of Teflon
Teflon is a versatile material with extensive applications across various sectors. Its unique properties, such as low friction, non-stick characteristics, and high chemical resistance, make it suitable for different uses. Understanding the applications of Teflon gives insight into its significance in everyday life and industry, as well as its broader implications for safety and sustainability.
Culinary Uses
Culinary applications of Teflon are widespread. It is primarily known for its use in non-stick cookware, which allows food to be cooked with minimal oil or fat. This feature not only lowers calories but also simplifies the cooking process. Teflon coatings can be found on frying pans, baking sheets, and various kitchen utensils.
The ease of cleaning Teflon-coated items is another advantage. Residues from food do not adhere strongly to the surface, making washing easy and less time-consuming. However, proper use and care are vital to maintaining the integrity of Teflon cookware. Avoiding metal utensils and high heat helps to protect the non-stick layer.
Industrial Applications
In industrial environments, Teflon is valued for its durability and resistance to extreme temperatures and chemicals. It is used in gaskets, seals, and bearings in machinery, ensuring smooth operation and longevity. The ability of Teflon to withstand corrosive substances means it finds use in chemical processing plants, where it helps protect equipment from wear and tear.
Moreover, Teflon is utilized in electrical insulation. Its high dielectric strength enables safe use in high-voltage applications. The automotive industry also benefits from Teflon in components such as fuel lines and wiring harnesses, as it minimizes friction and improves overall efficiency.
Medical Uses
In the medical field, Teflon is employed for its biocompatibility and stability. It can be found in surgical grafts and implants. Its non-reactive nature reduces the risk of complications when introduced to human tissues.
Furthermore, Teflon coatings are used in medical devices, enhancing their functionality and lifespan. However, ongoing research is necessary to fully understand the implications of Teflon in long-term medical applications.
Environmental Considerations
Understanding the environmental considerations surrounding Teflon is vital in today's context. As a popular material in various industries, Teflon's impact on ecosystems and waste management practices cannot be overlooked. These discussions are essential for researchers, students, and professionals who wish to comprehend the material’s lifecycle and its potential ramifications for our planet.
Impact on Ecosystems
The introduction of Teflon into the environment raises concerns mainly due to the chemical compounds involved in its production. When Teflon products, particularly those made from polytetrafluoroethylene (PTFE), are discarded, they can leach harmful substances.
Some major points to consider include:
- Chemical Persistence: Teflon is notably resistant to degradation. Its compounds, such as perfluoroalkyl substances (PFAS), can persist for many years in the environment. This resistance can lead to accumulation in soil and water systems, affecting living organisms.
- Aquatic Life: Studies indicate that these chemicals can infiltrate water resources, posing risks to aquatic ecosystems. Fish and other marine life are particularly vulnerable to the toxic effects of PCR substances, affecting their reproduction and survival rates.
- Food Chain Concerns: The accumulation of harmful substances in aquatic systems raises significant concern about bioaccumulation. When fish ingest these chemicals, they can enter the food chain, potentially affecting larger predators, including humans.
"The perpetual nature of PFAS compounds poses serious environmental and health implications."
Disposal Issues
Disposing of Teflon products poses considerable challenges and raises many questions regarding environmentally responsible practices. Some key points are:
- Recycling Difficulties: Unlike many common plastics, recycling Teflon is complex due to its unique chemical structure. Many recycling facilities lack the capability to process PTFE, causing it to end up in landfills.
- Incineration Concerns: Incinerating Teflon can release toxic gases, including hydrogen fluoride and carbonyl fluoride. These emissions can have adverse effects not just locally but also contribute to air pollution on a broader scale.
- Landfill Accumulation: Disposing of Teflon in landfills further contributes to the long-term environmental challenges associated with PFAS. The materials can leach into groundwater, posing risks to water quality and public health.
To mitigate these challenges, it is essential for industries and consumers alike to prioritize better practices, such as:
- Exploring alternative non-toxic materials for products.
- Participating in proper disposal and recycling programs.
- Advocating for stricter regulations on production and disposal of fluoropolymer products.
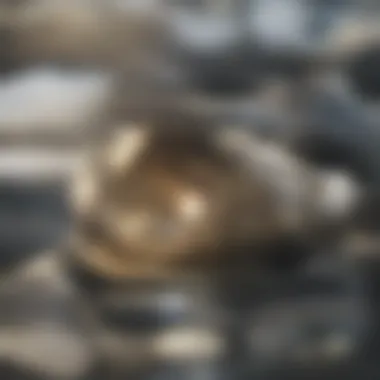
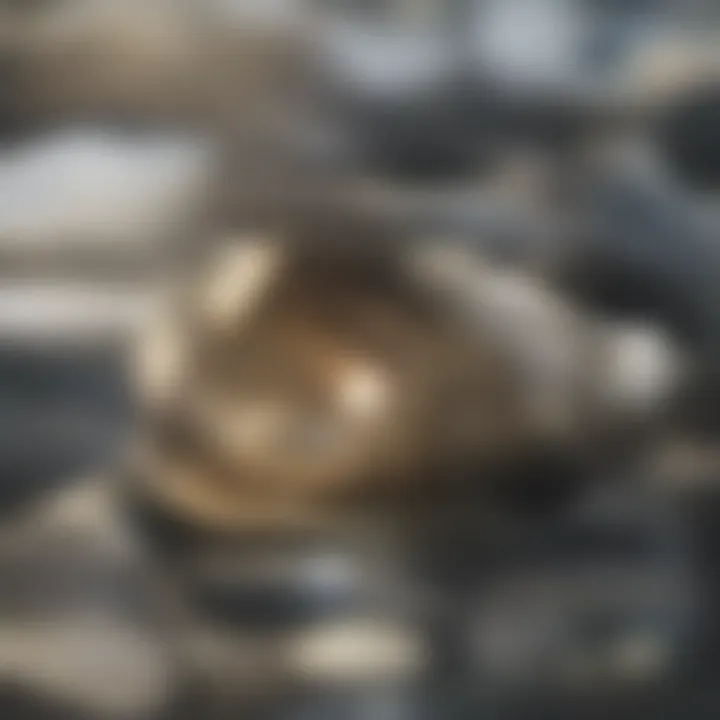
Ultimately, understanding the environmental considerations associated with Teflon is crucial in fostering more sustainable practices and policies. As the conversation around materials science and environmental responsibility grows, we must reflect on Teflon's wider implications and seek solutions that balance utility with ecological integrity.
Health Concerns Related to Teflon
The health concerns associated with Teflon are of significant importance in the modern discussion surrounding its uses and applications. Teflon, known chemically as polytetrafluoroethylene (PTFE), is a widely utilized material in various industries. However, its production and degradation can lead to potential chemical exposures that raise questions about long-term health effects. Understanding these concerns requires a look into the chemicals involved in Teflon's manufacture and the regulatory environment governing its use.
Chemical Exposure
Chemical exposure to compounds released from Teflon has garnered attention in health discussions. One critical compound has been perfluorooctanoic acid (PFOA), once used in Teflon production. PFOA is linked to several health issues, including liver damage and developmental problems. Its persistence in the environment and human body has prompted many to examine its impact carefully.
Research has indicated that while PTFE itself is considered stable and non-toxic at high temperatures, the by-products of its degradation can be toxic. Notably, prolonged heating of Teflon pans can lead to the release of fumes that may cause flu-like symptoms in humans. This condition is often referred to as polymer fume fever, emphasizing the need for proper use and ventilation during cooking.
Regulatory Framework
The regulatory framework for Teflon focuses on minimizing health risks associated with chemical exposure. Agencies, such as the Environmental Protection Agency (EPA) in the United States, have established guidelines for the use and disposal of PFOA and related compounds. In 2015, the EPA proposed action to phase out the use of PFOA, recognizing its hazardous nature and potential health risks.
Internationally, regulations are becoming stricter regarding the production and use of fluorinated compounds. Many countries are raising the standards for allowable levels of PFOA in drinking water and food products, aiming to protect public health. Manufacturers are encouraged to adopt alternative chemicals in production processes to reduce dependency on harmful substances.
In summary, while Teflon itself remains a valuable material, awareness of chemical exposure and adherence to the regulatory framework are essential. Educating users about safe practices can help mitigate health risks.
Understanding potential health implications is crucial for both consumers and manufacturers as we navigate the complexities surrounding Teflon.
Future Directions for Teflon Research
The exploration of Teflon, specifically its composition and applications, has reached critical junctures in recent years. Future directions for Teflon research are essential, not only for enhancing the utility of this material but also for addressing evolving environmental and health concerns. As industries continue to expand their reliance on fluoropolymers, a focus on sustainable and innovative practices becomes increasingly necessary.
Innovations in Material Science
Material science stands on the brink of breakthrough innovations. Research in this domain involves enhancing the properties of Teflon while minimizing potential downsides. Here are key areas of focus:
- Improved Performance: Research aims at developing Teflon with superior thermal and mechanical properties. Innovations in polymer formulations can lead to enhanced durability, making products last longer and reducing waste.
- Functionalization Techniques: By integrating other elements or compounds into Teflon, scientists can create materials with tailored characteristics. This includes increased adhesion properties, which can expand its applications beyond traditional uses.
- Nanotechnology: Utilizing nanotechnology may provide solutions for creating even lighter and stronger Teflon formulations. By manipulating materials at the molecular level, researchers can achieve desired characteristics while maintaining low production costs.
- Smart Materials: The incorporation of smart technologies into Teflon-based products represents a significant frontier. These materials could respond to environmental changes like temperature or humidity, enhancing their versatility in various applications.
Such focused research not only paves the way for advanced Teflon products but also influences competitive markets.
Sustainable Alternatives
The demand for sustainability influences Teflon research significantly. The production of traditional Teflon, particularly PTFE, raises environmental concerns due to potential pollution during manufacturing. Consequently, scientists are exploring sustainable alternatives:
- Biodegradable Polymers: Research is exploring bio-based alternatives that resemble Teflon's properties but are more environmentally friendly. For instance, using natural fibers or biopolymers can create coatings that possess desirable non-stick properties while being less harmful to the environment.
- Reduced Toxicity: Innovators are investigating methods to produce fluoropolymers with lower toxicity. Minimizing harmful byproducts can alleviate some environmental risks associated with Teflon.
- Life Cycle Assessment: Assessing the full life cycle of Teflon products promotes sustainability. This includes studying the energy use, resource consumption, and waste generation throughout the product’s life, aiming to refine processes for better outcomes.
Researchers in these areas understand that advancing Teflon technology is about balancing performance with responsibility. The creation of sustainable alternatives signifies a commitment to environmental stewardship while still delivering effective solutions for various industries.
"As we advance the science of materials like Teflon, our goal must be to innovate responsibly, merging performance with sustainability."
Ongoing research promises to yield significant advancements in Teflon's applications while minimizing environmental impact, ensuring that this material continues to meet the needs of future generations.
Closure
The exploration of Teflon's composition is critical in understanding its broad implications in various fields. This section synthesizes the key findings, emphasizing the material's unique attributes, manufacturing methods, and environmental considerations. It articulates how these elements converge to highlight Teflon's significance in both practical applications and ongoing research.
Summary of Findings
Throughout this article, we have examined several key aspects related to Teflon.
- Chemical Composition: Teflon, primarily made from polytetrafluoroethylene (PTFE), exhibits exceptional thermal stability and chemical resistance due to its molecular structure. These features have made it a valuable material in diverse sectors.
- Manufacturing Process: The production techniques for Teflon, particularly polymerization methods, are pivotal in determining its properties. Advances in production help optimize quality and sustainability.
- Applications Across Domains: Teflon is ubiquitous in culinary tools, industrial machinery, and even medical devices. Its non-stick properties are especially valued in kitchens, enhancing user experience and cooking efficiency.
- Environmental and Health Concerns: Understanding the impact of Teflon on ecosystems and potential health risks associated with chemical exposure is essential as regulatory frameworks evolve.
This holistic exploration lays a foundation for future inquiries into material applications and environmental safety.
Final Thoughts
As Teflon continues to play a relevant role in material science, ongoing research is necessary. Scholars and professionals must remain aware of both its benefits and challenges, particularly regarding sustainability. The evolution of Teflon research will likely focus on developing safer, more environmentally friendly alternatives while maintaining its advantageous properties. This balance is crucial not only for scientific advancement but also for societal well-being.
"Understanding material composition is vital for innovation and sustainability."
In summary, comprehending Teflon's intricate composition is not just an academic exercise; it is an opportunity to foster advancements that resonate in everyday life and industry. By addressing these elements, we create pathways for informed decisions that impact our future.